A single punch tablet machine, also known as a single station press, is a compact and widely used machine in pharmaceutical and nutraceutical industries for tablet production. It consists of several key components that work together to compress powder into tablets. The main parts include the hopper, die, punches, cam tracks, and ejection mechanism. Each part plays a critical role in ensuring the machine operates efficiently and produces high-quality tablets. Below, we will explore the different parts of a single punch tablet machine in detail, explaining their functions and importance in the tablet manufacturing process.
Key Points Explained:
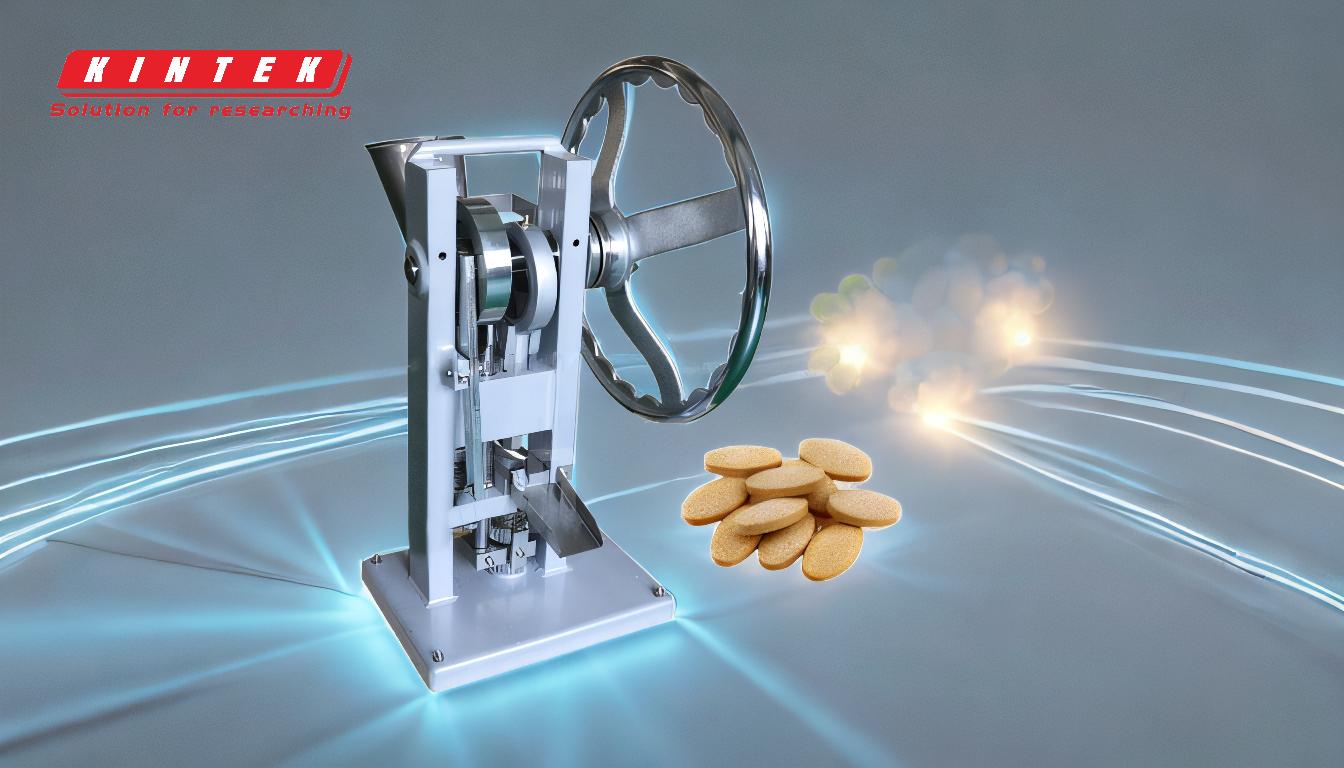
-
Hopper:
- Function: The hopper is a container that holds the powder or granulated material before it is fed into the die cavity.
- Importance: It ensures a consistent supply of material for tablet formation. The design of the hopper minimizes material segregation and ensures uniform flow.
- Details: Hoppers are often equipped with agitators or vibrators to prevent material bridging and ensure smooth flow.
