Sputtering is a versatile thin-film deposition technique used across various industries, including semiconductors, aerospace, and medical devices. It involves ejecting atoms from a solid target material onto a substrate to form a thin film. The process is categorized into several types based on the method of plasma generation, power supply, and application. The most common types include magnetron sputtering, ion beam sputtering, and diode sputtering. Magnetron sputtering, in particular, has subtypes such as Direct Current (DC) magnetron sputtering, Radio Frequency (RF) magnetron sputtering, and High Power Impulse Magnetron Sputtering (HIPIMS). Each type has unique characteristics and applications, making sputtering a highly adaptable and widely used technique.
Key Points Explained:
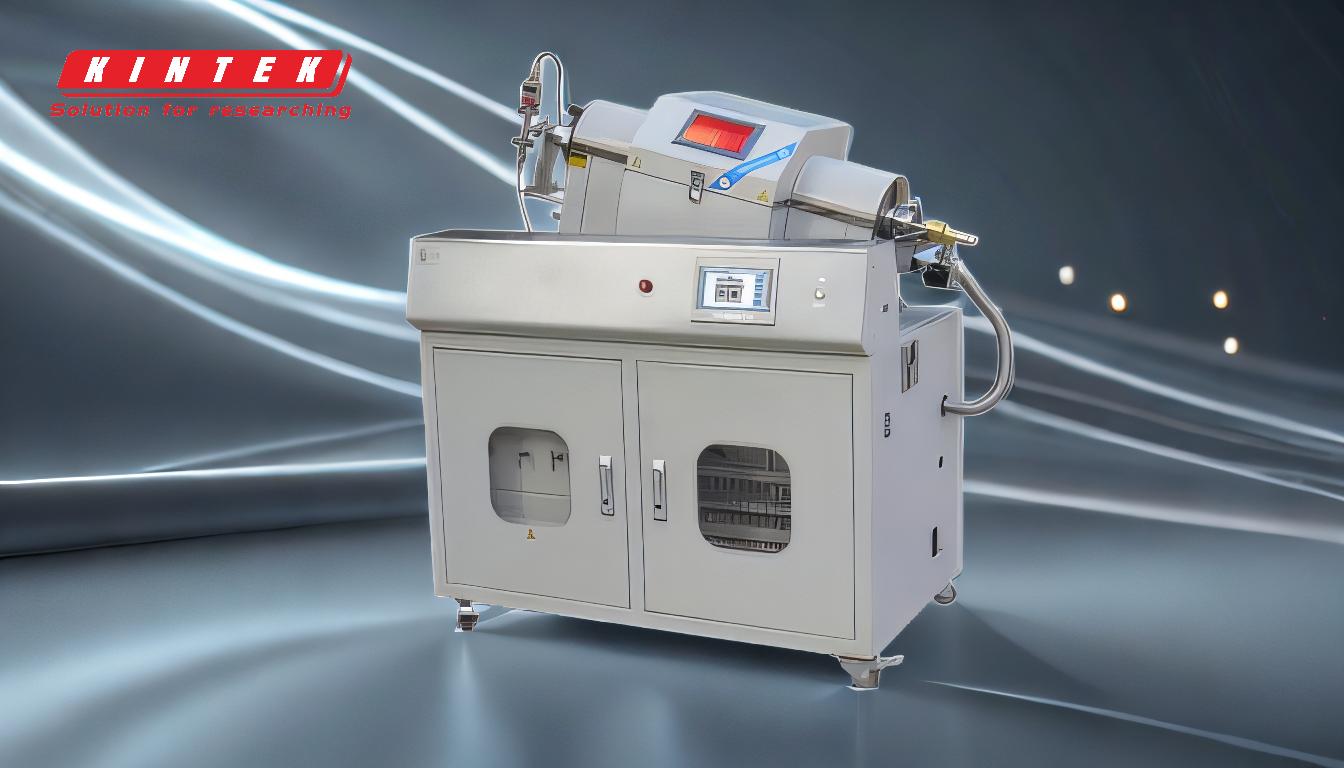
-
Overview of Sputtering:
- Sputtering is a physical vapor deposition (PVD) technique used to deposit thin films on substrates.
