Carbide tool coatings are essential for enhancing the performance, durability, and efficiency of cutting tools, particularly those made from tungsten carbide. These coatings are applied using specialized equipment and techniques to improve wear resistance, reduce friction, and extend tool life. The process involves advanced technologies such as HVOF thermal spray equipment, robotics, and precision masking fixtures to ensure consistent and high-quality coatings. Below, we explore the key aspects of carbide tool coatings, their types, and the equipment used in their application.
Key Points Explained:
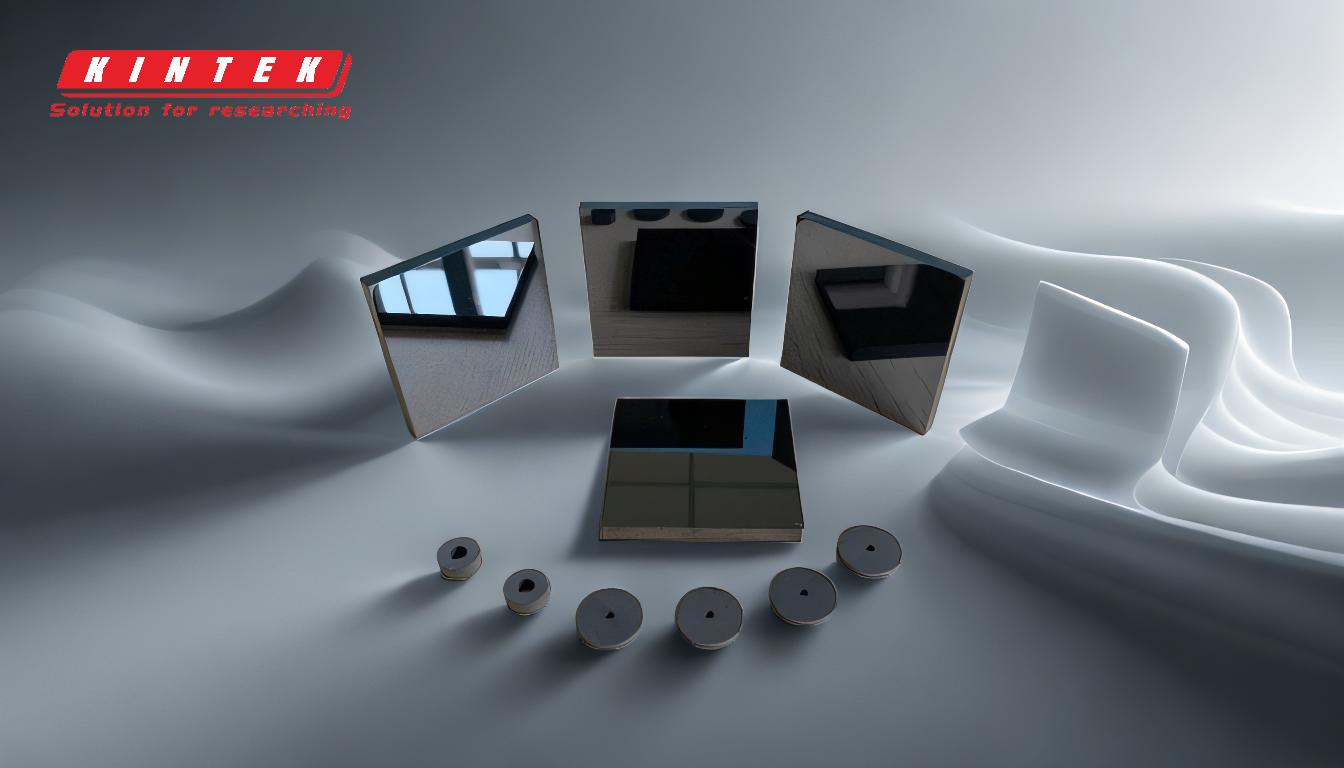
-
Types of Carbide Tool Coatings
Carbide tool coatings are categorized based on their composition and properties. The most common types include:- Titanium Nitride (TiN): A gold-colored coating that improves hardness and wear resistance. It is widely used for general-purpose cutting tools.
- Titanium Carbonitride (TiCN): A grayish coating with higher hardness and better wear resistance than TiN, ideal for high-speed machining.
- Aluminum Titanium Nitride (AlTiN): A high-performance coating with excellent heat resistance, suitable for dry machining and high-temperature applications.
- Diamond-Like Carbon (DLC): A low-friction coating that reduces wear and improves surface finish, often used for non-ferrous materials.
- Chromium Nitride (CrN): A corrosion-resistant coating that performs well in wet and corrosive environments.
-
Equipment Used for Coating Application
The application of carbide tool coatings requires specialized equipment to ensure precision and consistency. Key equipment includes:- HVOF Thermal Spray Equipment: High-Velocity Oxygen Fuel (HVOF) systems are used to apply coatings with high density and adhesion. This method is ideal for tungsten carbide coatings due to its ability to produce a uniform and durable layer.
- Robots and X-Y Gun Manipulators: Automated systems ensure accurate and repeatable coating application, especially for complex tool geometries.
- Overhead Cranes: Used for handling heavy tools and fixtures during the coating process.
- Custom-Built Fixtures: Designed for repetitive production, these fixtures ensure consistent coating application across multiple tools.
- Masking Fixtures: Protect uncoated areas of the tool, ensuring that only the intended surfaces receive the coating.
-
Benefits of Carbide Tool Coatings
- Enhanced Tool Life: Coatings reduce wear and extend the lifespan of cutting tools, reducing the need for frequent replacements.
- Improved Performance: Coatings reduce friction and heat generation, allowing for higher cutting speeds and better surface finishes.
- Cost Efficiency: By increasing tool durability and reducing downtime, coatings contribute to overall cost savings in manufacturing processes.
-
Application Considerations
- Material Compatibility: The choice of coating depends on the material being machined and the operating conditions.
- Coating Thickness: Optimal thickness ensures a balance between performance and tool geometry.
- Surface Preparation: Proper cleaning and surface treatment are critical for achieving strong adhesion and uniform coatings.
In summary, carbide tool coatings play a vital role in modern machining by enhancing tool performance and longevity. The use of advanced equipment, such as HVOF thermal spray systems and robotic manipulators, ensures high-quality and consistent coatings tailored to specific applications. Understanding the types of coatings and their benefits helps manufacturers select the right solution for their machining needs.
Summary Table:
Coating Type | Properties | Applications |
---|---|---|
Titanium Nitride (TiN) | Gold-colored, improves hardness and wear resistance | General-purpose cutting tools |
Titanium Carbonitride (TiCN) | Grayish, higher hardness and wear resistance than TiN | High-speed machining |
Aluminum Titanium Nitride (AlTiN) | High-performance, excellent heat resistance | Dry machining, high-temperature applications |
Diamond-Like Carbon (DLC) | Low-friction, reduces wear, improves surface finish | Non-ferrous materials |
Chromium Nitride (CrN) | Corrosion-resistant, performs well in wet and corrosive environments | Wet and corrosive environments |
Discover the perfect carbide tool coating for your needs—contact our experts today!