Sputtering is a widely used physical vapor deposition (PVD) technique with several advantages and disadvantages. It is particularly valued for its ability to produce high-quality thin films with excellent uniformity, density, and control over film properties. However, challenges such as contamination, difficulty in combining with lift-off processes, and limitations in active control for layer-by-layer growth are notable drawbacks. Despite these issues, sputtering remains a versatile and efficient method, especially in applications requiring precise control over film thickness and material properties.
Key Points Explained:
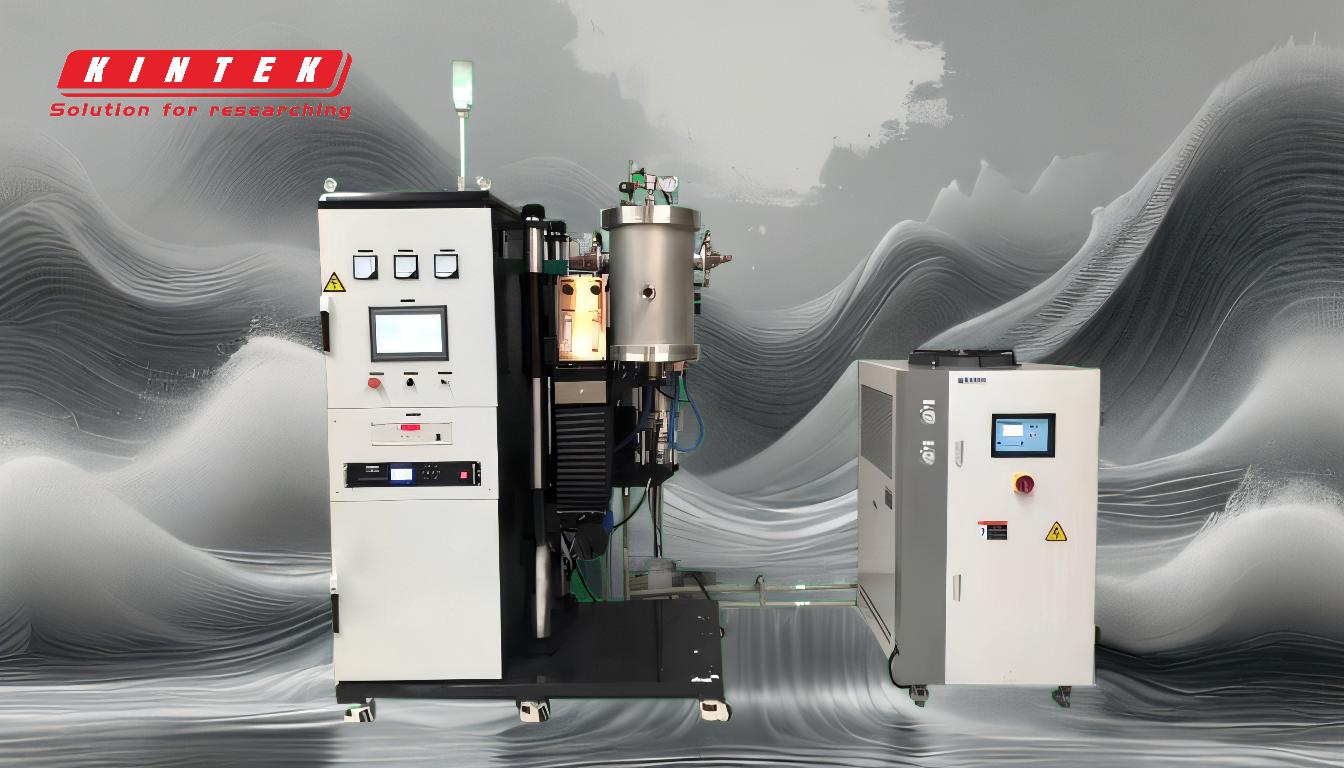
-
Advantages of Sputtering:
- High-Quality Films: Sputtering produces films with excellent morphological quality, including low roughness, controlled grain size, and precise stoichiometry. This makes it ideal for applications where surface quality is critical.
- Film Densification: The process results in better film densification compared to other deposition methods, leading to improved mechanical and optical properties.
- Low Residual Stresses: Films deposited via sputtering typically exhibit low or medium residual stresses due to the low or medium temperature deposition process, which is beneficial for substrate integrity.
- High Deposition Rates: Sputtering offers high deposition rates without thickness limitations, making it efficient for producing thick films.
- Substrate Cleaning: The ability to clean substrates within the vacuum chamber before deposition enhances film adhesion and quality.
- Uniformity and Control: Sputtering allows for excellent control over film thickness and uniformity by adjusting process parameters such as power, pressure, and deposition time.
-
Disadvantages of Sputtering:
- Contamination Issues: Impurities from the source materials or sputtering gases can diffuse into the film, leading to contamination. This limits the selection of coating materials based on their melting temperature and purity.
- Difficulty with Lift-Off Processes: The diffuse transport of sputtered atoms makes full shadowing impossible, complicating the combination of sputtering with lift-off processes for film structuring.
- Challenges in Layer-by-Layer Growth: Active control for precise layer-by-layer growth is more challenging in sputtering compared to methods like pulsed laser deposition.
- Inert Gas Impurities: Inert sputtering gases, such as argon, can become impurities in the growing film, affecting its properties.
-
Magnetron Sputtering:
- Enhanced Material Properties: Magnetron sputtering creates uniform and tight patterns of high-energy atoms that penetrate the substrate, improving properties such as corrosion resistance, wear resistance, and specific optical or electrical characteristics.
- High Deposition Rates and Precision: This technique offers high deposition rates and precise control over the deposition process, making it particularly useful for depositing dielectric and nitride films in microelectronics and semiconductor applications.
-
Applications and Versatility:
- Microelectronics and Semiconductors: Sputtering is widely used in these fields due to its ability to deposit high-quality dielectric and nitride films with precise control.
- Ongoing Advancements: Continuous research and development are expanding the capabilities and applications of sputtering, making it a versatile and evolving technique.
In summary, sputtering is a powerful and versatile deposition technique with significant advantages in producing high-quality thin films. However, it also presents challenges such as contamination and difficulty in certain process integrations. Understanding these pros and cons is essential for selecting the appropriate deposition method for specific applications.
Summary Table:
Aspect | Advantages | Disadvantages |
---|---|---|
Film Quality | High-quality films with low roughness, controlled grain size, and stoichiometry | Contamination issues from source materials or sputtering gases |
Film Densification | Improved mechanical and optical properties due to better densification | Difficulty in combining with lift-off processes |
Residual Stresses | Low or medium residual stresses, beneficial for substrate integrity | Challenges in active control for layer-by-layer growth |
Deposition Rates | High deposition rates without thickness limitations | Inert gas impurities (e.g., argon) affecting film properties |
Substrate Cleaning | Enhanced film adhesion and quality through in-chamber cleaning | |
Uniformity & Control | Precise control over film thickness and uniformity |
Want to learn more about sputtering and its applications? Contact our experts today for tailored solutions!