The speed of a ball mill plays a critical role in determining its grinding efficiency and overall performance. At low speeds, the grinding balls slide or roll over each other, resulting in minimal size reduction. At excessively high speeds, centrifugal force causes the balls to stick to the cylinder wall, preventing effective grinding. However, at an optimal speed, the balls are lifted to a certain height and then cascade down, creating a powerful impact and friction that maximizes size reduction. The speed must be carefully balanced with other factors such as ball size, material properties, and filling ratio to achieve the best grinding performance.
Key Points Explained:
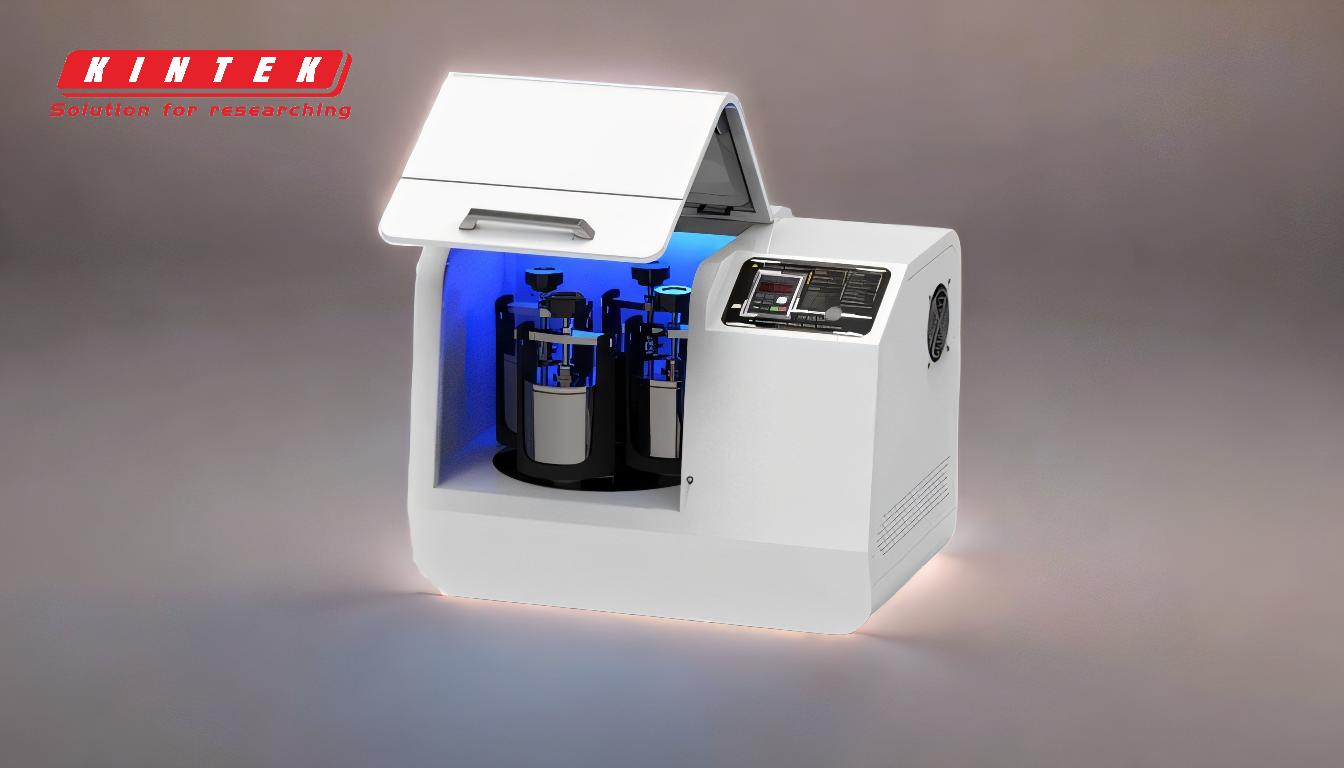
-
Impact of Speed on Grinding Mechanics:
- Low Speed: At low rotational speeds, the balls in the mill slide or roll over each other without significant lifting. This results in minimal grinding action, as the balls do not gain enough energy to break down the material effectively.
- High Speed: When the speed is too high, centrifugal force overcomes gravity, causing the balls to stick to the cylinder wall. This prevents the balls from cascading and grinding the material, leading to inefficient milling.
- Optimal Speed: At the right speed, the balls are lifted to the top of the mill and then cascade down in a parabolic trajectory. This creates a combination of impact and friction forces that maximize size reduction.
-
Factors Influencing Optimal Speed:
- Mill Diameter and Length: The size of the mill, particularly the drum diameter and the length-to-diameter ratio (L:D), affects the optimal speed. A well-balanced L:D ratio (typically 1.56–1.64) ensures efficient grinding.
- Ball Size and Density: Larger or denser balls require higher speeds to achieve the same cascading effect, while smaller or lighter balls may need lower speeds.
- Material Properties: The hardness, size, and type of material being ground influence the required speed. Harder materials may need higher speeds to achieve effective grinding.
- Filling Ratio: The percentage of the mill volume filled with grinding balls (filling ratio) impacts the optimal speed. Overfilling or underfilling the mill can reduce grinding efficiency.
-
Interaction with Other Grinding Parameters:
- Residence Time: The time the material spends in the mill chamber is influenced by the speed. Faster speeds may reduce residence time, while slower speeds can increase it.
- Feed Rate and Level: The rate at which material is fed into the mill and the level of material in the vessel must be balanced with the speed to ensure consistent grinding.
- Armor Surface Shape: The shape of the mill's interior surface (armor) can affect how the balls cascade and interact with the material, influencing the optimal speed.
-
Practical Implications for Equipment Purchasers:
- Speed Control: Purchasers should ensure the mill has adjustable speed settings to optimize performance for different materials and grinding requirements.
- Energy Efficiency: Operating at the optimal speed reduces energy consumption while maximizing grinding efficiency, leading to cost savings.
- Maintenance Considerations: High speeds can increase wear and tear on the mill and grinding balls, so purchasers should consider the durability of materials used in construction.
-
Optimization Strategies:
- Trial and Testing: Conducting trials at different speeds with the specific material to be ground can help determine the optimal operating conditions.
- Monitoring and Adjustment: Regularly monitoring the grinding process and adjusting the speed as needed can maintain peak performance over time.
- Balancing Speed with Other Parameters: Speed should be balanced with factors like ball size, filling ratio, and feed rate to achieve the best results.
By understanding how speed affects ball mill performance and considering the interplay with other factors, purchasers can make informed decisions to optimize grinding efficiency and achieve their desired outcomes.
Summary Table:
Aspect | Details |
---|---|
Low Speed | Minimal grinding; balls slide or roll without significant lifting. |
High Speed | Centrifugal force causes balls to stick to walls, reducing grinding action. |
Optimal Speed | Balls cascade down, creating impact and friction for maximum size reduction. |
Key Factors | Mill size, ball size, material properties, filling ratio. |
Practical Implications | Adjustable speed, energy efficiency, and durability considerations. |
Optimization Strategies | Trial testing, monitoring, and balancing speed with other parameters. |
Ready to optimize your ball mill performance? Contact our experts today for tailored solutions!