Plasma generation in sputtering is a critical process that involves creating a potential difference between a cathode (target material) and an anode (chamber wall or substrate), ionizing a low-pressure inert gas like argon, and sustaining the plasma through various discharge maintenance processes. The plasma is ignited by applying a high voltage, which ionizes the gas atoms, creating positively charged ions and free electrons. The recombination of these ions and electrons releases energy in the form of light, producing the characteristic plasma glow. The process is further enhanced by magnetic fields in magnetron sputtering, which increase ionization efficiency and deposition rates. Understanding the operating parameters, such as particle densities, discharge currents, and energy distributions, is essential for optimizing the sputtering process.
Key Points Explained:
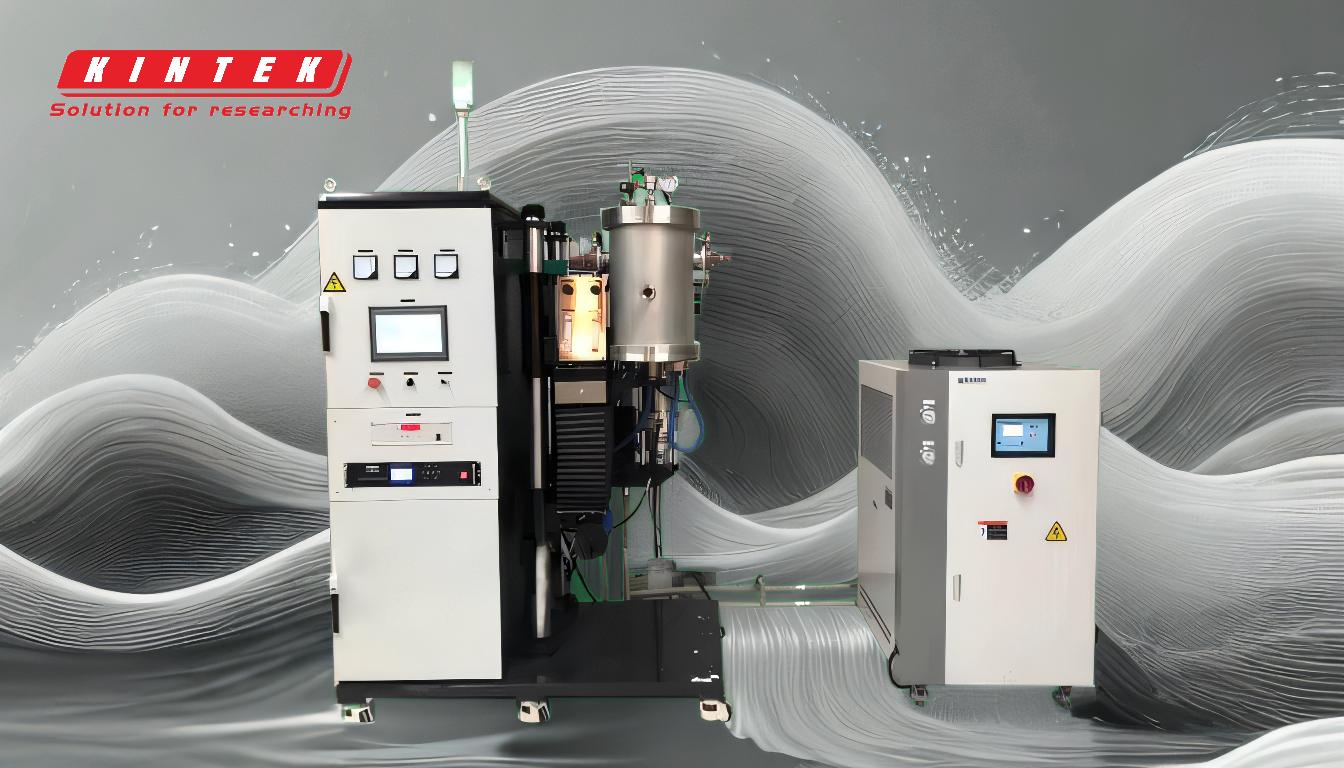
-
Potential Difference and Ionization:
- Plasma generation begins with creating a potential difference between the cathode (target material) and the anode (chamber wall or substrate). This voltage differential ionizes the neutral gas, typically argon, in the chamber.
- The ionization process involves stripping electrons from argon atoms, creating positively charged argon ions and free electrons. This ionization is essential for sustaining the plasma.
-
Role of Inert Gas (Argon):
- Argon is the most commonly used inert gas in sputtering due to its larger atomic mass compared to other inert gases like helium or neon. This larger mass increases the efficiency of the sputtering process by enhancing the momentum transfer during collisions with the target material.
- The low-pressure environment (around 1 Pa) is critical for maintaining the plasma, as it reduces the likelihood of unwanted collisions and ensures a stable discharge.
-
Plasma Glow and Recombination:
- The visible plasma glow is a result of the recombination of positively charged ions with free electrons. When an electron recombines with an ion, it releases excess energy in the form of light, producing the characteristic glow.
- This recombination process is a key indicator of a stable plasma and is used to monitor the sputtering process.
-
Magnetron Sputtering and Magnetic Fields:
- In magnetron sputtering, a magnetic field is applied to confine the electrons near the target surface, increasing the ionization efficiency and deposition rate.
- The magnetic field traps electrons, forcing them to spiral along the field lines, which increases the likelihood of collisions with argon atoms and enhances the plasma density.
-
Operating Parameters and Plasma Properties:
- Key parameters in sputtering include particle densities, discharge current composition, electron and ion energy distributions, and deposition rates.
- Understanding these parameters is crucial for optimizing the sputtering process, as they directly affect the quality and efficiency of the thin film deposition.
-
Discharge Maintenance Processes:
- The plasma is sustained through various discharge maintenance processes, including electron heating, secondary electron creation, Ohmic heating, and sputter processes.
- These processes ensure that the plasma remains stable and that the sputtering process continues efficiently.
-
Reactive Sputtering and Surface Reactions:
- In reactive sputtering, chemical reactions occur at three primary surfaces: the target surface, the substrate surface, and the chamber (or chamber liner) surface.
- These reactions can influence the composition and properties of the deposited film, making it essential to control the reactive gas flow and plasma conditions.
-
Steps in the Sputtering Process:
- The sputtering process involves several key steps: creating a vacuum, introducing an inert gas, heating the chamber, applying a magnetic field, ionizing the gas, and negatively charging the target to attract ions.
- Each step must be carefully controlled to ensure optimal plasma generation and film deposition.
By understanding these key points, one can gain a comprehensive understanding of how plasma is generated and sustained in the sputtering process, enabling better control and optimization of thin film deposition techniques.
Summary Table:
Key Aspect | Description |
---|---|
Potential Difference | Voltage between cathode and anode ionizes inert gas (argon). |
Role of Argon | Larger atomic mass enhances momentum transfer for efficient sputtering. |
Plasma Glow | Recombination of ions and electrons releases energy as visible light. |
Magnetron Sputtering | Magnetic fields increase ionization efficiency and deposition rates. |
Operating Parameters | Particle densities, discharge currents, and energy distributions are critical. |
Discharge Maintenance | Processes like electron heating and Ohmic heating sustain stable plasma. |
Reactive Sputtering | Chemical reactions at surfaces influence film composition and properties. |
Sputtering Steps | Vacuum creation, inert gas introduction, ionization, and target charging. |
Optimize your sputtering process with expert insights—contact us today!