Sputtering deposition is a versatile and widely used technique for creating thin films on various substrates, with applications spanning multiple industries. It is particularly valuable in the semiconductor industry, optical coatings, data storage, and renewable energy sectors. The process involves ejecting atoms from a target material and depositing them onto a substrate in a vacuum environment, resulting in precise and high-quality thin films. Key applications include the production of computer hard disks, integrated circuits, anti-reflective coatings, cutting tool coatings, and solar cells. Its ability to deposit a wide range of materials, including metals, nitrides, and oxides, makes it indispensable in modern manufacturing and technology.
Key Points Explained:
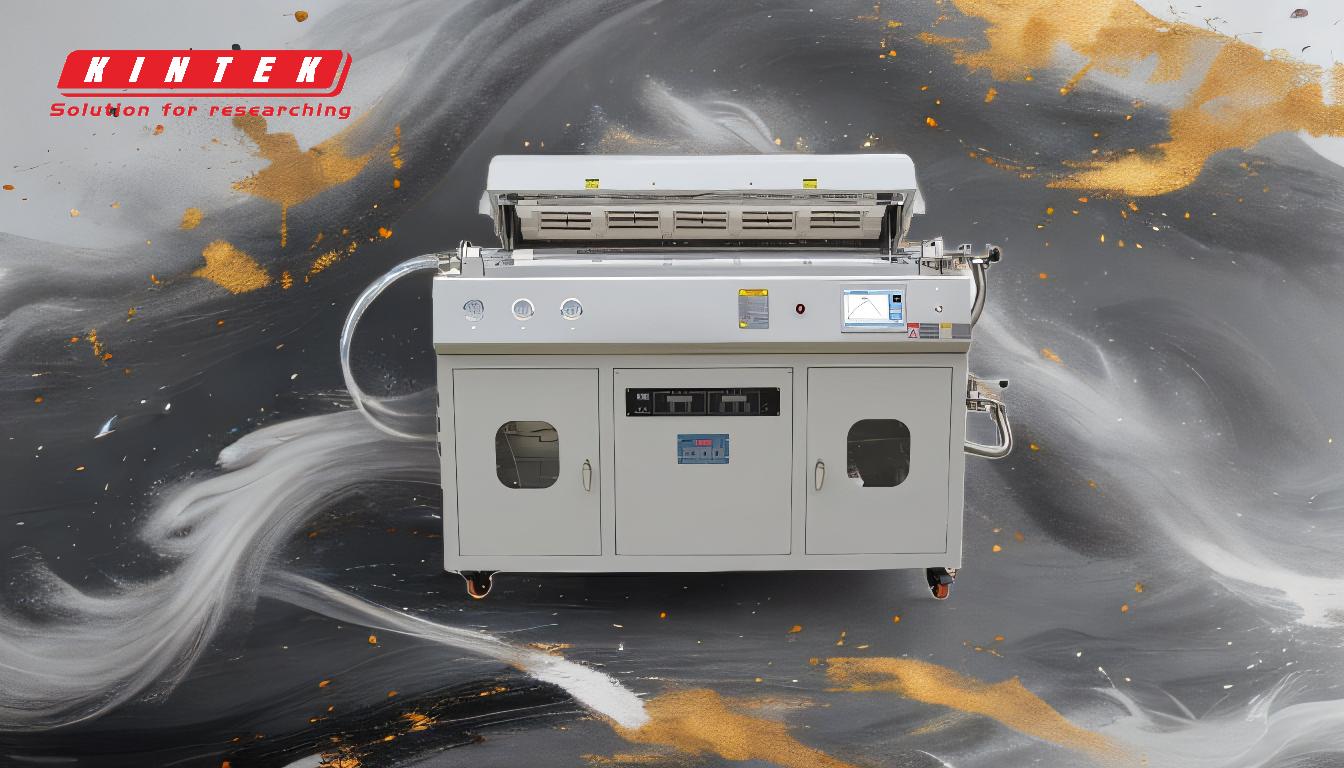
-
Semiconductor Industry:
- Application: Sputtering deposition is extensively used in the semiconductor industry for depositing thin films in integrated circuits.
- Details: It is employed to deposit various materials, such as metals and dielectrics, onto silicon wafers to create transistors, interconnects, and other components. This process ensures precise control over film thickness and uniformity, which is critical for the performance of semiconductor devices.
