To determine the optimal number of balls to load into a ball mill, it is essential to consider the mill's volume and the efficiency of the milling process. The general rule is that the total volume of balls should not exceed 30–35% of the mill's internal volume. This ensures that the balls have enough space to move and interact with the material being milled, leading to effective grinding or mixing. Overloading the mill with balls can reduce efficiency, cause excessive wear, and potentially damage the equipment. The type of balls (e.g., stainless steel or rubber) and the material being processed also play a role in determining the optimal ball load.
Key Points Explained:
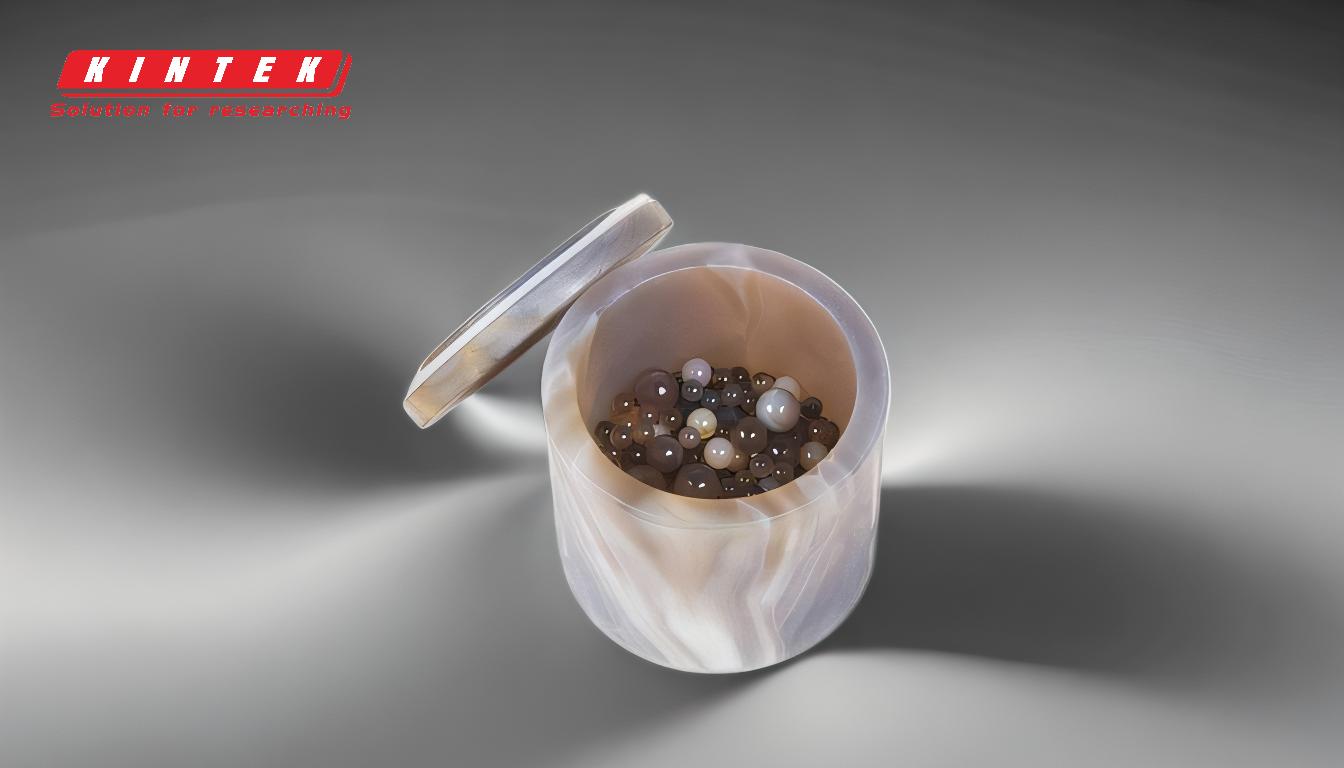
-
Ball Mill Volume and Ball Load Relationship:
- The ball mill operates by rotating a hollow cylindrical shell filled with grinding media (balls) and the material to be processed.
- The volume of balls loaded into the mill should not exceed 30–35% of the mill's total internal volume. This ensures proper movement and interaction of the balls with the material.
-
Efficiency of the Milling Process:
- Overloading the mill with balls can lead to inefficiency, as the balls may not have enough space to move freely. This can result in inadequate grinding or mixing.
- Underloading the mill can also reduce efficiency, as there may not be enough balls to effectively process the material.
-
Types of Balls and Their Impact:
- The type of balls used (e.g., stainless steel, rubber) can affect the milling process. For example, stainless steel balls are more durable and suitable for hard materials, while rubber balls are gentler and better for softer materials.
- The size and density of the balls also play a role in determining the optimal load. Larger or denser balls may require adjustments to the total volume to maintain efficiency.
-
Material Being Processed:
- The characteristics of the material being milled (e.g., hardness, particle size) influence the optimal ball load. Harder materials may require more balls or a higher ball density to achieve effective grinding.
- The desired final particle size or consistency of the material also affects the ball load. Finer grinding may require a higher ball load or longer milling time.
-
Practical Considerations:
- Regularly monitor the mill's performance and adjust the ball load as needed to maintain optimal efficiency.
- Consider the wear and tear on the balls and the mill itself. Overloading can lead to increased wear and potential damage to the equipment.
By adhering to these guidelines, you can ensure that your ball mill operates efficiently and effectively, producing the desired results while minimizing wear and tear on the equipment.
Summary Table:
Factor | Guideline |
---|---|
Ball Load Volume | Should not exceed 30–35% of the mill's internal volume. |
Efficiency Considerations | Overloading reduces efficiency; underloading limits material processing. |
Ball Types | Stainless steel for hard materials; rubber for softer materials. |
Material Characteristics | Harder materials may require more balls or higher density for effective grinding. |
Practical Tips | Monitor performance regularly and adjust ball load to maintain efficiency. |
Need help optimizing your ball mill? Contact our experts today for personalized advice!