Twin screw extruders are widely used in various industries due to their versatility and efficiency. They offer several advantages, including improved wear resistance of components, cost-effectiveness, enhanced labor efficiency, and the ability to operate at high torque and speed. These benefits make them a preferred choice for processing materials that require precise mixing, compounding, or extrusion.
Key Points Explained:
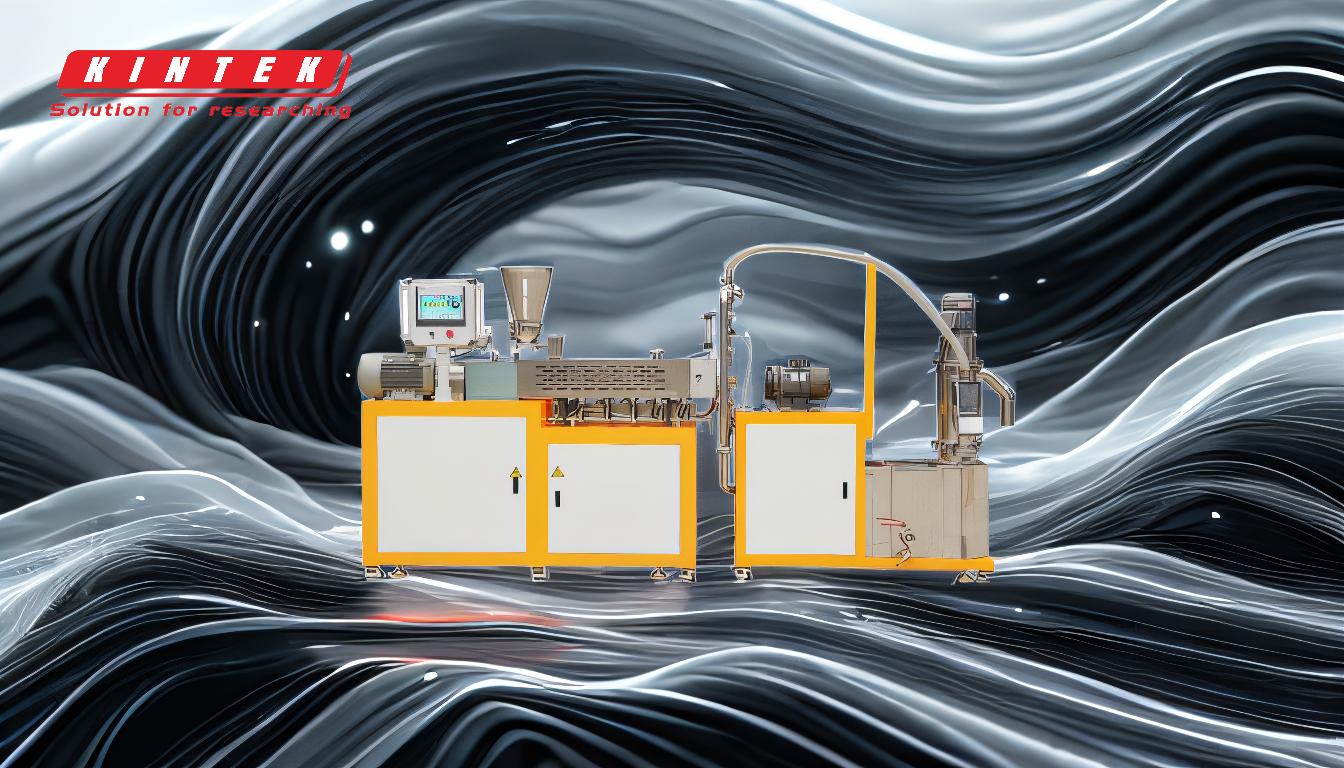
-
Improved Wear Resistance of Wearing Parts:
- Twin screw extruders are designed with durable materials and advanced engineering, which significantly reduces the wear and tear of critical components.
- This durability ensures longer operational life and minimizes downtime for maintenance, leading to consistent production quality.
- The wear-resistant design is particularly beneficial for processing abrasive materials, as it maintains performance over extended periods.
-
Reduction in Production Costs:
- The efficient design and operation of twin screw extruders contribute to lower energy consumption, which directly reduces operational costs.
- Their ability to process materials with minimal waste and high precision further enhances cost-effectiveness.
- Reduced maintenance requirements and longer component lifespan also contribute to overall cost savings.
-
Enhanced Labor Efficiency:
- Twin screw extruders are often automated or semi-automated, reducing the need for manual intervention and improving labor efficiency.
- Their consistent performance and ability to handle complex processes with minimal supervision free up workers to focus on other tasks.
- Automation also reduces the likelihood of human error, ensuring higher product quality.
-
High Torque and High-Speed Capabilities:
- Twin screw extruders are capable of operating at high torque and speed, making them suitable for processing a wide range of materials, including those with high viscosity or requiring intensive mixing.
- This capability allows for faster production rates and the ability to handle demanding applications, such as compounding polymers or producing specialty materials.
- The combination of high torque and speed ensures efficient material processing, even for challenging formulations.
In summary, twin screw extruders offer a combination of durability, cost-effectiveness, labor efficiency, and high-performance capabilities, making them an ideal choice for industries requiring precise and efficient material processing.
Summary Table:
Advantage | Description |
---|---|
Improved Wear Resistance | Durable materials and advanced engineering reduce wear, ensuring longer lifespan. |
Reduction in Production Costs | Lower energy consumption, minimal waste, and reduced maintenance save costs. |
Enhanced Labor Efficiency | Automation reduces manual intervention, improves consistency, and minimizes errors. |
High Torque & Speed | Capable of processing high-viscosity materials and demanding applications. |
Ready to enhance your material processing? Contact us today to learn more about twin screw extruders!