- Example: Sputtering is used to deposit contact metals in thin-film transistors, which are essential for displays and other electronic devices.
-
Optical Coatings:
- Application: Sputtering is used to create anti-reflective and low-emissivity coatings on glass.
- Details: Anti-reflective coatings reduce glare and improve visibility, making them ideal for eyeglasses, camera lenses, and display screens. Low-emissivity coatings are applied to double-pane windows to improve energy efficiency by reflecting infrared radiation.
- Example: Architectural glass with low-emissivity coatings helps regulate indoor temperatures, reducing heating and cooling costs.
-
Data Storage:
- Application: Sputtering deposition is crucial in the production of computer hard disks, CDs, and DVDs.
- Details: Thin magnetic films deposited via sputtering are used to store data on hard disks, while reflective coatings are applied to CDs and DVDs to enable data reading and writing.
- Example: The magnetic layers in hard disks are created using sputtering, ensuring high data density and reliability.
-
Cutting Tool Coatings:
- Application: Sputtering is used to coat cutting tools with wear-resistant materials like titanium nitride.
- Details: These coatings enhance the durability and performance of cutting tools by reducing wear and friction, extending their lifespan and improving machining efficiency.
- Example: Titanium nitride coatings on drill bits and milling cutters significantly increase their resistance to abrasion and heat.
-
Renewable Energy:
- Application: Sputtering is used in the fabrication of photovoltaic solar cells.
- Details: Thin films of materials like silicon, cadmium telluride, and copper indium gallium selenide are deposited onto substrates to create solar cells. These films are critical for converting sunlight into electricity efficiently.
- Example: Sputtering is used to deposit transparent conductive oxides, such as indium tin oxide, which are essential for the electrodes in solar cells.
-
Decorative and Functional Coatings:
- Application: Sputtering is used to apply decorative and functional coatings on various materials.
- Details: This includes metalizing plastics, creating reflective coatings on polymers, and applying wear-resistant coatings on tools. These coatings enhance both the aesthetic and functional properties of the materials.
- Example: Reflective coatings on automotive parts and decorative coatings on consumer electronics improve both appearance and performance.
-
Surface Physics and Analysis:
- Application: Sputtering is used in surface physics for cleaning and analyzing surfaces.
- Details: It is employed to prepare high-purity surfaces for research and to analyze the chemical composition of surfaces using techniques like secondary ion mass spectrometry (SIMS).
- Example: Sputtering is used to clean semiconductor wafers before further processing, ensuring high-quality thin films.
-
Historical and Commercial Applications:
- Application: Sputtering has been used commercially since the early 20th century.
- Details: Thomas Edison used sputtering to apply thin metal layers to wax phonograph recordings for mass duplication. Modern applications include anodizing aluminum for cookware and automobile wheels, providing a shiny, uniform surface and resistance to sticking.
- Example: Anodized aluminum cookware benefits from sputtering by having a durable, non-stick surface that is easy to clean.
In summary, sputtering deposition is a critical technology with a wide range of applications across various industries. Its ability to deposit thin films with high precision and uniformity makes it indispensable in modern manufacturing, from semiconductors and optical coatings to renewable energy and data storage. The versatility and reliability of sputtering ensure its continued importance in advancing technology and improving everyday products.
Summary Table:
Industry | Applications | Key Benefits |
---|---|---|
Semiconductor | Thin films for integrated circuits, transistors, and interconnects | Precise control, uniformity, and high performance |
Optical Coatings | Anti-reflective and low-emissivity coatings for glass | Improved visibility, energy efficiency, and durability |
Data Storage | Magnetic layers for hard disks, reflective coatings for CDs/DVDs | High data density, reliability, and efficient data storage |
Cutting Tools | Wear-resistant coatings like titanium nitride | Enhanced durability, reduced wear, and improved machining efficiency |
Renewable Energy | Thin films for solar cells (e.g., silicon, cadmium telluride) | Efficient sunlight-to-electricity conversion, durability, and cost-effectiveness |
Decorative Coatings | Reflective and wear-resistant coatings for automotive and consumer electronics | Improved aesthetics and functionality |
Surface Physics | Surface cleaning and analysis for research | High-purity surfaces, accurate chemical analysis |
Historical Uses | Anodizing aluminum for cookware and wheels | Durable, non-stick, and shiny surfaces |
Discover how sputtering deposition can enhance your manufacturing processes—contact our experts today!