Ceramic fiber, a high-performance insulation material, is widely used in high-temperature applications due to its excellent thermal insulation properties and energy efficiency. Its lifespan can vary significantly depending on factors such as operating conditions, maintenance, and the specific application. Under ideal conditions, ceramic fiber blankets can last up to 12 years, but in more demanding environments, their lifespan may be reduced to just a few months. Key factors influencing durability include operating temperature, thermal stability, fiber diameter, and the frequency of maintenance. Understanding these factors is crucial for optimizing the lifespan of ceramic fiber in industrial applications.
Key Points Explained:
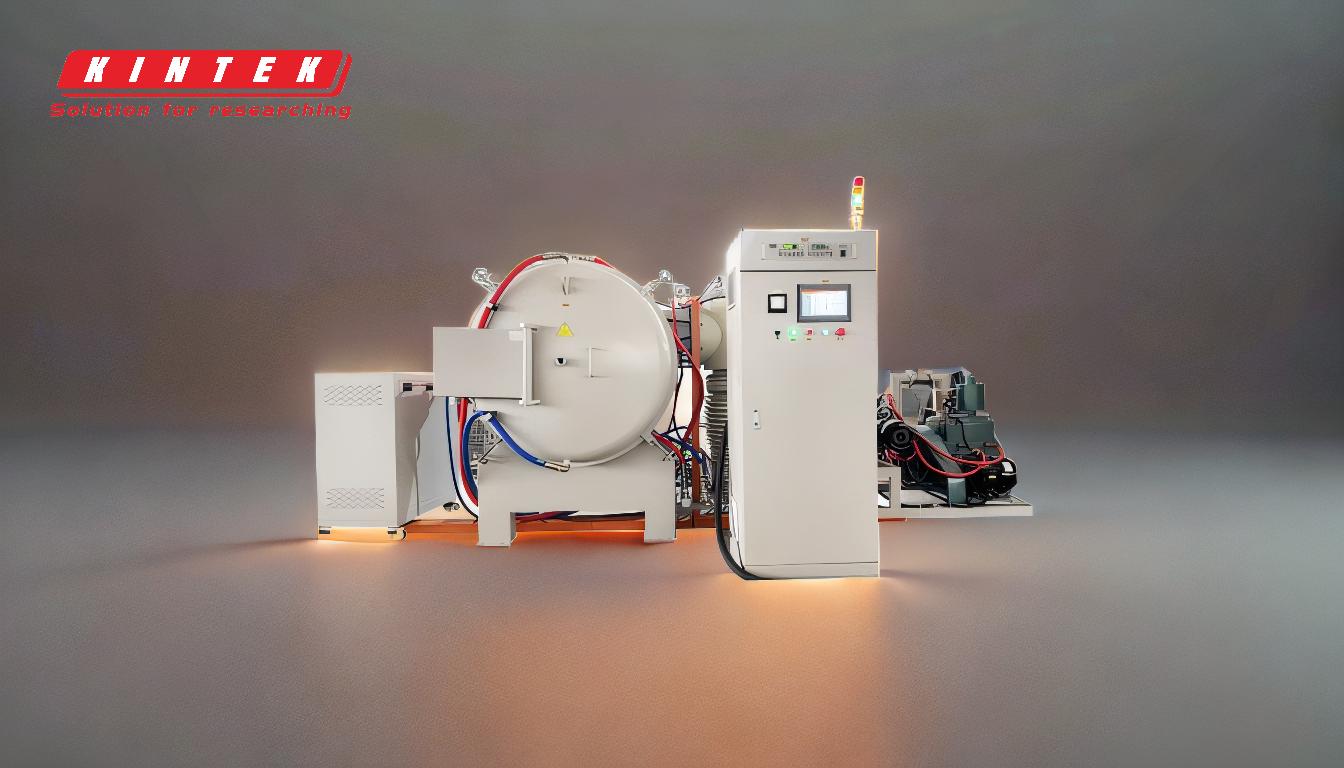
-
Operating Temperature:
- Ceramic fiber can withstand temperatures up to 1649 ℃, making it suitable for high-temperature environments like kilns and furnaces.
- Prolonged exposure to temperatures near the maximum limit can accelerate degradation, reducing the material's lifespan.
- Operating below the maximum temperature threshold can significantly extend the life of ceramic fiber.
-
Thermal Stability:
- Thermal stability is a critical performance indicator for ceramic fiber, often measured by line shrinkage at high temperatures.
- Higher thermal stability ensures minimal dimensional changes and maintains insulation efficiency over time.
- Frequent thermal cycling (heating and cooling) can cause stress on the fibers, leading to reduced lifespan.
-
Fiber Diameter:
- The fiber diameter typically ranges from 22-33 microns, influencing the material's strength and insulation properties.
- Thicker fibers may offer better durability under mechanical stress, while thinner fibers provide superior thermal insulation.
- The choice of fiber diameter should align with the specific application requirements to optimize lifespan.
-
Furnace Atmosphere and Watt Density:
- The furnace atmosphere (e.g., oxidizing, reducing, or neutral) can impact the chemical stability of ceramic fiber.
- High watt density (power per unit area) can lead to localized overheating, accelerating wear and tear.
- Proper selection of ceramic fiber type and watt density can mitigate these effects and extend lifespan.
-
Maintenance and Usage Patterns:
- Regular maintenance, such as inspecting for damage and replacing worn sections, can significantly extend the life of ceramic fiber.
- Continuous operation may lead to faster degradation compared to intermittent use, as the material is subjected to prolonged thermal stress.
- Proper installation and handling during maintenance are crucial to avoid mechanical damage.
-
Application-Specific Lifespan:
- In ideal conditions, ceramic fiber blankets can last up to 12 years, providing consistent thermal insulation.
- In more demanding applications, such as those involving aggressive chemical environments or rapid thermal cycling, the lifespan may be reduced to months.
- Understanding the specific demands of the application is essential for predicting and optimizing the lifespan of ceramic fiber.
-
Energy Efficiency and Heat Storage:
- Ceramic fiber's small heat storage characteristics contribute to its energy efficiency, reducing operational costs.
- Lower heat storage also minimizes thermal stress during heating and cooling cycles, potentially extending the material's lifespan.
- These properties make ceramic fiber a preferred choice for industries prioritizing energy savings and durability.
By considering these factors, equipment and consumable purchasers can make informed decisions about the selection, installation, and maintenance of ceramic fiber to maximize its lifespan and performance in their specific applications.
Summary Table:
Factor | Impact on Lifespan |
---|---|
Operating Temperature | Up to 1649 ℃; near-maximum exposure accelerates degradation. |
Thermal Stability | Higher stability minimizes shrinkage and stress from thermal cycling. |
Fiber Diameter | Thicker fibers resist mechanical stress; thinner fibers offer better insulation. |
Furnace Atmosphere | Chemical stability varies with oxidizing, reducing, or neutral environments. |
Watt Density | High density causes localized overheating, reducing lifespan. |
Maintenance | Regular inspections and proper handling extend lifespan. |
Usage Patterns | Intermittent use reduces thermal stress compared to continuous operation. |
Application | Lifespan ranges from months to 12 years, depending on environmental demands. |
Energy Efficiency | Low heat storage minimizes thermal stress and enhances energy savings. |
Optimize your ceramic fiber lifespan—contact our experts today for tailored solutions!