Centrifugation and filtration are both widely used separation techniques, but their suitability depends on the specific application, sample type, and desired outcomes. Centrifugation leverages centrifugal force to separate components based on density differences, making it ideal for separating particles or cells from liquids. Filtration, on the other hand, relies on physical barriers (filters) to separate solids from liquids based on particle size. The choice between the two depends on factors such as sample volume, particle size, throughput requirements, and the need for scalability. Centrifugation is often faster and more efficient for small particles and high-throughput applications, while filtration is better suited for large-scale operations and samples with larger particles. Both methods have their advantages and limitations, and the decision should be guided by the specific requirements of the task at hand.
Key Points Explained:
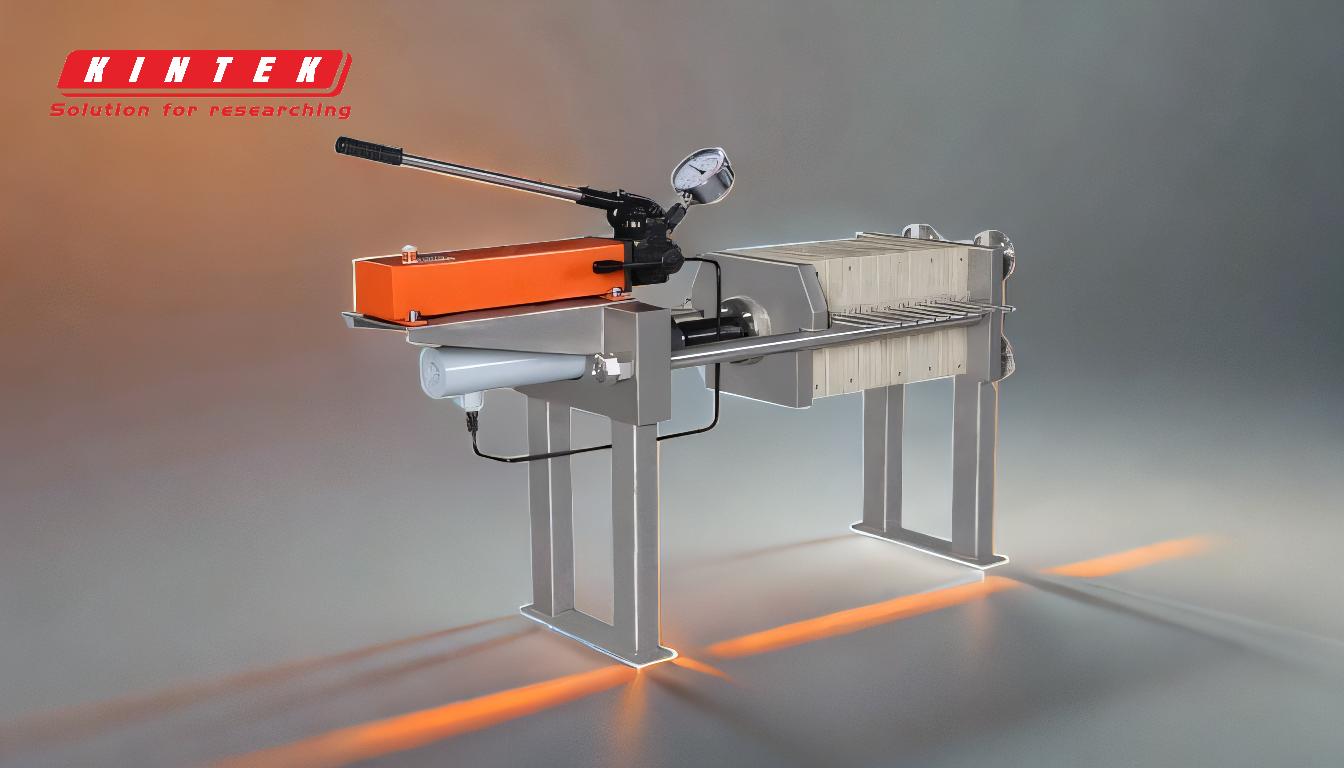
-
Principle of Operation:
- Centrifugation: Utilizes centrifugal force to separate components based on their density differences. Denser particles move outward, while lighter components remain closer to the center.
- Filtration: Relies on a physical barrier (filter) to separate solids from liquids based on particle size. Particles larger than the filter's pore size are retained, while smaller particles and liquids pass through.
-
Applications:
- Centrifugation: Ideal for separating small particles, cells, or organelles from liquids. Commonly used in biological research, clinical diagnostics, and industrial processes.
- Filtration: Suitable for separating larger particles or clarifying liquids. Widely used in water treatment, pharmaceutical manufacturing, and food processing.
-
Speed and Efficiency:
- Centrifugation: Generally faster and more efficient for separating small particles, especially in high-throughput applications. However, it requires specialized equipment and can be energy-intensive.
- Filtration: Slower compared to centrifugation but can handle larger volumes and is more scalable. It is less energy-intensive but may require frequent filter replacements.
-
Sample Volume and Throughput:
- Centrifugation: Best suited for smaller sample volumes and high-throughput applications. It is less practical for large-scale operations due to equipment limitations.
- Filtration: More adaptable to large-scale operations and continuous processes. It can handle larger volumes but may require additional steps for fine particle separation.
-
Particle Size and Type:
- Centrifugation: Effective for separating particles of varying densities, including very small particles like cells or nanoparticles.
- Filtration: Better suited for separating larger particles or aggregates. It may struggle with very fine particles unless specialized filters are used.
-
Cost and Maintenance:
- Centrifugation: Higher initial cost due to the need for specialized equipment. Maintenance can be complex, and energy consumption is higher.
- Filtration: Lower initial cost and simpler maintenance. However, ongoing costs for filter replacements can add up, especially in high-throughput applications.
-
Scalability:
- Centrifugation: Limited scalability due to equipment size and energy requirements. More suitable for laboratory-scale or small industrial applications.
- Filtration: Highly scalable and adaptable to large-scale industrial processes. It is often the preferred method for continuous production lines.
-
Environmental Impact:
- Centrifugation: Higher energy consumption and potential noise pollution. However, it produces less waste compared to filtration.
- Filtration: Lower energy consumption but generates more waste in the form of used filters. Proper disposal of filters is necessary to minimize environmental impact.
In conclusion, the choice between centrifugation and filtration depends on the specific requirements of the application, including sample type, particle size, throughput, and scalability. Both methods have their strengths and limitations, and the decision should be based on a careful evaluation of these factors.
Summary Table:
Aspect | Centrifugation | Filtration |
---|---|---|
Principle of Operation | Uses centrifugal force to separate components based on density differences. | Relies on a physical barrier to separate solids from liquids based on size. |
Applications | Ideal for small particles, cells, or organelles (e.g., biological research). | Suitable for larger particles or clarifying liquids (e.g., water treatment). |
Speed and Efficiency | Faster and more efficient for small particles and high-throughput applications. | Slower but scalable for large volumes and continuous processes. |
Sample Volume | Best for smaller volumes and high-throughput. | Adaptable to large-scale operations and continuous processes. |
Particle Size | Effective for very small particles like cells or nanoparticles. | Better for larger particles; struggles with fine particles without specialized filters. |
Cost and Maintenance | Higher initial cost and energy consumption; complex maintenance. | Lower initial cost but ongoing filter replacement costs. |
Scalability | Limited scalability; suited for lab-scale or small industrial applications. | Highly scalable for large-scale industrial processes. |
Environmental Impact | Higher energy consumption; less waste. | Lower energy use but generates more waste from used filters. |
Still unsure which separation method is right for you? Contact our experts today for personalized advice!