Dual extrusion and co-extrusion are often used interchangeably, but they are not exactly the same. Dual extrusion refers to the process of using two extruders to print with two different materials simultaneously, often in 3D printing. Co-extrusion, on the other hand, is a broader term that refers to the process of extruding two or more materials through a single die to create a single part with multiple layers or components. While both processes involve the use of multiple materials, the key difference lies in the method and application. Dual extrusion is specific to 3D printing, whereas co-extrusion is used in various manufacturing processes to create multi-layered products.
Key Points Explained:
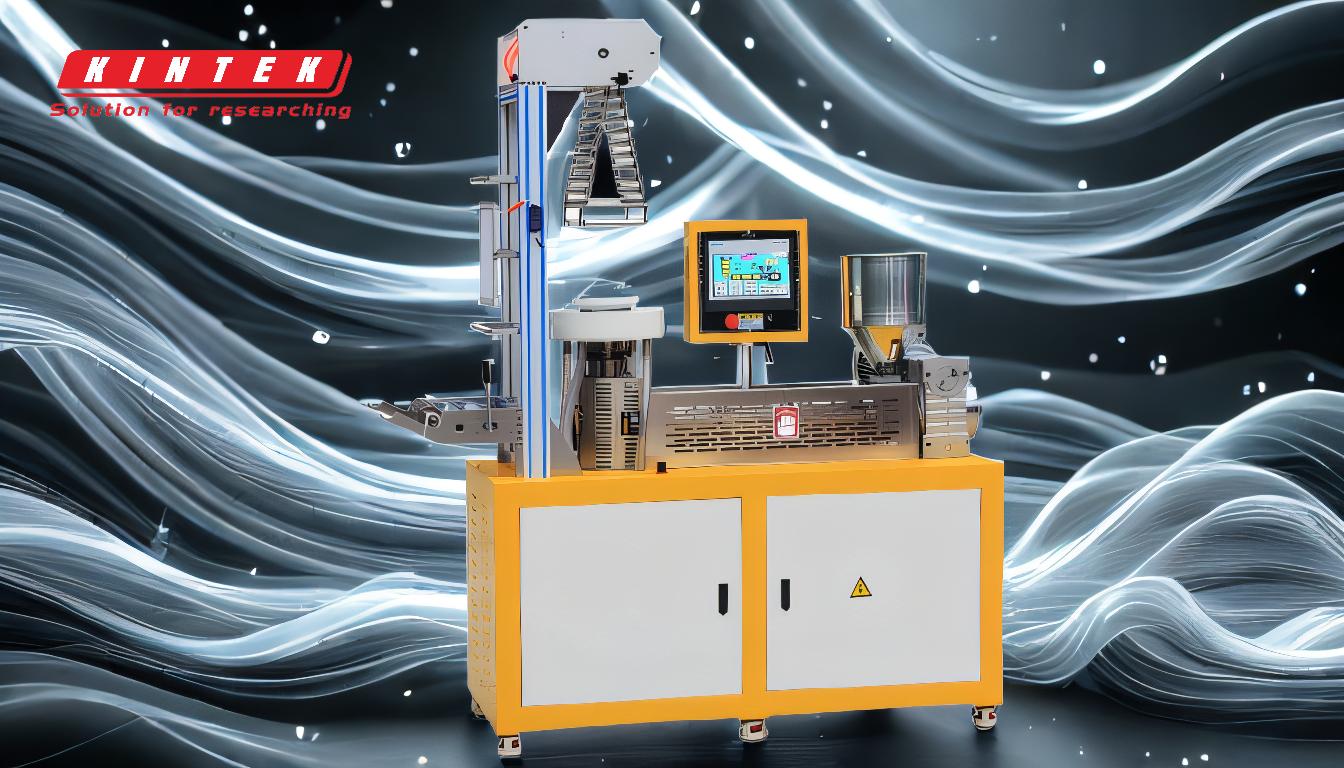
-
Definition of Dual Extrusion:
- Dual extrusion involves using two separate extruders to deposit two different materials simultaneously. This is commonly used in 3D printing to create objects with multiple colors or materials.
- The process allows for the creation of complex structures by combining different materials in a single print job.
-
Definition of Co-Extrusion:
- Co-extrusion is a manufacturing process where two or more materials are extruded through a single die to form a single part. This is often used to create products with multiple layers, such as multi-layered films, pipes, or profiles.
- The materials used in co-extrusion must be compatible to ensure proper bonding and adhesion between layers.
-
Key Differences:
- Application: Dual extrusion is primarily used in 3D printing, while co-extrusion is used in a variety of manufacturing processes, including the production of packaging materials, pipes, and profiles.
- Process: In dual extrusion, two separate extruders are used to deposit materials, whereas in co-extrusion, a single die is used to merge multiple materials into a single part.
- Material Compatibility: Dual extrusion can use a wider range of materials, including those that do not bond well together, as they are deposited separately. Co-extrusion requires materials that can bond effectively, as they are extruded together through a single die.
-
Practical Implications:
- For 3D Printing: Dual extrusion allows for the creation of multi-material or multi-color prints, enabling more complex and functional designs.
- For Manufacturing: Co-extrusion is used to create products with specific properties, such as barrier layers in packaging or reinforced layers in pipes, by combining different materials in a single extrusion process.
-
Conclusion:
- While dual extrusion and co-extrusion both involve the use of multiple materials, they are distinct processes with different applications and methodologies. Dual extrusion is specific to 3D printing, whereas co-extrusion is a broader manufacturing technique used to create multi-layered products. Understanding the differences between these processes is crucial for selecting the appropriate method for a given application.
Summary Table:
Aspect | Dual Extrusion | Co-Extrusion |
---|---|---|
Definition | Uses two extruders to print with two materials simultaneously in 3D printing. | Extrudes two or more materials through a single die to create multi-layered parts. |
Application | Primarily used in 3D printing for multi-material or multi-color prints. | Used in manufacturing for products like films, pipes, and profiles. |
Process | Two separate extruders deposit materials independently. | A single die merges multiple materials into one part. |
Material Compatibility | Can use materials that do not bond well together. | Requires materials that bond effectively for proper adhesion. |
Need help choosing the right extrusion method for your project? Contact our experts today for personalized guidance!