The optimal volume to be filled in a ball mill typically ranges between 30% to 50% of the total mill volume. This range ensures efficient grinding by balancing the impact and attrition forces exerted by the grinding media (balls) on the material. Overfilling can reduce grinding efficiency due to insufficient space for the balls to cascade, while underfilling may lead to excessive wear and inadequate grinding. Factors such as the type of material, size of grinding media, and desired fineness of the product influence the ideal filling volume. Proper filling ensures effective energy transfer, maximizes throughput, and minimizes wear on the mill components.
Key Points Explained:
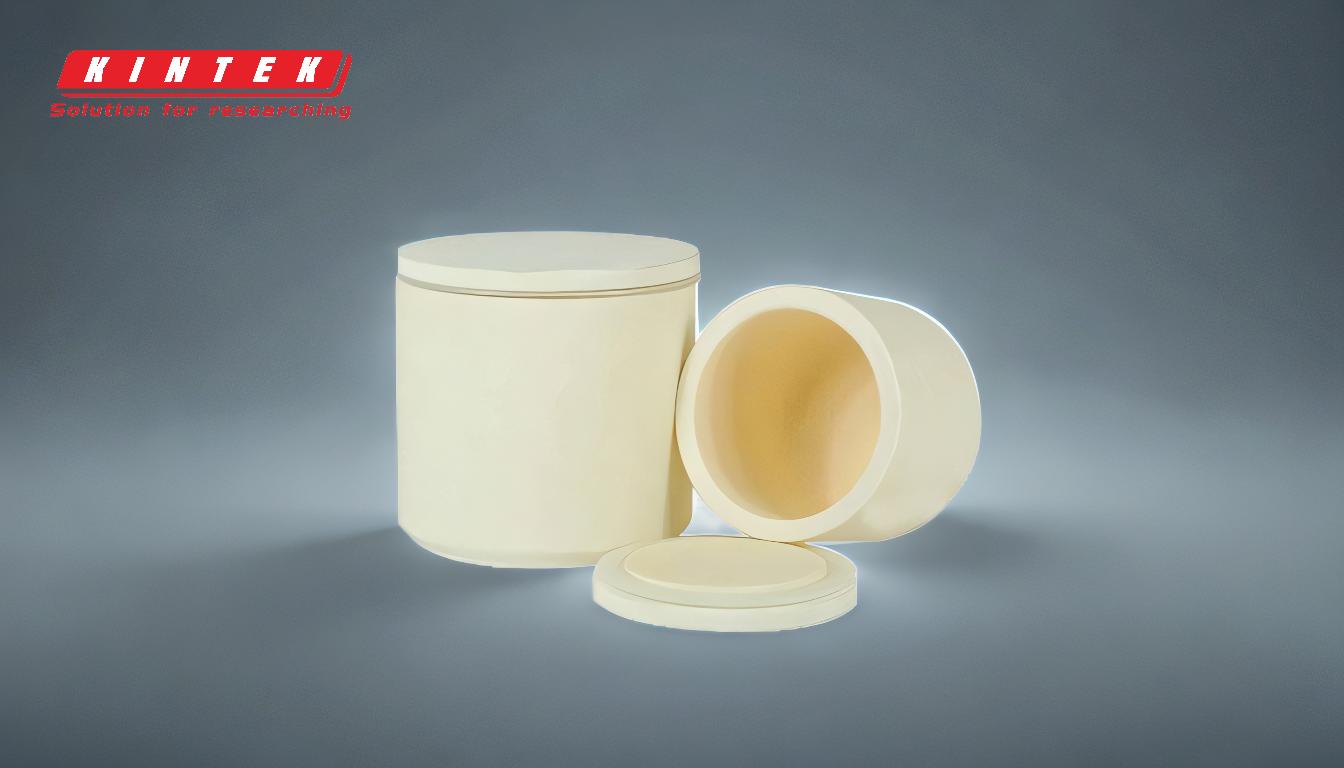
-
Optimal Filling Volume (30% to 50%):
- The ball mill should be filled to 30% to 50% of its total volume with grinding media (balls) and material. This range is widely accepted as optimal for most grinding operations.
-
Why this range?:
- 30% filling: Ensures sufficient space for the balls to cascade and impact the material effectively, promoting efficient grinding.
- 50% filling: Maximizes the grinding media's contact with the material, enhancing throughput without overloading the mill.
- Overfilling beyond 50% can lead to:
- Reduced grinding efficiency due to insufficient space for ball movement.
- Increased energy consumption as the mill works harder to rotate the overloaded charge.
- Underfilling below 30% can cause:
- Excessive wear on the mill lining and grinding media due to direct impact without material cushioning.
- Inadequate grinding due to insufficient material being processed.
-
Factors Influencing Filling Volume:
-
Material Properties:
- Hardness, density, and particle size of the material affect the grinding process. Harder materials may require a higher filling volume to achieve the desired fineness.
-
Grinding Media Size:
- Larger grinding media (balls) require a lower filling volume to ensure proper cascading and impact, while smaller media can accommodate a higher filling volume.
-
Mill Speed:
- The rotational speed of the mill (expressed as a percentage of critical speed) influences the optimal filling volume. Higher speeds may require a lower filling volume to prevent overloading.
-
Desired Product Fineness:
- Finer grinding typically requires a higher filling volume to increase the contact time between the material and grinding media.
-
Material Properties:
-
Importance of Proper Filling:
-
Efficient Energy Transfer:
- Proper filling ensures that the energy from the rotating mill is effectively transferred to the grinding media and material, maximizing grinding efficiency.
-
Minimized Wear and Tear:
- Adequate filling reduces direct impact between the grinding media and mill lining, extending the lifespan of both.
-
Consistent Throughput:
- Maintaining the optimal filling volume ensures a steady flow of material through the mill, preventing bottlenecks and ensuring consistent product quality.
-
Efficient Energy Transfer:
-
Practical Considerations:
-
Measurement Techniques:
- The filling volume can be measured using:
- Visual inspection: Observing the level of material and grinding media in the mill.
- Sound analysis: Monitoring the mill's operating sound, which changes with filling volume.
- Power draw: Measuring the mill's power consumption, which correlates with filling volume.
- The filling volume can be measured using:
-
Adjustments:
- If the mill is underperforming, adjustments can be made by:
- Adding or removing grinding media.
- Adjusting the feed rate of material to maintain the optimal filling volume.
- If the mill is underperforming, adjustments can be made by:
-
Measurement Techniques:
-
Common Mistakes to Avoid:
-
Overfilling:
- Leads to inefficient grinding, increased energy consumption, and potential mill damage.
-
Underfilling:
- Results in excessive wear, reduced throughput, and inconsistent product quality.
-
Ignoring Mill Speed:
- Failing to consider the mill's rotational speed when determining filling volume can lead to suboptimal performance.
-
Overfilling:
By adhering to the recommended filling volume range and considering the factors outlined above, operators can ensure efficient and effective ball mill operation, achieving the desired grinding results while minimizing wear and energy consumption.
Summary Table:
Aspect | Details |
---|---|
Optimal Filling Volume | 30% to 50% of total mill volume |
Overfilling Risks | Reduced efficiency, increased energy use, potential mill damage |
Underfilling Risks | Excessive wear, inadequate grinding, inconsistent product quality |
Key Factors | Material properties, grinding media size, mill speed, desired fineness |
Measurement Methods | Visual inspection, sound analysis, power draw |
Common Mistakes | Overfilling, underfilling, ignoring mill speed |
Optimize your ball mill performance today—contact our experts for tailored advice!