Biomass reactors are essential in converting biomass into valuable products through processes like pyrolysis. The primary types of biomass reactors include fixed bed, fluidized bed (bubbling and circulating), and rotary kiln reactors. Each type has unique design and operational characteristics that influence the yield and quality of the end products. Factors such as temperature, residence time, and biomass type play a critical role in determining the efficiency of these reactors. Fluidized bed reactors, in particular, are widely used in industrial applications due to their rapid reaction rates, efficient heat transfer, and scalability. Understanding the differences between these reactors is crucial for selecting the right equipment for specific biomass conversion needs.
Key Points Explained:
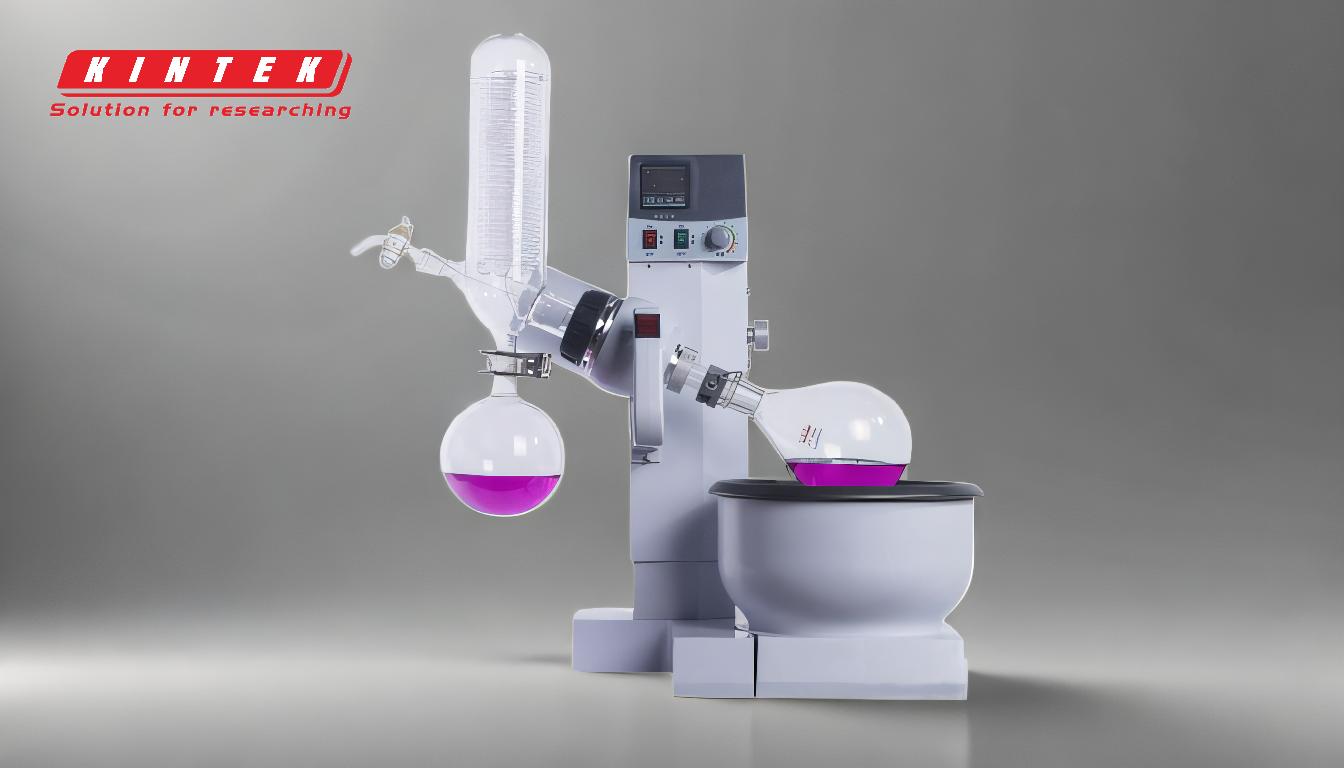
-
Types of Biomass Reactors:
-
Fixed Bed Reactors:
- These reactors are simple in design and operate by placing biomass in a stationary bed.
- They are suitable for small-scale applications and are often used in batch processes.
- The heating system is typically external, and the biomass is heated uniformly.
- However, fixed bed reactors may have limitations in scalability and heat transfer efficiency compared to other types.