-
Die:
- Function: The die is a cylindrical cavity where the powder is compressed to form the tablet.
- Importance: The die determines the size and shape of the tablet. It must be precisely machined to ensure uniformity.
- Details: Dies are typically made of high-strength steel to withstand the pressure exerted during compression.
-
Punches:
- Function: Punches are the upper and lower tools that compress the powder within the die to form the tablet.
- Importance: They apply the necessary force to compact the powder into a solid tablet. The shape of the punch tips determines the tablet's surface design.
- Details: Punches are made of hardened steel and are designed to withstand repeated compression cycles without deformation.
-
Cam Tracks:
- Function: Cam tracks guide the movement of the punches during the compression cycle.
- Importance: They ensure precise and synchronized movement of the upper and lower punches, which is critical for consistent tablet formation.
- Details: The cam tracks are designed to control the timing and force applied by the punches during the filling, compression, and ejection stages.
-
Ejection Mechanism:
- Function: The ejection mechanism removes the formed tablet from the die after compression.
- Importance: It ensures that the tablet is ejected smoothly without damage, maintaining the integrity of the final product.
- Details: The mechanism typically involves a lower punch that pushes the tablet out of the die cavity, often assisted by an ejection cam.
-
Feeding Mechanism:
- Function: The feeding mechanism ensures that the powder is evenly distributed into the die cavity.
- Importance: Uniform filling of the die is essential for consistent tablet weight and hardness.
- Details: This mechanism can include a feed shoe or paddle that moves over the die cavity, ensuring an even distribution of material.
-
Compression Rollers:
- Function: Compression rollers apply the force required to compact the powder into a tablet.
- Importance: They ensure that the correct amount of pressure is applied to achieve the desired tablet hardness and density.
- Details: The rollers are positioned to interact with the punches at the exact moment of compression, ensuring precise force application.
-
Turret:
- Function: The turret is a rotating component that holds the dies and punches in place.
- Importance: It allows for continuous operation of the machine by rotating the dies and punches through the various stages of the tablet compression process.
- Details: The turret is typically made of high-strength materials to endure the mechanical stresses of continuous operation.
-
Control Panel:
- Function: The control panel allows operators to set and monitor the machine's parameters, such as compression force and speed.
- Importance: It ensures that the machine operates within the desired specifications, leading to consistent tablet quality.
- Details: Modern single punch tablet machines often feature digital control panels with touchscreen interfaces for ease of use.
-
Frame and Base:
- Function: The frame and base provide structural support to the machine.
- Importance: They ensure stability during operation, minimizing vibrations and maintaining alignment of the components.
- Details: The frame and base are typically made of heavy-duty materials to provide a solid foundation for the machine.
Understanding the different parts of a single punch tablet machine is crucial for anyone involved in tablet manufacturing. Each component plays a vital role in ensuring the machine operates efficiently and produces high-quality tablets. By maintaining and optimizing these parts, manufacturers can achieve consistent results and meet the stringent requirements of the pharmaceutical and nutraceutical industries.
Summary Table:
Part | Function | Importance |
---|---|---|
Hopper | Holds and feeds powder into the die cavity. | Ensures consistent material supply and prevents segregation. |
Die | Cylindrical cavity where powder is compressed into tablets. | Determines tablet size and shape; ensures uniformity. |
Punches | Upper and lower tools that compress powder into tablets. | Applies force for compaction; defines tablet surface design. |
Cam Tracks | Guide punch movement during compression. | Ensures precise and synchronized punch operation for consistent tablet formation. |
Ejection Mechanism | Removes tablets from the die after compression. | Ensures smooth ejection without damaging tablets. |
Feeding Mechanism | Distributes powder evenly into the die cavity. | Ensures uniform tablet weight and hardness. |
Compression Rollers | Apply force to compact powder into tablets. | Ensures correct pressure for desired tablet hardness and density. |
Turret | Rotating component holding dies and punches. | Enables continuous operation by rotating through compression stages. |
Control Panel | Allows setting and monitoring of machine parameters. | Maintains consistent tablet quality by controlling compression force and speed. |
Frame and Base | Provides structural support to the machine. | Ensures stability and alignment during operation. |
Ready to optimize your tablet production? Contact us today to learn more about single punch tablet machines!