Sputtering is a versatile thin film deposition technique widely used in industries such as semiconductors, optical devices, and data storage. It involves ejecting atoms from a target material onto a substrate to form a thin film. The process is characterized by strong adhesion, excellent step coverage, and high reproducibility, making it suitable for mass production. There are several types of sputtering, including DC diode sputtering, RF sputtering, magnetron sputtering, ion beam sputtering, and reactive sputtering. Each method has unique advantages, such as high deposition rates, precise control, and the ability to deposit a wide range of materials, including metals, oxides, and compounds. These techniques are chosen based on the specific requirements of the application, such as the type of material, substrate, and desired film properties.
Key Points Explained:
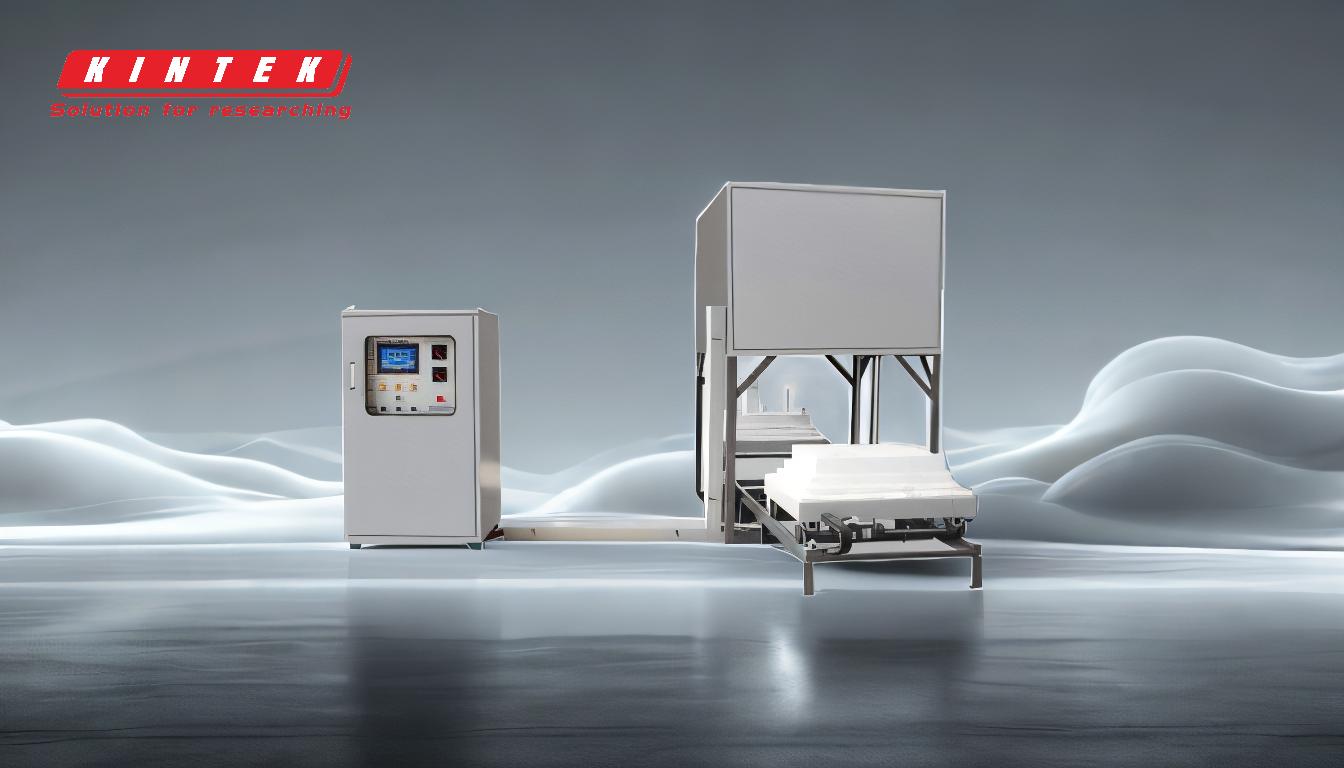
-
DC Diode Sputtering:
- Process: Involves applying a DC voltage (500-1000 V) to ignite an argon low-pressure plasma between the target and substrate. Positive argon ions bombard the target, ejecting atoms that deposit onto the substrate.
- Advantages: Simple setup, effective for conductive materials.
- Limitations: Not suitable for insulating materials due to charge buildup.
-
RF Sputtering:
- Process: Uses a high-frequency alternating field instead of a DC electric field. The alternating field prevents charge buildup, making it suitable for insulating and semiconducting materials.
- Advantages: Can sputter insulators, reduced substrate heating, higher sputtering rates at lower pressures.
- Applications: Ideal for depositing dielectric films in microelectronics.
-
Magnetron Sputtering:
- Process: Utilizes magnetic fields to confine electrons near the target, increasing ionization and sputtering efficiency.
- Advantages: High deposition rates, precise control, versatile for depositing metals, oxides, and nitrides.
- Applications: Widely used in microelectronics, semiconductor devices, and optical coatings.
-
Ion Beam Sputtering:
- Process: A focused ion beam bombards the target, ejecting atoms that deposit onto the substrate. The process occurs in a high-vacuum environment.
- Advantages: High precision, excellent film quality, and minimal contamination.
- Applications: Used for high-precision optical coatings and research applications.
-
Reactive Sputtering:
- Process: Involves introducing a reactive gas (e.g., oxygen or nitrogen) into the sputtering chamber. The gas reacts with the sputtered material to form compound films (e.g., oxides or nitrides).
- Advantages: Enables deposition of compound films with tailored properties.
- Applications: Used for depositing optical coatings, hard coatings, and semiconductor films.
-
Key Traits of Sputtering:
- Strong Adhesion: Ensures durable and long-lasting films.
- Excellent Step Coverage: Uniform deposition over complex geometries.
- High Reproducibility: Consistent results for mass production.
- Alloy Film Deposition: Capability to deposit multi-component films.
- Low Target Replacement Frequency: Reduces operational costs.
-
Applications of Sputtering:
- Semiconductors: Deposition of conductive and insulating layers.
- Optical Devices: Anti-reflective and reflective coatings.
- Data Storage: Thin films for CDs and disk drives.
- Research and Development: High-precision coatings for advanced materials.
By understanding the different types of sputtering and their unique advantages, equipment and consumable purchasers can select the most appropriate technique for their specific application, ensuring optimal performance and cost-effectiveness.
Summary Table:
Type of Sputtering | Key Advantages | Applications |
---|---|---|
DC Diode Sputtering | Simple setup, effective for conductive materials | Conductive thin films |
RF Sputtering | Can sputter insulators, reduced substrate heating | Dielectric films in microelectronics |
Magnetron Sputtering | High deposition rates, precise control | Microelectronics, optical coatings |
Ion Beam Sputtering | High precision, excellent film quality | High-precision optical coatings, research |
Reactive Sputtering | Enables deposition of compound films | Optical coatings, hard coatings |
Need help selecting the right sputtering technique for your application? Contact our experts today!