-
Fluidized Bed Reactors:
-
Bubbling Fluidized Bed (BFB):
- In BFB reactors, biomass is mixed with an inert material like sand, which is fluidized by a gas flow.
- This creates a bubbling effect, enhancing heat transfer and reaction rates.
- BFBs are ideal for continuous processes and are widely used in industrial applications due to their efficiency and scalability.
-
Circulating Fluidized Bed (CFB):
- CFB reactors operate at higher gas velocities, causing the bed material and biomass to circulate continuously.
- This design provides even better heat transfer and mixing, making CFBs suitable for large-scale operations.
- CFBs are particularly effective for maximizing the production of liquid products like bio-oil.
-
Bubbling Fluidized Bed (BFB):
-
Rotary Kiln Reactors:
- These reactors consist of a rotating cylindrical chamber that tumbles the biomass as it is heated.
- The rotation ensures uniform heating and mixing, making rotary kilns suitable for processing large volumes of biomass.
- They are often used in applications where the biomass has a high moisture content or requires prolonged heating.
-
-
Key Factors Influencing Reactor Performance:
-
Temperature:
- The operating temperature of the reactor significantly affects the yield and quality of the end products.
- Higher temperatures generally favor the production of gases, while moderate temperatures are optimal for liquid products like bio-oil.
-
Residence Time:
- The time biomass spends in the reactor impacts the extent of pyrolysis.
- Longer residence times can lead to more complete conversion but may also result in secondary reactions that degrade product quality.
-
Biomass Type:
- Different biomass feedstocks have varying compositions, which influence the choice of reactor and operating conditions.
- For example, woody biomass may require different processing parameters compared to agricultural residues.
-
Temperature:
-
Advantages of Fluidized Bed Reactors:
-
Rapid Reaction and Heat Transfer:
- Fluidized bed reactors provide excellent heat transfer due to the intimate contact between the biomass and the fluidizing medium.
- This results in faster reaction rates and more efficient energy utilization.
-
Wide Contact Area:
- The fluidized state creates a large surface area for reactions, enhancing the overall process efficiency.
-
Scalability:
- Fluidized bed reactors, particularly CFBs, are highly scalable and can be adapted for large-scale industrial applications.
-
Versatility:
- These reactors can handle a wide range of biomass types and are suitable for producing various end products, including bio-oil, syngas, and biochar.
-
Rapid Reaction and Heat Transfer:
-
Applications and Industrial Use:
- Fluidized bed reactors are extensively used in industries focused on bio-oil production due to their efficiency and scalability.
- Fixed bed reactors are more commonly used in small-scale or research settings where simplicity and cost-effectiveness are prioritized.
- Rotary kiln reactors are employed in applications requiring uniform heating and mixing, such as the processing of high-moisture biomass or waste materials.
-
Considerations for Equipment Selection:
- When selecting a biomass reactor, factors such as the scale of operation, desired end products, and biomass characteristics must be considered.
- Fluidized bed reactors are generally preferred for large-scale, continuous processes, while fixed bed reactors may be more suitable for smaller, batch operations.
- Rotary kiln reactors are ideal for specific applications where uniform heating and mixing are critical.
In conclusion, the choice of biomass reactor depends on the specific requirements of the biomass conversion process, including the scale of operation, desired products, and feedstock characteristics. Fluidized bed reactors, with their rapid reaction rates and scalability, are particularly well-suited for industrial applications, while fixed bed and rotary kiln reactors offer advantages in specific scenarios. Understanding the strengths and limitations of each reactor type is essential for optimizing biomass conversion processes.
Summary Table:
Reactor Type | Key Features | Best Use Cases |
---|---|---|
Fixed Bed Reactors | Simple design, uniform heating, suitable for small-scale or batch processes | Small-scale applications, research settings |
Bubbling Fluidized Bed | Rapid reaction rates, efficient heat transfer, ideal for continuous processes | Industrial bio-oil production, continuous operations |
Circulating Fluidized Bed | Superior heat transfer, large-scale operations, maximizes liquid product yield | Large-scale bio-oil production, high-efficiency processes |
Rotary Kiln Reactors | Uniform heating and mixing, handles high-moisture biomass | Processing high-moisture biomass, waste materials |
Need help selecting the right biomass reactor for your project? Contact our experts today for tailored solutions!