Ball milling is a widely used method for material synthesis and processing, offering both advantages and disadvantages. It is inexpensive, easy to perform, and capable of producing crystal defects that can be beneficial for specific applications. However, it has limitations such as being a slow process, generating noise and vibrations, and being unsuitable for soft, tacky, or fibrous materials. Additionally, high-energy ball milling, a variant of this method, is commercially viable and effective for nanoparticle synthesis but suffers from drawbacks like low surface area, polydisperse size distributions, and partially amorphous states in the final product. These factors make ball milling a versatile yet context-dependent technique.
Key Points Explained:
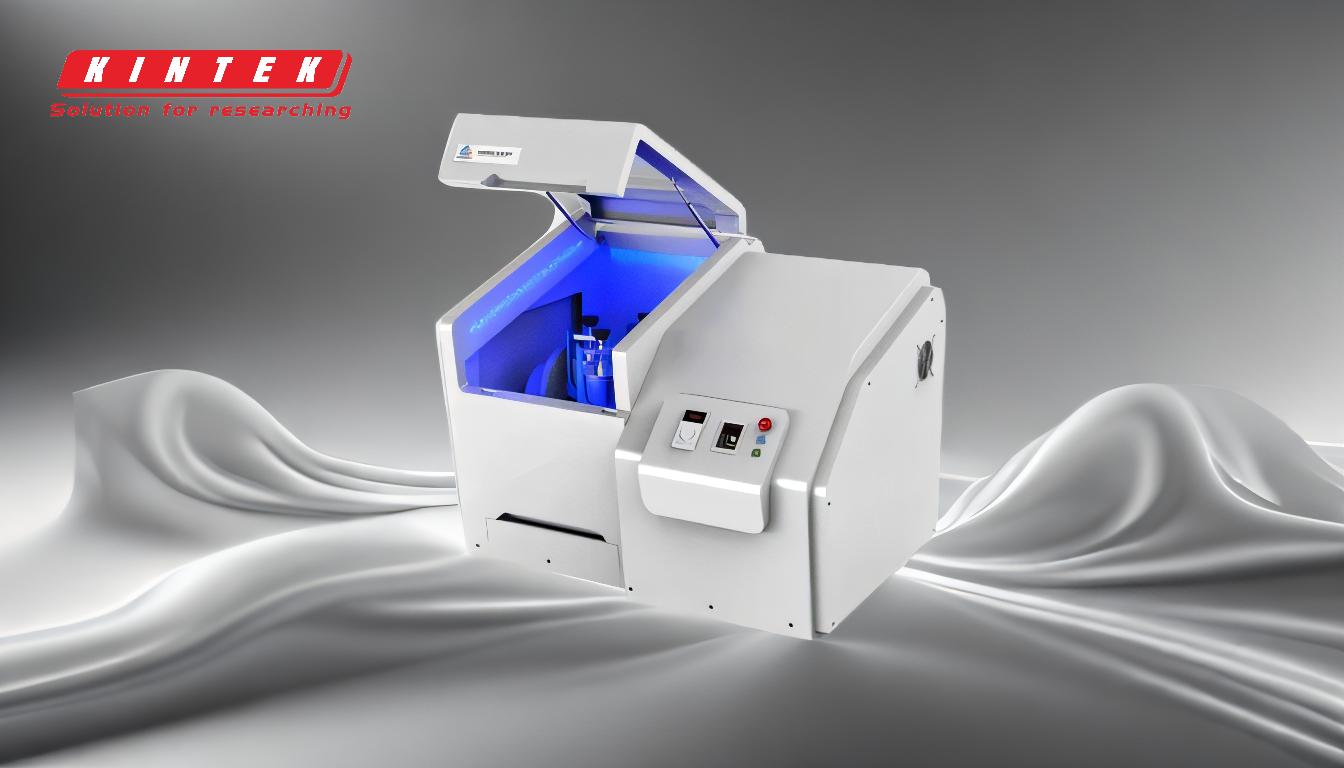
-
Advantages of Ball Milling:
-
Cost-Effective and Easy to Perform:
- Ball milling is relatively inexpensive compared to other material processing techniques, making it accessible for both research and industrial applications. Its simplicity in operation reduces the need for highly specialized training or equipment.
-
Crystal Defect Generation:
- The method can introduce crystal defects, which are beneficial in certain applications such as catalysis, where defects can enhance reactivity or improve material properties.
-
Commercial Viability (High-Energy Ball Milling):
- High-energy ball milling is particularly effective for synthesizing nanoparticles, including magnetic, catalytic, and structural nanoparticles. Its commercial viability stems from its scalability and ability to produce large quantities of material.
-
Impurity Reduction:
- Using tungsten carbide components and inert atmospheres in high-energy ball milling can significantly reduce impurities, making it suitable for high-purity applications.
-
Cost-Effective and Easy to Perform:
-
Disadvantages of Ball Milling:
-
Slow Process:
- Ball milling is often time-consuming, especially when fine particle sizes or specific material properties are required. This can be a limitation in time-sensitive applications.
-
Noise and Vibrations:
- The process generates strong vibrations and noise, which can be mitigated to some extent by using rubber balls but remains a significant drawback in environments where noise control is critical.
-
Material Limitations:
- Ball milling is ineffective for processing soft, tacky, or fibrous materials, limiting its applicability to harder, more brittle substances.
-
Wear and Contamination:
- The wear of milling components, such as the balls and cylinders, can lead to contamination of the processed material. This is particularly problematic in applications requiring high purity.
-
Low Surface Area and Polydisperse Size Distributions:
- High-energy ball milling often results in powders with low surface area and highly polydisperse size distributions, which can be undesirable for applications requiring uniform particle sizes.
-
Partially Amorphous States:
- The as-prepared powders from high-energy ball milling may be partially amorphous, which can affect their performance in applications where crystalline structures are preferred.
-
Slow Process:
-
Context-Dependent Utility:
- The effectiveness of ball milling depends on the specific requirements of the application. For example, its ability to generate crystal defects is advantageous in catalysis but may be a disadvantage in applications requiring high crystallinity. Similarly, its cost-effectiveness and ease of use make it a popular choice for bulk material processing, but its limitations in handling certain materials and producing uniform particle sizes may necessitate alternative methods in more specialized applications.
By carefully weighing these advantages and disadvantages, users can determine whether ball milling is the most suitable method for their specific needs.
Summary Table:
Aspect | Advantages | Disadvantages |
---|---|---|
Cost | Inexpensive and easy to perform | Slow process, time-consuming |
Material Properties | Generates crystal defects beneficial for catalysis | Unsuitable for soft, tacky, or fibrous materials |
Commercial Viability | Effective for nanoparticle synthesis; scalable and high-purity applications | Low surface area, polydisperse size distributions, partially amorphous states |
Operational Challenges | Reduces impurities with tungsten carbide and inert atmospheres | Generates noise and vibrations; wear and contamination risks |
Need help deciding if ball milling is right for your application? Contact our experts today!