Sputter deposition is a highly versatile and efficient thin-film deposition technique with numerous advantages over other methods like thermal evaporation or E-beam deposition. It excels in reproducibility, process automation, and the ability to deposit a wide range of materials, including those with high melting points. The process ensures strong film adhesion, uniform coatings, and precise control over film properties, making it suitable for applications in optics, electronics, and advanced materials. Additionally, sputter deposition is cost-effective, compatible with reactive gases, and capable of producing high-quality films at reduced temperatures, making it a preferred choice for many industrial and research applications.
Key Points Explained:
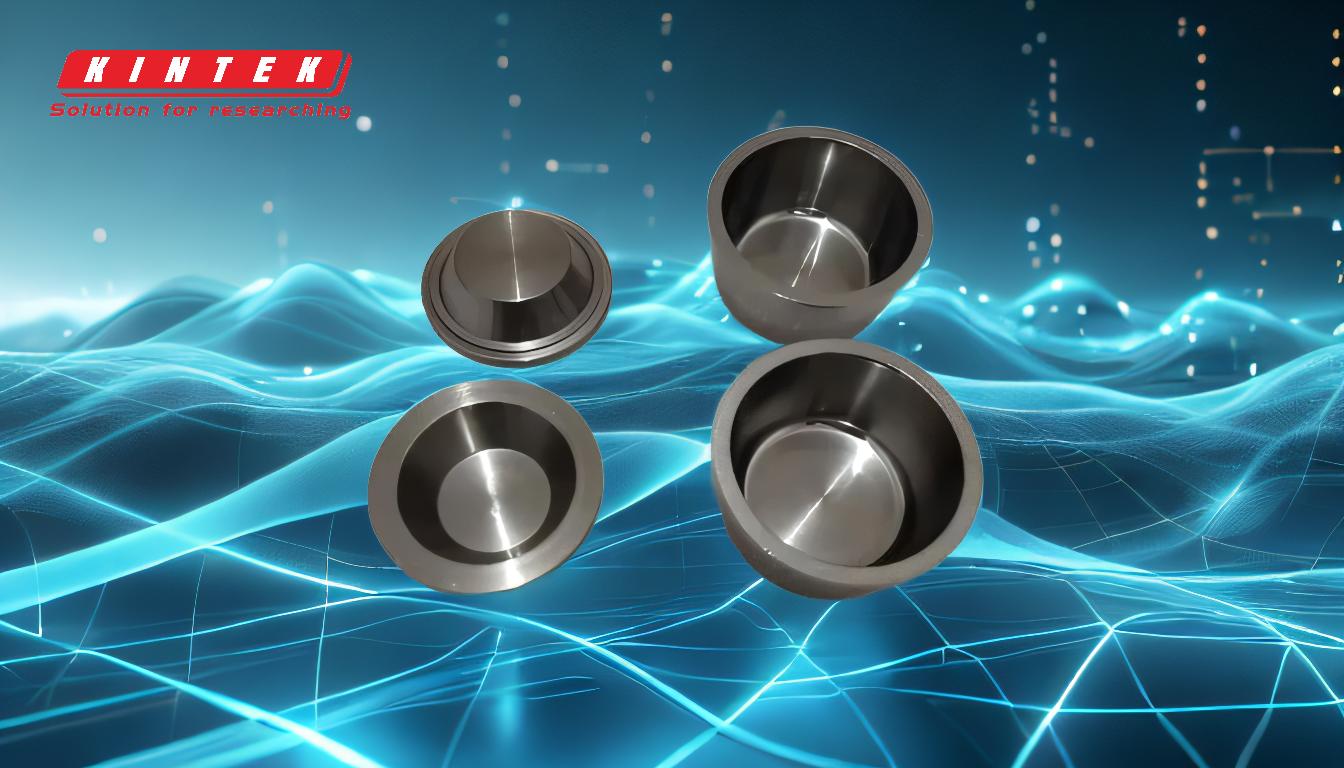
-
Reproducibility and Process Automation:
- Sputter deposition offers high reproducibility, ensuring consistent film quality across multiple runs.
- The process is easier to automate compared to methods like E-beam or thermal evaporation, reducing human error and increasing efficiency.
-
Versatility in Material Deposition:
- It can deposit a wide range of materials, including elements, alloys, and compounds, making it suitable for diverse applications.
- Materials with very high melting points, which are difficult or impossible to evaporate, can be easily sputtered.
-
Strong Film Adhesion:
- Sputter-ejected atoms have higher kinetic energies than evaporated materials, resulting in better adhesion to substrates.
- This strong adhesion is crucial for applications requiring durable and long-lasting coatings.
-
Uniform and High-Quality Films:
- Sputter deposition produces more uniform films with higher packing densities, even at low temperatures.
- The process allows for molecular-level precision, enabling the creation of pristine interfaces and precise tuning of film properties.
-
Reactive Deposition Capability:
- Reactive deposition can be easily accomplished using reactive gaseous species activated in plasma.
- This capability is essential for forming oxide or nitride film layers with desired compositions, particularly in optical film applications.
-
Low Radiant Heat and Compact Configuration:
- The process generates very little radiant heat, allowing the source and substrate to be spaced close together.
- The sputter deposition chamber can have a small volume, making it suitable for compact and efficient setups.
-
Cost-Effectiveness:
- Sputter deposition is relatively inexpensive compared to other deposition processes, making it an economical choice for many applications.
-
Compatibility with Various Substrates:
- It can coat a wide range of substrates, including plastics, organics, glass, and metals, at reduced temperatures.
- This versatility makes it suitable for applications in diverse industries, from electronics to packaging.
-
Maintenance-Free and Ultrahigh Vacuum Compatibility:
- The process is maintenance-free and can be performed in ultrahigh vacuum conditions, ensuring high purity and quality of the deposited films.
- It supports advanced processes like epitaxial growth, which is crucial for high-performance electronic devices.
-
Concurrent Double-Sided Coating:
- With appropriate mechanical configuration, sputter deposition can perform concurrent double-sided coating, increasing throughput and efficiency.
In summary, sputter deposition stands out for its versatility, precision, and efficiency, making it a preferred method for a wide range of thin-film applications. Its ability to produce high-quality, durable, and uniform films at a relatively low cost ensures its continued relevance in both industrial and research settings.
Summary Table:
Advantage | Description |
---|---|
Reproducibility & Automation | Ensures consistent film quality and reduces human error through automation. |
Versatility in Materials | Deposits elements, alloys, and high-melting-point materials with ease. |
Strong Film Adhesion | Higher kinetic energy of sputtered atoms ensures durable coatings. |
Uniform & High-Quality Films | Produces dense, uniform films with molecular-level precision. |
Reactive Deposition Capability | Forms oxide/nitride layers using reactive gases for optical applications. |
Low Radiant Heat | Compact setup with minimal heat generation for efficient operation. |
Cost-Effectiveness | Economical compared to other deposition methods. |
Substrate Compatibility | Coats plastics, organics, glass, and metals at reduced temperatures. |
Maintenance-Free & Ultrahigh Vacuum | Ensures high-purity films and supports advanced processes like epitaxial growth. |
Double-Sided Coating | Increases throughput with concurrent double-sided coating. |
Ready to enhance your thin-film processes? Contact us today to learn how sputter deposition can benefit your applications!