Tungsten is a material with unique properties that make it highly valuable in various industrial applications, particularly in high-temperature environments. Its high melting point, corrosion resistance, and thermal conductivity are significant advantages. However, it also has limitations, such as challenges in processing certain materials and constraints related to its use in evaporation boats. Below, we explore the advantages and disadvantages of tungsten in detail, focusing on its properties and applications, especially in the context of tungsten boats.
Key Points Explained:
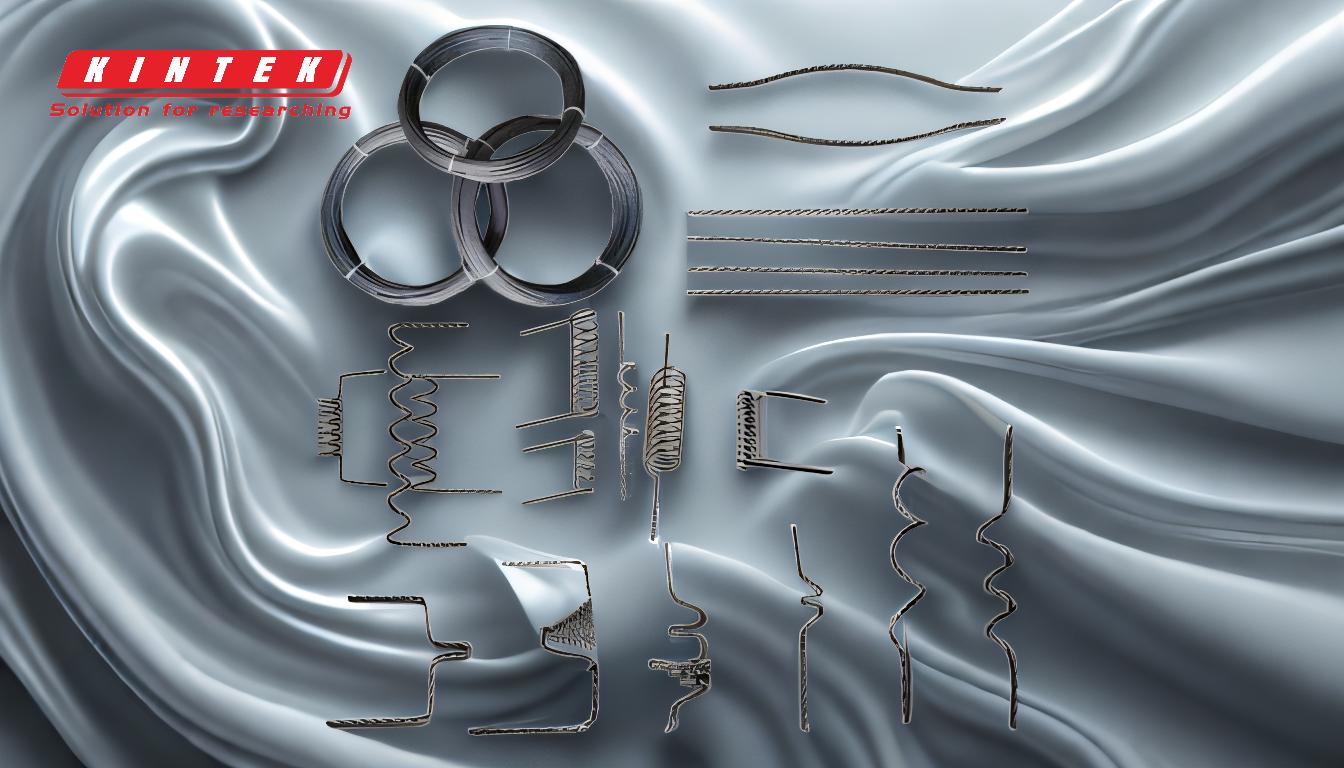
-
Advantages of Tungsten:
- High Melting Point: Tungsten has the highest melting point of all metals (3,422°C or 6,192°F), making it ideal for high-temperature applications such as filaments in incandescent light bulbs, heating elements, and aerospace components.
- Corrosion Resistance: Tungsten is highly resistant to corrosion, which is further enhanced by special dopants like potassium silicate. This makes it suitable for use in harsh chemical environments.
- Thermal and Mechanical Properties: Tungsten exhibits excellent thermal conductivity and mechanical strength, making it useful in applications requiring durability and heat dissipation, such as in electronics and thin-film coatings.
- Dimensional Stability: Tungsten maintains its shape and size even under extreme conditions, which is critical for precision applications like evaporation boats used in thin-film deposition processes.
-
Disadvantages of Tungsten:
- Processing Limitations: While tungsten is excellent for high-temperature applications, it has limitations in processes like evaporation. For instance, the melting point of the coating material cannot exceed that of the tungsten boat, restricting the range of materials that can be evaporated.
- Poor Film Density: In evaporation processes, tungsten boats can produce thin films with poor density, which may not be suitable for certain applications requiring dense, uniform coatings.
- Brittleness: Tungsten is relatively brittle at room temperature, which can make machining and shaping difficult. This limits its use in applications requiring intricate designs or flexibility.
- Cost: Tungsten is relatively expensive compared to other metals, which can be a disadvantage in cost-sensitive applications.
-
Applications of Tungsten:
- Evaporation Boats: Tungsten boats are widely used in thin-film deposition processes due to their high melting point and corrosion resistance. However, they are limited by the materials they can evaporate and the density of the resulting films.
- Electronics and Semiconductors: Tungsten's thermal and mechanical properties make it ideal for use in microelectronics, such as interconnects and diffusion barriers in semiconductor devices.
- Aerospace and Defense: Tungsten is used in high-temperature components, radiation shielding, and ammunition due to its strength and density.
- Decorative Coatings: Tungsten thin films are used for their aesthetic appeal and durability in decorative applications.
-
Considerations for Purchasers:
- Material Compatibility: When using tungsten boats, ensure the materials being processed have melting points below that of tungsten to avoid damage or inefficiency.
- Application Requirements: Evaluate whether the density and uniformity of the films produced by tungsten boats meet the specific needs of your application.
- Cost vs. Performance: While tungsten offers exceptional performance in high-temperature and corrosive environments, its cost may be a limiting factor for budget-conscious projects.
- Machining and Fabrication: Consider the challenges of machining tungsten due to its brittleness and ensure that your fabrication processes are equipped to handle it.
In summary, tungsten is a versatile material with significant advantages in high-temperature and corrosive environments, making it indispensable in industries like electronics, aerospace, and thin-film deposition. However, its limitations, such as processing constraints and brittleness, must be carefully considered when selecting it for specific applications. For applications involving tungsten boats, understanding these trade-offs is crucial for achieving optimal results.
Summary Table:
Aspect | Advantages | Disadvantages |
---|---|---|
High Melting Point | Ideal for high-temperature applications (3,422°C or 6,192°F). | Processing limitations for materials with higher melting points. |
Corrosion Resistance | Resistant to harsh chemical environments, enhanced by dopants like potassium silicate. | Poor film density in evaporation processes. |
Thermal Conductivity | Excellent heat dissipation, suitable for electronics and thin-film coatings. | Brittle at room temperature, making machining difficult. |
Dimensional Stability | Maintains shape under extreme conditions, critical for precision applications. | High cost compared to other metals, limiting use in budget-sensitive projects. |
Discover how tungsten can enhance your industrial processes—contact our experts today for tailored solutions!