Sieving is a fundamental process used in various industries to separate particles based on size. The method involves passing material through a mesh or sieve, allowing smaller particles to pass through while retaining larger ones. Different types of sieving techniques are employed depending on the material properties, desired particle size distribution, and application requirements. These techniques include dry sieving, wet sieving, air jet sieving, and sonic sieving, each with unique advantages and applications. Understanding these methods is crucial for selecting the right sieving approach for specific materials and achieving optimal separation efficiency.
Key Points Explained:
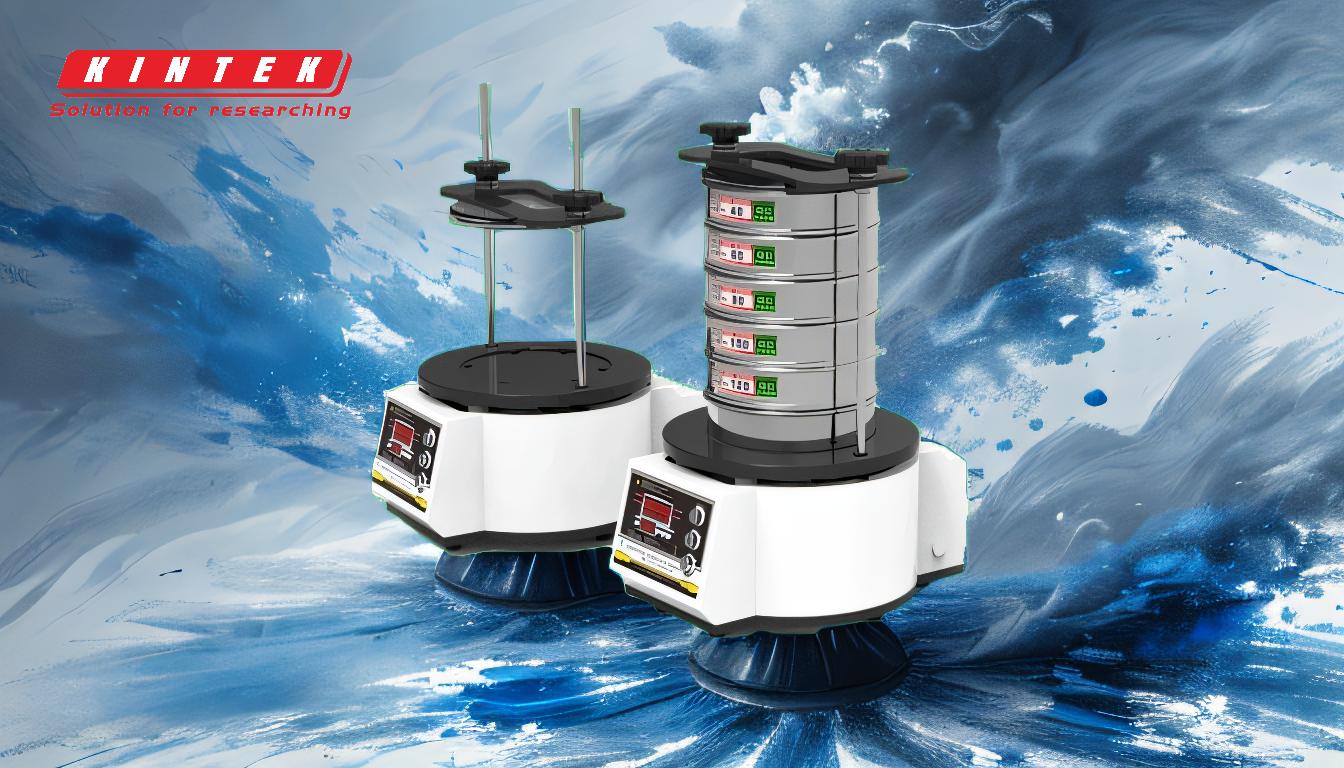
-
Dry Sieving
- Definition: Dry sieving is the most common and straightforward sieving method, where dry materials are passed through a sieve without the use of liquids.
