The power consumption of a hammer mill depends on several factors, including the size of the mill, the type of material being processed, the desired output size, and the efficiency of the motor. Hammer mills typically range in power usage from 5 kW for small-scale operations to over 200 kW for industrial-scale mills. Understanding these variables is crucial for selecting the right hammer mill for your needs and ensuring energy-efficient operation. Below, we break down the key factors influencing power consumption and provide insights into optimizing energy usage.
Key Points Explained:
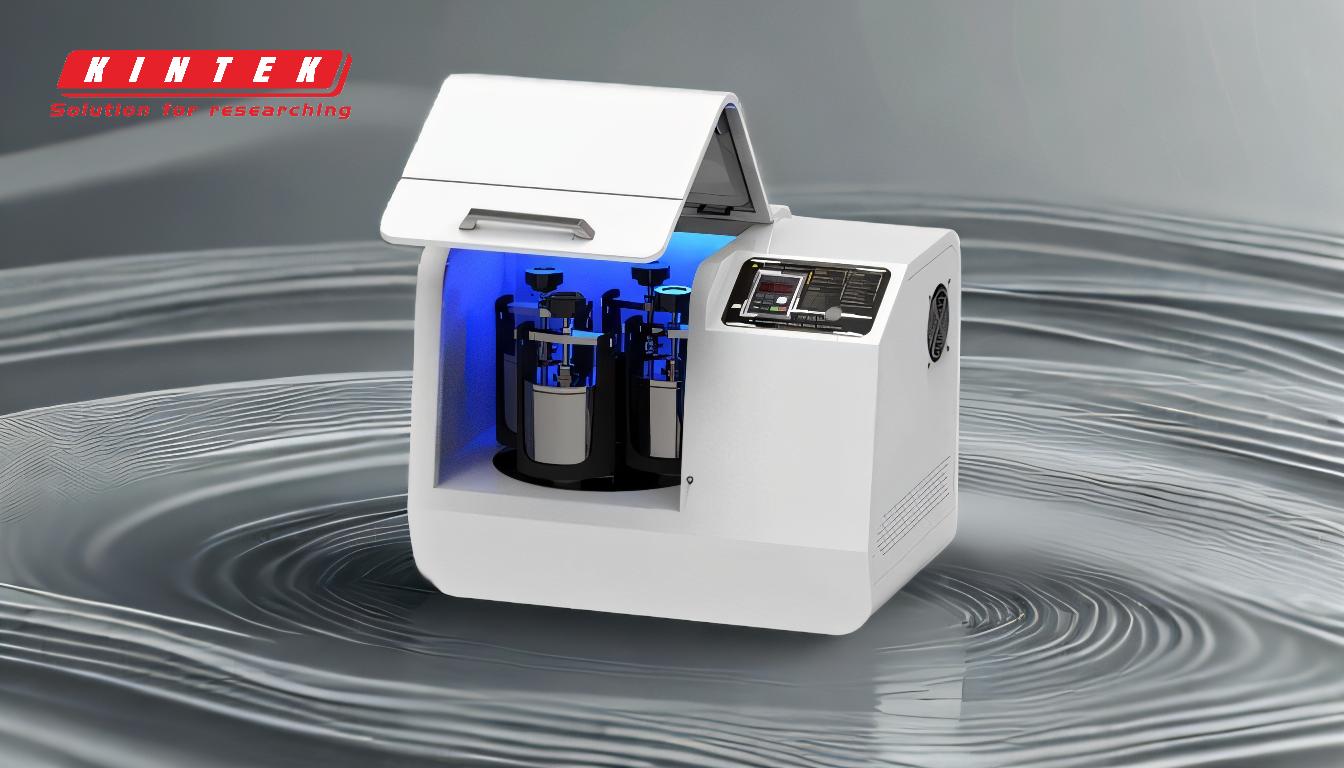
-
Factors Affecting Power Consumption
- Motor Size and Efficiency: The motor is the primary component determining power usage. Larger motors consume more power but are necessary for processing tougher materials or achieving higher throughput.
- Material Characteristics: Harder or denser materials (e.g., wood, metal, or stone) require more energy to grind compared to softer materials (e.g., grains or biomass).
- Screen Size and Output Fineness: Smaller screen sizes produce finer particles, which require more energy. Coarser grinding requires less power.
- Feed Rate and Consistency: Overloading the mill or feeding it inconsistently can increase power consumption. A steady, controlled feed rate optimizes energy use.
- Mill Design and Maintenance: Well-maintained mills with sharp hammers and properly aligned components operate more efficiently, reducing power usage.
-
Typical Power Ranges for Hammer Mills
- Small-Scale Mills: These mills, often used in laboratories or small farms, typically consume between 5 kW and 15 kW.
- Medium-Scale Mills: Used in small to medium-sized industries, these mills may require 15 kW to 75 kW.
- Large-Scale Industrial Mills: These high-capacity mills, used in large-scale manufacturing or processing plants, can consume anywhere from 75 kW to over 200 kW.
-
Calculating Power Requirements
-
Motor Power Formula: The power required by a hammer mill can be estimated using the formula:
[ P = \frac{Q \times E}{\eta} ]
Where:- ( P ) = Power (kW)
- ( Q ) = Feed rate (tons/hour)
- ( E ) = Specific energy consumption (kWh/ton)
- ( \eta ) = Motor efficiency (typically 0.8–0.95)
- Specific Energy Consumption: This varies based on material type and desired output size. For example, grinding wood may require 10–30 kWh/ton, while grinding grains may require 5–15 kWh/ton.
-
Motor Power Formula: The power required by a hammer mill can be estimated using the formula:
-
Energy Optimization Tips
- Choose the Right Mill: Select a hammer mill with a motor size that matches your material and throughput requirements. Oversized motors waste energy, while undersized motors strain the system.
- Regular Maintenance: Keep hammers sharp, screens clean, and bearings lubricated to reduce friction and energy loss.
- Optimize Feed Rate: Ensure a consistent and appropriate feed rate to avoid overloading or underloading the mill.
- Use Variable Frequency Drives (VFDs): VFDs allow you to adjust motor speed based on load, improving energy efficiency.
-
Environmental and Cost Considerations
- Energy Costs: Higher power consumption increases operational costs, so selecting an energy-efficient mill can significantly reduce expenses over time.
- Carbon Footprint: Energy-efficient mills contribute to lower greenhouse gas emissions, aligning with sustainability goals.
By understanding these factors and implementing energy-saving practices, you can optimize the power usage of your hammer mill, ensuring efficient and cost-effective operation.
Summary Table:
Factor | Impact on Power Consumption |
---|---|
Motor Size and Efficiency | Larger motors consume more power but are needed for tougher materials or higher throughput. |
Material Characteristics | Harder materials (e.g., wood, metal) require more energy than softer ones (e.g., grains). |
Screen Size and Output | Finer particles require more energy; coarser grinding uses less power. |
Feed Rate and Consistency | Inconsistent or overloaded feed rates increase power consumption. |
Mill Design and Maintenance | Well-maintained mills with sharp hammers and aligned components reduce energy loss. |
Typical Power Ranges | Small-Scale: 5–15 kW |
Ready to optimize your hammer mill's energy efficiency? Contact our experts today for tailored solutions!