A ball mill is a cylindrical grinding machine that uses steel balls or rods as grinding media to reduce the size of materials through impact and attrition. It operates by rotating a horizontally or vertically mounted cylinder, causing the grinding balls to collide with the material, breaking it down into finer particles. The efficiency of the ball mill depends on achieving a critical rotational speed, which ensures the balls cascade and impact the material effectively. Ball mills are widely used in industries like mining, ceramics, and pharmaceuticals for grinding materials into fine powders or slurries.
Key Points Explained:
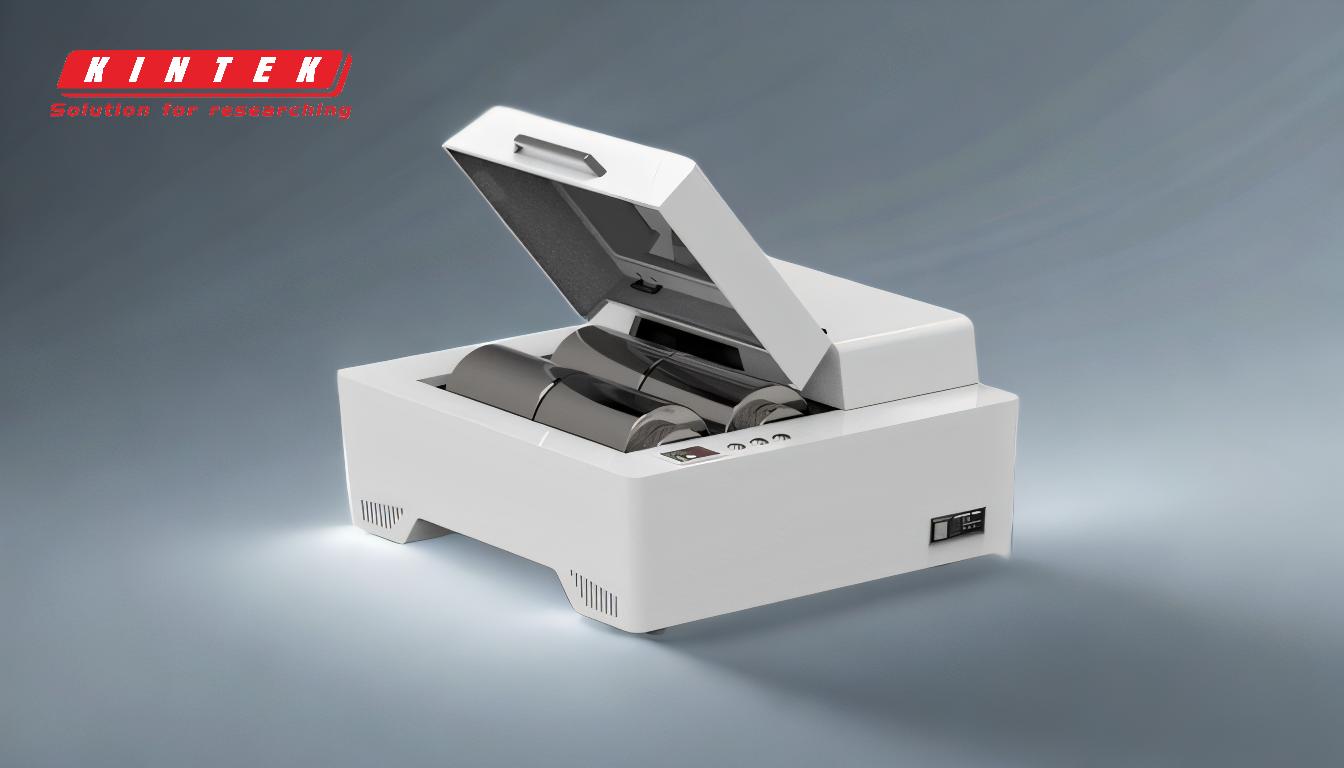
-
Structure and Components of a Ball Mill:
- A ball mill consists of a horizontally or vertically mounted rotating cylinder.
- The cylinder is typically made of metal and contains grinding media, such as steel balls or rods.
- The grinding media vary in size, with larger balls breaking down coarse materials and smaller balls reducing void spaces to produce finer particles.
-
Working Principle:
- The ball mill operates by rotating the cylinder, causing the grinding balls to move and collide with the material inside.
- Two primary mechanisms are involved: Impact (force from collisions) and Attrition (friction and grinding between particles).
- The rotation creates a cascading effect, where the balls lift and then fall, smashing into the material to break it down.
-
Critical Speed:
- The ball mill must achieve a critical rotational speed to ensure effective grinding.
- At this speed, the centrifugal force causes the grinding balls to rotate along the inner walls of the cylinder, maximizing impact and grinding efficiency.
- If the speed is too low, the balls will not cascade effectively, and if it is too high, the balls may stick to the walls due to excessive centrifugal force, reducing grinding efficiency.
-
Grinding Media:
- The grinding media (steel balls or rods) play a crucial role in the grinding process.
- Larger balls are used for coarse grinding, while smaller balls are used for fine grinding.
- The size and material of the grinding media are selected based on the properties of the material being ground and the desired fineness of the final product.
-
Applications:
- Ball mills are widely used in industries such as mining, ceramics, cement, and pharmaceuticals.
- They are suitable for grinding a variety of materials, including ores, chemicals, and pigments, into fine powders or slurries.
-
Advantages:
- Ball mills are versatile and can handle both wet and dry grinding processes.
- They are capable of producing very fine particles, making them ideal for applications requiring high precision.
- The design is relatively simple, and maintenance is straightforward.
-
Limitations:
- Ball mills can be noisy and generate significant heat during operation.
- They require a consistent feed rate to maintain efficiency, and overloading can reduce performance.
- The grinding media and lining of the cylinder may wear out over time, requiring replacement.
By understanding these key points, a purchaser can evaluate whether a ball mill is suitable for their specific grinding needs, considering factors such as material properties, desired particle size, and operational efficiency.
Summary Table:
Aspect | Details |
---|---|
Structure | Horizontal or vertical rotating cylinder with grinding media (steel balls/rods). |
Working Principle | Impact and attrition through cascading grinding balls. |
Critical Speed | Ensures effective grinding; too low or high reduces efficiency. |
Grinding Media | Steel balls/rods; size varies for coarse or fine grinding. |
Applications | Mining, ceramics, cement, pharmaceuticals; grinding ores, chemicals, etc. |
Advantages | Versatile, produces fine particles, simple design, easy maintenance. |
Limitations | Noisy, generates heat, requires consistent feed rate, media wear over time. |
Ready to optimize your grinding process? Contact us today to find the perfect ball mill for your needs!