- The process involves bombarding a target material with ions, causing atoms to be ejected and deposited onto a substrate.
- It is widely used in industries such as semiconductors, aerospace, and medical devices due to its precision and versatility.
-
Types of Sputtering:
-
Magnetron Sputtering:
- This is the most common sputtering technique, characterized by the use of magnetic fields to enhance plasma generation.
- Subtypes include:
- Direct Current (DC) Magnetron Sputtering: Uses a DC power supply to generate plasma in a low-pressure gas environment. Ideal for conductive materials.
- Radio Frequency (RF) Magnetron Sputtering: Uses an RF power supply, making it suitable for insulating materials.
- High Power Impulse Magnetron Sputtering (HIPIMS): Uses high-power pulses to achieve high ionization rates, resulting in dense and high-quality films.
-
Ion Beam Sputtering:
- Involves directing a focused ion beam at the target material. This method offers precise control over the deposition process and is often used for high-precision applications.
-
Diode Sputtering:
- A simpler form of sputtering that uses a direct current between two electrodes. It is less efficient than magnetron sputtering but is still used in specific applications.
-
Magnetron Sputtering:
-
Applications of Sputtering:
- Semiconductor Industry: Used for depositing chemically resistant thin films and dielectric stacks.
- Aerospace and Defense: Applied for neutron radiography using gadolinium films.
- Medical Devices: Used to create gas-impermeable films for corrosion protection and electrical isolation in surgical tools.
-
Sputtering Process Steps:
- The sputtering process typically involves six key steps:
- Vacuuming the Chamber: The deposition chamber is evacuated to a pressure of around 10^-6 torr.
- Introducing Sputtering Gas: A sputtering gas, such as argon or xenon, is introduced into the chamber.
- Generating Plasma: Voltage is applied to generate a glow discharge between two electrodes.
- Ion Formation: Free electrons collide with sputtering gas atoms, forming positive ions.
- Ion Acceleration: Positive ions accelerate towards the cathode due to the applied voltage.
- Target Erosion and Deposition: Positive ions collide with the cathode, causing target atoms to be dislodged and deposited onto the substrate.
- The sputtering process typically involves six key steps:
-
Advantages of Different Sputtering Types:
- Magnetron Sputtering: High deposition rates, efficient use of target material, and suitability for a wide range of materials.
- Ion Beam Sputtering: High precision and control, ideal for high-quality thin films.
- Diode Sputtering: Simplicity and cost-effectiveness for less demanding applications.
-
Future Trends:
- The development of advanced sputtering techniques, such as HIPIMS, is driving improvements in film quality and deposition efficiency.
- Increasing adoption of sputtering in emerging fields like renewable energy and flexible electronics.
In conclusion, sputtering is a highly adaptable and widely used technique with various types tailored to specific applications. Understanding the differences between these types is crucial for selecting the right method for a given application.
Summary Table:
Type of Sputtering | Key Characteristics | Applications |
---|---|---|
Magnetron Sputtering | - Uses magnetic fields to enhance plasma generation | - High deposition rates, suitable for conductive and insulating materials |
DC Magnetron Sputtering | - Uses DC power supply for conductive materials | - Ideal for conductive thin films |
RF Magnetron Sputtering | - Uses RF power supply for insulating materials | - Suitable for dielectric and insulating films |
HIPIMS | - High-power pulses for dense, high-quality films | - Advanced applications requiring superior film quality |
Ion Beam Sputtering | - Focused ion beam for precise control | - High-precision applications, e.g., optical coatings |
Diode Sputtering | - Simple, direct current between electrodes | - Cost-effective for less demanding applications |
Interested in learning more about sputtering techniques? Contact our experts today for tailored solutions!