Plasma in the sputtering process is created by applying a high voltage between the cathode (where the target material is placed) and the anode (typically the chamber wall or substrate connected to electrical ground). This voltage accelerates electrons from the cathode, which collide with neutral gas atoms (usually argon) in the chamber, causing ionization. The resulting plasma consists of ions, electrons, and neutral atoms in a dynamic equilibrium. The positive ions are then accelerated toward the negatively charged cathode, leading to high-energy collisions with the target material, which sputters atoms from the target onto the substrate.
Key Points Explained:
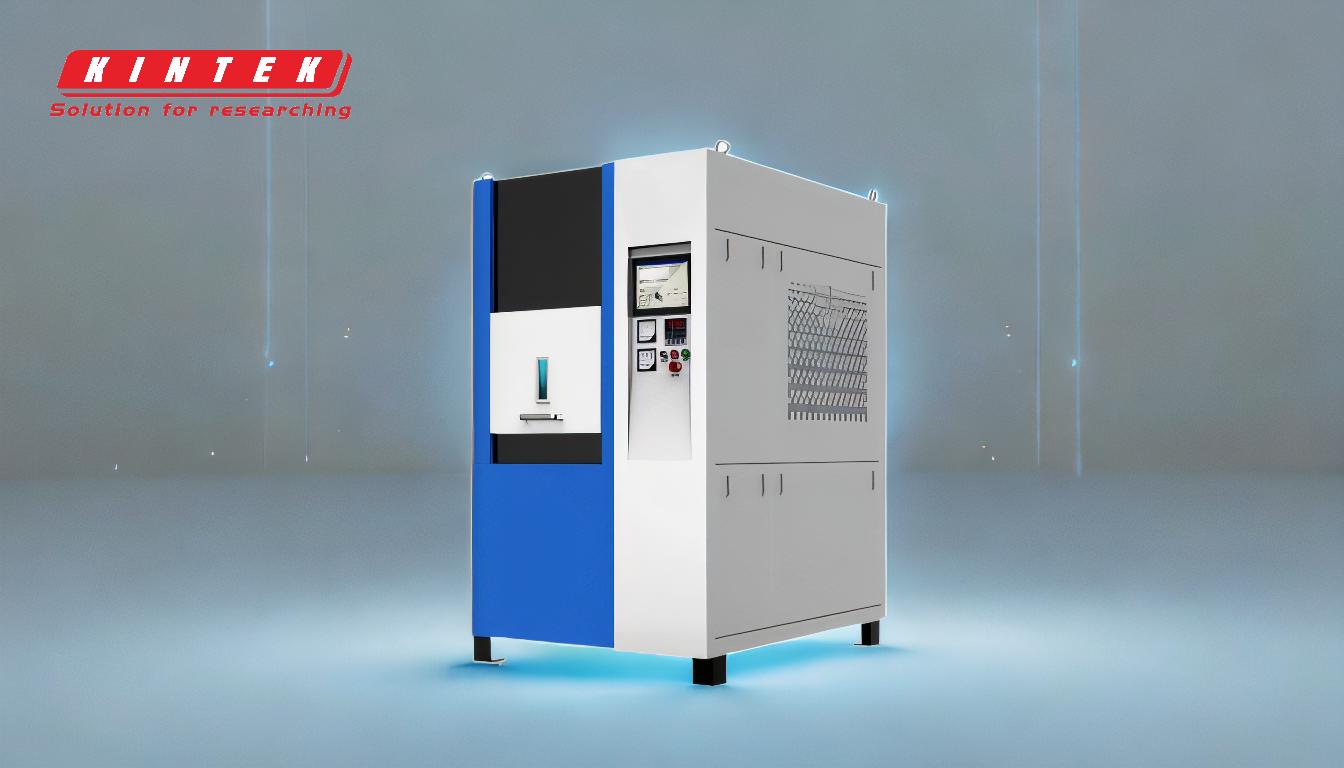
-
Application of High Voltage:
- A high voltage is applied between the cathode (target material) and the anode (chamber or substrate).
- This voltage creates an electric field that accelerates electrons away from the cathode.
-
Electron Acceleration and Collisions:
- The accelerated electrons collide with neutral gas atoms (typically argon) in the chamber.
- These collisions transfer energy to the gas atoms, causing ionization.
-
Ionization of Gas Atoms:
- Ionization occurs when electrons are stripped from neutral gas atoms, creating positively charged ions and free electrons.
- This process forms a plasma, which is a mixture of ions, electrons, and neutral atoms.
-
Formation of Plasma:
- The plasma is a dynamic environment where ions, electrons, and neutral atoms are in near equilibrium.
- The plasma is sustained by continuous energy input from the applied voltage.
-
Acceleration of Ions Toward Cathode:
- Positive ions in the plasma are attracted to the negatively charged cathode.
- These ions gain high kinetic energy as they accelerate toward the cathode.
-
High-Energy Collisions with Target Material:
- The high-energy ions collide with the target material, dislodging atoms from the target surface.
- This process is known as sputtering, and the dislodged atoms deposit onto the substrate to form a thin film.
-
Role of Noble Gas (Argon):
- Argon is commonly used as the sputtering gas due to its inert nature and ability to easily ionize.
- The gas is injected into the chamber and maintained at a specific pressure to sustain the plasma.
-
Use of DC or RF Voltage:
- DC voltage is typically used for conductive target materials.
- RF (radio frequency) voltage is used for insulating target materials to prevent charge buildup.
-
Vacuum Environment:
- The process occurs in a vacuum chamber to minimize contamination and control the gas pressure.
- The vacuum environment ensures that the plasma is stable and that the sputtered atoms travel unimpeded to the substrate.
By understanding these key points, one can appreciate the intricate process of plasma generation in sputtering and how it enables the precise deposition of thin films in various applications.
Summary Table:
Step | Description |
---|---|
High Voltage Application | A high voltage is applied between the cathode (target) and anode (chamber/substrate). |
Electron Acceleration | Electrons are accelerated, colliding with neutral gas atoms (argon) to cause ionization. |
Plasma Formation | Ionization creates a plasma of ions, electrons, and neutral atoms in dynamic equilibrium. |
Ion Acceleration | Positive ions are attracted to the negatively charged cathode, gaining high kinetic energy. |
Sputtering | High-energy ions collide with the target, dislodging atoms that deposit onto the substrate. |
Argon Gas Role | Argon is used for its inert nature and ease of ionization, maintaining plasma stability. |
DC/RF Voltage | DC voltage for conductive targets; RF voltage for insulating targets to prevent charge buildup. |
Vacuum Environment | A vacuum chamber minimizes contamination and ensures stable plasma and precise deposition. |
Ready to optimize your sputtering process? Contact our experts today for tailored solutions!