- Process: The material is placed on the top sieve of a stack, and mechanical agitation (shaking or tapping) is applied to allow particles to pass through the mesh.
- Applications: Ideal for free-flowing, dry materials such as powders, granules, and aggregates. Commonly used in construction, agriculture, and food industries.
- Advantages: Simple, cost-effective, and suitable for materials that do not clump or stick together.
- Limitations: Not suitable for fine powders or materials prone to static charges, as these can clog the mesh.
-
Wet Sieving
- Definition: Wet sieving involves the use of water or other liquids to aid in the separation of particles, particularly for materials that are difficult to sieve in a dry state.
- Process: The material is mixed with water and poured onto the sieve. The liquid helps disperse the particles and carry fine particles through the mesh.
- Applications: Used for fine powders, clays, and materials that tend to agglomerate or form lumps. Common in soil analysis, mineral processing, and pharmaceutical industries.
- Advantages: Effective for fine and sticky materials, reduces clogging, and improves separation accuracy.
- Limitations: Requires additional equipment for liquid handling and drying of the sieved material.
-
Air Jet Sieving
- Definition: Air jet sieving uses a stream of air to assist in the separation of particles, particularly for fine powders that are challenging to sieve using traditional methods.
- Process: The material is placed on a sieve, and a controlled air stream is directed through the mesh to dislodge fine particles and carry them through.
- Applications: Suitable for fine powders in industries such as pharmaceuticals, cosmetics, and chemicals.
- Advantages: High precision for fine particles, minimizes clogging, and reduces sieving time.
- Limitations: Requires specialized equipment and may not be suitable for coarse or heavy materials.
-
Sonic Sieving
- Definition: Sonic sieving employs ultrasonic vibrations to enhance the sieving process, particularly for materials that are difficult to separate using conventional methods.
- Process: Ultrasonic waves are applied to the sieve, causing the mesh to vibrate at high frequencies. This helps dislodge fine particles and prevents clogging.
- Applications: Ideal for fine and sticky materials, such as pigments, ceramics, and certain food products.
- Advantages: Improves sieving efficiency, reduces clogging, and is suitable for a wide range of particle sizes.
- Limitations: Requires specialized ultrasonic equipment and may be more expensive than traditional sieving methods.
-
Considerations for Selecting a Sieving Method
- Material Properties: The choice of sieving method depends on the material's characteristics, such as particle size, moisture content, and tendency to agglomerate.
- Application Requirements: The desired particle size distribution and the level of precision required influence the selection of the sieving technique.
- Equipment Availability: The availability of specialized equipment, such as air jet or sonic sieving machines, may limit the choice of method.
- Cost and Efficiency: Factors such as cost, time, and energy efficiency should be considered when selecting a sieving method.
By understanding the different types of sieving and their respective advantages and limitations, equipment and consumable purchasers can make informed decisions to optimize their processes and achieve the desired particle separation outcomes.
Summary Table:
Sieving Method | Process | Applications | Advantages | Limitations |
---|---|---|---|---|
Dry Sieving | Mechanical agitation of dry materials through a sieve. | Free-flowing powders, granules, aggregates (construction, agriculture, food). | Simple, cost-effective, no liquid required. | Not suitable for fine powders or static-prone materials. |
Wet Sieving | Uses water or liquids to disperse and separate particles. | Fine powders, clays, agglomerated materials (soil analysis, mineral processing, pharmaceuticals). | Effective for sticky materials, reduces clogging. | Requires liquid handling and drying equipment. |
Air Jet Sieving | Air stream dislodges fine particles through the sieve. | Fine powders (pharmaceuticals, cosmetics, chemicals). | High precision, minimizes clogging, faster sieving. | Requires specialized equipment; not for coarse materials. |
Sonic Sieving | Ultrasonic vibrations enhance particle separation. | Fine, sticky materials (pigments, ceramics, food products). | Improves efficiency, reduces clogging, versatile. | Requires ultrasonic equipment; higher cost. |
Need help selecting the right sieving method for your materials? Contact our experts today for personalized advice!