Sieving is a fundamental process used in various industries to separate particles based on their size. The method chosen depends on the material properties, desired particle size distribution, and the scale of operation. Common sieving methods include manual sieving, mechanical sieving, air jet sieving, and sonic sifting. Each method has its unique advantages and limitations, making them suitable for specific applications. Understanding these methods helps in selecting the right equipment for efficient particle separation.
Key Points Explained:
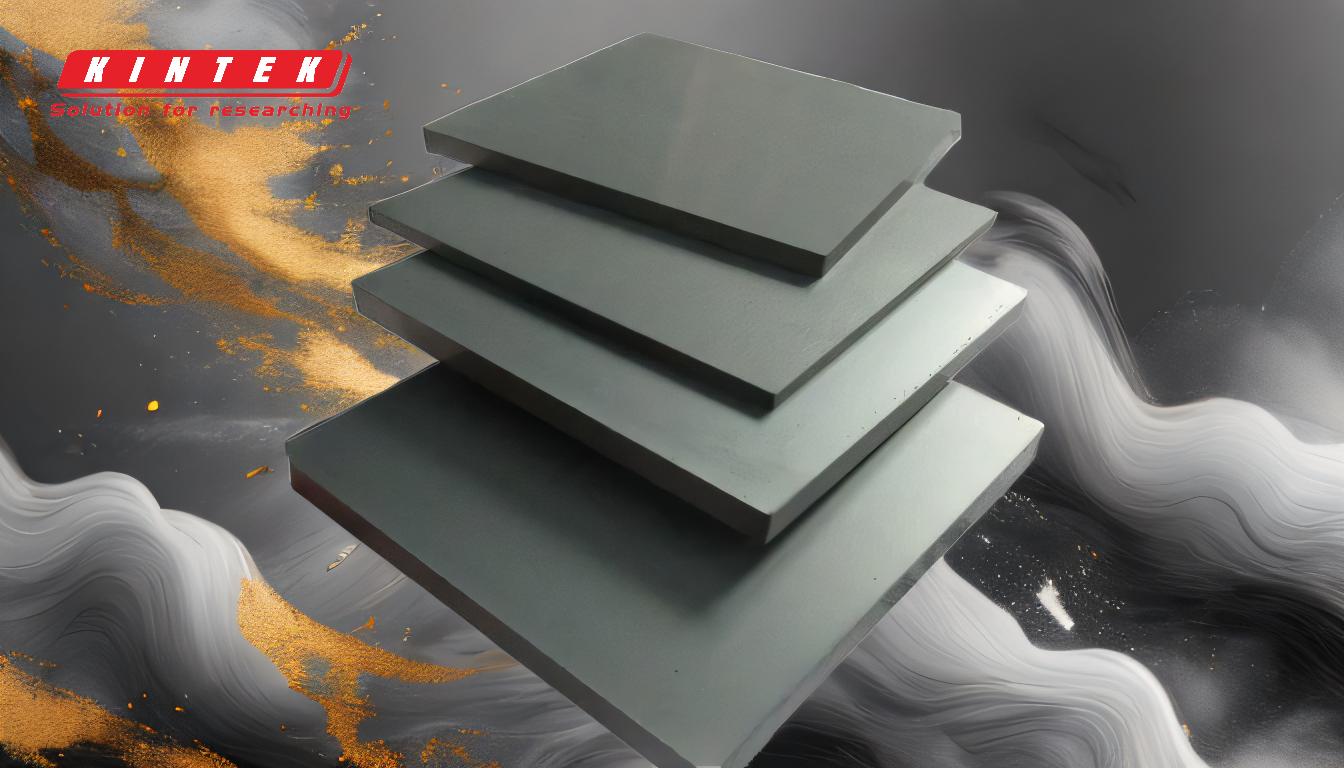
-
Manual Sieving
- Process: Involves manually shaking or tapping a sieve to separate particles.
- Applications: Suitable for small-scale operations or when dealing with delicate materials.
- Advantages: Low cost, simple to operate, and does not require power.
