The power consumption of a ball mill depends on several factors, including the size and type of the mill, the grinding media, the material being ground, and the operating conditions. Generally, ball mills are energy-intensive devices, with power usage ranging from a few kilowatts for small laboratory mills to several megawatts for large industrial mills. The energy efficiency of a ball mill is influenced by factors such as rotational speed, filling ratio, and the size and density of the grinding media. Understanding these variables is crucial for optimizing power usage and ensuring cost-effective operation.
Key Points Explained:
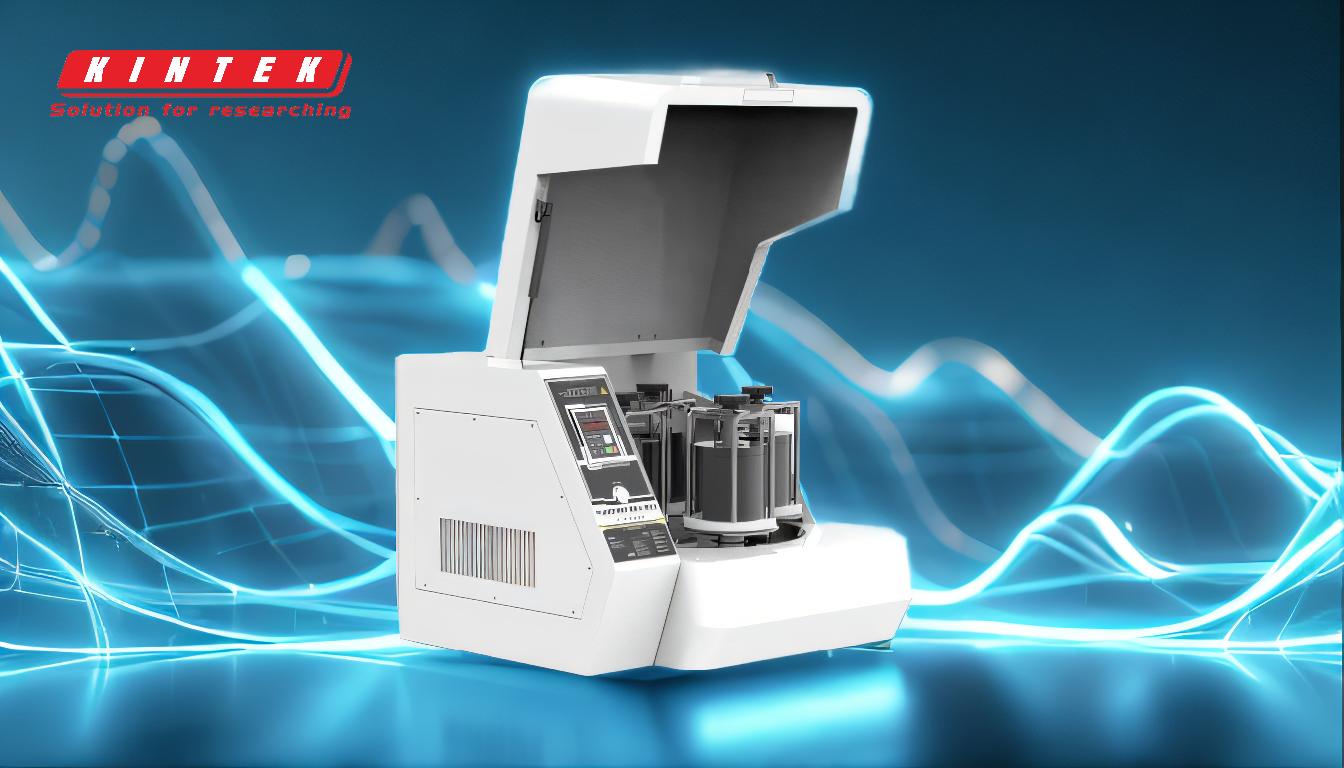
-
Factors Affecting Power Consumption
The power consumption of a ball mill is influenced by:- Mill Size and Type: Larger mills and those designed for industrial use consume more power than smaller, laboratory-scale mills.
- Grinding Media: The size, density, and material of the grinding media (e.g., steel balls) impact energy usage.
- Material Properties: The hardness, density, and feed size of the material being ground affect power requirements.
- Operating Conditions: Rotational speed, filling ratio (percentage of the mill volume filled with grinding media), and the design of the mill liner also play a role.
-
Typical Power Consumption Ranges
- Laboratory Ball Mills: These small-scale mills typically consume between 0.5 kW to 5 kW of power.
- Industrial Ball Mills: Larger mills used in mining or cement production can consume anywhere from 500 kW to 5 MW, depending on their size and capacity.
-
Energy Efficiency Considerations
- Optimizing Rotational Speed: Operating the mill at its critical speed (the speed at which the grinding media begins to centrifuge) maximizes efficiency.
- Filling Ratio: Maintaining an optimal filling ratio (usually between 30% to 50% of the mill volume) ensures effective grinding without excessive energy use.
- Grinding Media Size: Using appropriately sized grinding media reduces energy waste and improves grinding efficiency.
-
Calculating Power Consumption
The power consumption of a ball mill can be estimated using empirical formulas, such as: [ P = K \cdot D^{2.5} \cdot L \cdot n ] Where:- ( P ) = Power consumption (kW)
- ( K ) = Constant depending on mill type and operating conditions
- ( D ) = Mill diameter (meters)
- ( L ) = Mill length (meters)
- ( n ) = Rotational speed (rpm)
-
Practical Implications for Purchasers
- Cost Analysis: Understanding power consumption helps in estimating operational costs and selecting energy-efficient equipment.
- Sustainability: Lower power usage reduces the environmental impact and aligns with sustainability goals.
- Maintenance and Longevity: Efficient operation minimizes wear and tear, extending the lifespan of the mill and reducing maintenance costs.
By considering these factors, purchasers can make informed decisions about ball mill selection and operation, balancing performance, cost, and energy efficiency.
Summary Table:
Factor | Impact on Power Consumption |
---|---|
Mill Size and Type | Larger and industrial mills consume more power than smaller, laboratory-scale mills. |
Grinding Media | Size, density, and material of grinding media (e.g., steel balls) affect energy usage. |
Material Properties | Hardness, density, and feed size of the material influence power requirements. |
Operating Conditions | Rotational speed, filling ratio, and mill liner design play a role in energy efficiency. |
Power Consumption Range | Lab mills: 0.5 kW to 5 kW; Industrial mills: 500 kW to 5 MW. |
Energy Efficiency Tips | Optimize rotational speed, filling ratio (30%-50%), and grinding media size for better results. |
Need help selecting or optimizing a ball mill for energy efficiency? Contact our experts today!