Designing a pyrolysis reactor involves a comprehensive understanding of the process requirements, material characteristics, and operational goals. The design must ensure efficiency, safety, and adaptability to the specific feedstock and desired outputs. Key considerations include the reactor type (batch or continuous), size, heating mechanism, and integration with auxiliary systems like gas handling and product separation. Below, we break down the essential aspects of designing a pyrolysis reactor.
Key Points Explained:
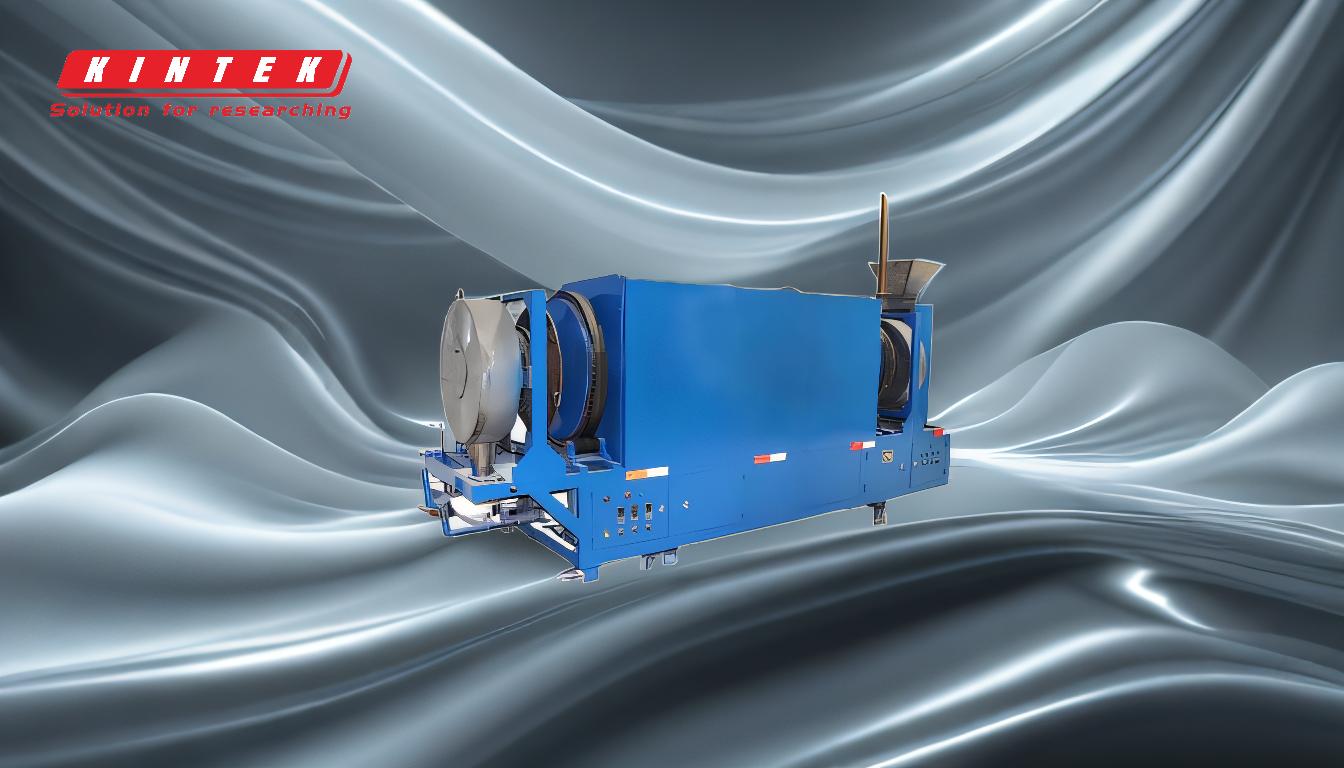
-
Determine the Reactor Type Based on Operational Needs:
- Batch vs. Continuous Reactors: Batch reactors are suitable for smaller-scale operations or when processing limited feedstock. They are cost-effective and simpler to operate but may have lower efficiency. Continuous reactors, on the other hand, are ideal for large-scale operations requiring high throughput and automation. They offer better energy efficiency and consistent output but come with higher initial costs.
- Decision Factors: Choose based on feedstock availability, budget, and desired automation level. For instance, if you have a continuous supply of raw materials and a higher budget, a continuous pyrolysis reactor is preferable.
-
Select the Appropriate Size and Capacity:
- Feedstock Volume: The reactor size should match the volume of feedstock you plan to process. For small-scale operations, compact reactors are sufficient, while larger reactors are needed for industrial-scale processing.
- Scalability: Ensure the design allows for future expansion if needed. Modular designs can be advantageous for scaling up operations.
-
Consider the Heating Mechanism:
- Direct vs. Indirect Heating: Direct heating involves exposing the feedstock to a heat source, while indirect heating uses a heat exchanger. Indirect heating is often preferred for better control over temperature and reduced contamination risks.
- Heat Source: Common heat sources include electric heaters, gas burners, or waste heat from other processes. The choice depends on cost, availability, and energy efficiency.
-
Integrate Auxiliary Systems:
- Gas Handling: Pyrolysis produces syngas, which must be safely captured and processed. Design a system for gas collection, cooling, and purification.
- Product Separation: The reactor should be integrated with cyclones, condensers, and quenchers to separate biochar, bio-oil, and syngas effectively.
- Safety Systems: Include pressure relief valves, temperature sensors, and emergency shutdown mechanisms to ensure safe operation.
-
Optimize for Feedstock Characteristics:
- Material Type: Different feedstocks (e.g., plastics, rubber, biomass) have varying thermal properties and decomposition temperatures. Design the reactor to accommodate these variations.
- Pretreatment Requirements: Some materials may require drying or shredding before pyrolysis. Ensure the reactor design can handle pretreated feedstock efficiently.
-
Ensure Energy Efficiency and Environmental Compliance:
- Heat Recovery: Incorporate heat recovery systems to reuse waste heat, improving overall energy efficiency.
- Emissions Control: Design the reactor to minimize emissions and comply with environmental regulations. This may include scrubbers or filters for gas treatment.
-
Evaluate Cost and Maintenance Considerations:
- Initial Investment: Balance the upfront cost with long-term operational benefits. For example, a continuous reactor may have a higher initial cost but lower operating expenses over time.
- Maintenance Requirements: Choose a design that minimizes downtime and maintenance costs. Durable materials and easy-to-access components can reduce maintenance efforts.
By carefully considering these factors, you can design a pyrolysis reactor that meets your specific operational needs, maximizes efficiency, and ensures safety and environmental compliance. Whether you choose a batch or continuous system, the key is to align the design with your feedstock, budget, and production goals.
Summary Table:
Key Aspect | Details |
---|---|
Reactor Type | Batch (small-scale, cost-effective) or Continuous (large-scale, automated) |
Size & Capacity | Match feedstock volume; ensure scalability for future expansion |
Heating Mechanism | Direct (exposure) or Indirect (heat exchanger); choose heat source wisely |
Auxiliary Systems | Gas handling, product separation, and safety mechanisms |
Feedstock Optimization | Accommodate material type and pretreatment requirements |
Energy Efficiency | Incorporate heat recovery and emissions control systems |
Cost & Maintenance | Balance initial investment with long-term operational benefits |
Ready to design a pyrolysis reactor tailored to your needs? Contact our experts today for a customized solution!