- Limitations: Labor-intensive, inconsistent results, and not suitable for large-scale operations.
-
Mechanical Sieving
- Process: Uses motorized equipment to agitate the sieve, causing particles to pass through the mesh.
- Applications: Widely used in industries like pharmaceuticals, food processing, and mining.
- Advantages: Consistent results, high throughput, and can handle a wide range of particle sizes.
- Limitations: Requires power, more expensive than manual sieving, and may cause wear on the sieve mesh.
-
Air Jet Sieving
- Process: Utilizes a stream of air to force particles through the sieve mesh.
- Applications: Ideal for fine powders and materials that are difficult to sieve using traditional methods.
- Advantages: Effective for very fine particles, reduces clogging, and can handle sticky or cohesive materials.
- Limitations: Requires specialized equipment, higher operational costs, and may not be suitable for all materials.
-
Sonic Sifting
- Process: Employs ultrasonic vibrations to separate particles, enhancing the sieving process.
- Applications: Used in industries requiring precise particle size separation, such as electronics and advanced materials.
- Advantages: High precision, reduces clogging, and can handle fine and ultra-fine particles.
- Limitations: Expensive equipment, requires technical expertise, and may not be suitable for all materials.
-
Wet Sieving
- Process: Involves using a liquid medium to assist in the separation of particles.
- Applications: Suitable for materials that are difficult to sieve dry, such as clays or fine aggregates.
- Advantages: Effective for materials that tend to agglomerate, reduces dust, and can handle very fine particles.
- Limitations: Requires additional drying steps, more complex setup, and potential for material loss in the liquid medium.
-
Automated Sieving Systems
- Process: Combines mechanical sieving with automation for continuous and consistent particle separation.
- Applications: Used in high-volume production environments where consistency and efficiency are critical.
- Advantages: High throughput, consistent results, and reduced labor costs.
- Limitations: High initial investment, requires maintenance, and may need specialized training for operation.
-
Vibratory Sieving
- Process: Uses vibration to move particles across the sieve surface, enhancing the separation process.
- Applications: Common in industries like construction, agriculture, and recycling.
- Advantages: Efficient for a wide range of particle sizes, reduces clogging, and can handle large volumes.
- Limitations: Can be noisy, requires power, and may cause wear on the sieve mesh.
-
Centrifugal Sieving
- Process: Employs centrifugal force to separate particles based on size.
- Applications: Suitable for fine powders and materials that require high-speed separation.
- Advantages: High-speed operation, effective for fine particles, and reduces clogging.
- Limitations: Requires specialized equipment, higher operational costs, and may not be suitable for all materials.
Each sieving method has its unique set of advantages and limitations, making it crucial to select the appropriate method based on the specific requirements of the material and the desired outcome. Understanding these methods helps in optimizing the sieving process for efficiency and accuracy.
Summary Table:
Method | Applications | Advantages | Limitations |
---|---|---|---|
Manual Sieving | Small-scale, delicate materials | Low cost, simple, no power required | Labor-intensive, inconsistent, not for large-scale |
Mechanical Sieving | Pharmaceuticals, food, mining | Consistent results, high throughput | Requires power, expensive, sieve wear |
Air Jet Sieving | Fine powders, sticky materials | Effective for fine particles, reduces clogging | Specialized equipment, higher costs |
Sonic Sifting | Electronics, advanced materials | High precision, reduces clogging | Expensive, technical expertise required |
Wet Sieving | Clays, fine aggregates | Reduces dust, handles agglomerates | Complex setup, drying steps, material loss |
Automated Sieving | High-volume production | High throughput, consistent, reduced labor | High investment, maintenance, training required |
Vibratory Sieving | Construction, agriculture, recycling | Efficient, reduces clogging, handles volumes | Noisy, power required, sieve wear |
Centrifugal Sieving | Fine powders, high-speed separation | High-speed, effective for fine particles | Specialized equipment, higher costs |
Need help selecting the best sieving method for your application? Contact our experts today!