Ball mill grinding, while widely used in various industries, has several notable disadvantages that can impact efficiency, cost, and material quality. These include slow processing speeds, high energy consumption, noise and vibration issues, limitations in handling certain types of materials, and potential contamination due to wear and tear. Understanding these drawbacks is crucial for equipment purchasers to make informed decisions and explore alternative grinding methods when necessary.
Key Points Explained:
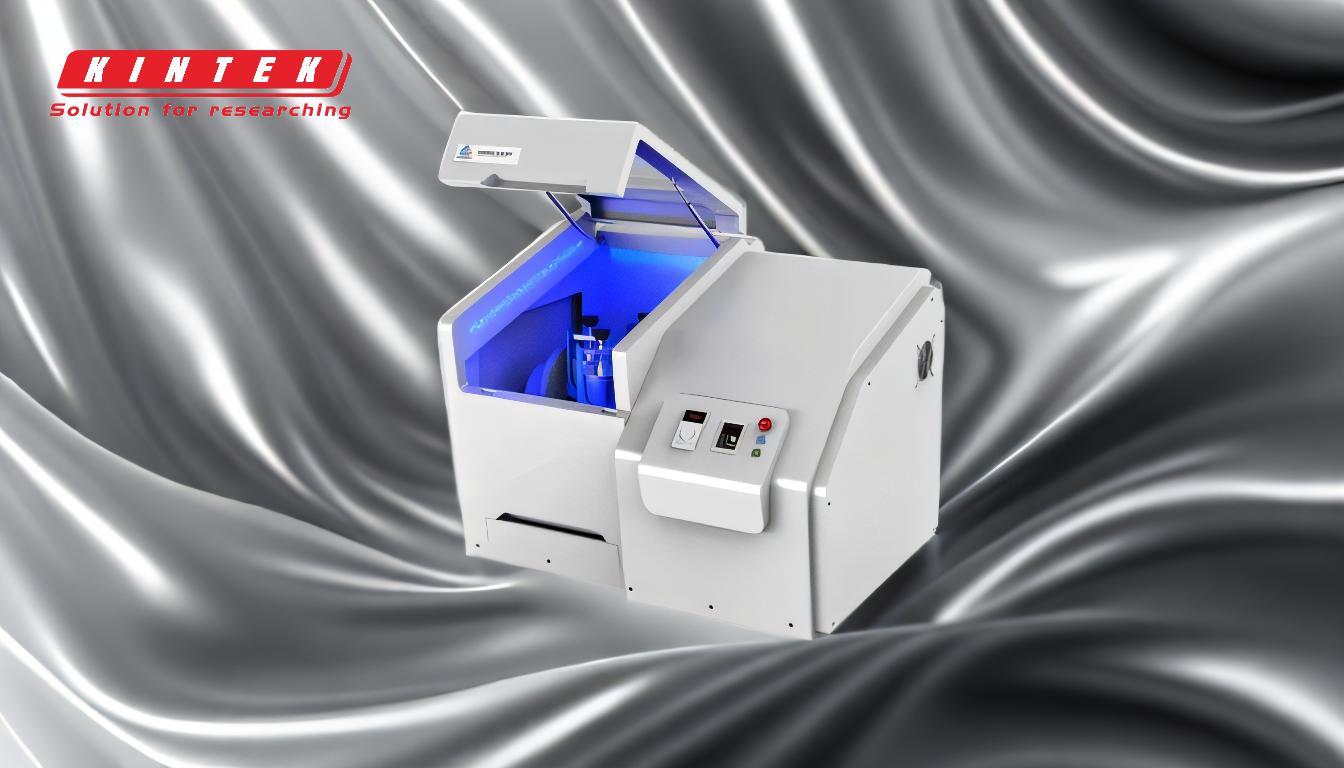
-
Slow Processing Speed
- Ball mills are inherently slow in grinding materials compared to other grinding methods. This is due to the reliance on the cascading and tumbling motion of grinding media (balls) to break down particles.
- The slow speed can lead to bottlenecks in production lines, especially in industries requiring high throughput or rapid material processing.
- For time-sensitive operations, this inefficiency can result in increased operational costs and delays.
-
High Energy Consumption
- Ball mills consume a significant amount of energy, primarily due to the wear of grinding balls and the internal lining (wall armor) of the mill.
- Friction between the grinding media and the material being processed generates heat, further contributing to energy loss.
- The high specific energy consumption makes ball mills less cost-effective in the long run, particularly for large-scale operations.
-
Noise and Vibration During Operation
- Ball mills produce strong vibrations and noise during operation, which can be disruptive in industrial settings.
- While rubber balls can reduce noise levels to some extent, the issue remains a significant drawback, especially in environments where noise pollution is a concern.
- Excessive vibration can also lead to structural wear and tear on the mill and surrounding equipment, increasing maintenance costs.
-
Limitations in Handling Certain Materials
- Ball mills are not well-suited for grinding soft, tacky, fibrous, or heat-sensitive materials.
- Soft and tacky materials can gum up the grinder walls and sieves, requiring frequent stoppages for cleaning, which disrupts workflow.
- Heat-sensitive materials may degrade or lose their properties due to the heat generated during grinding.
- Fibrous materials can clog the mill, reducing efficiency and increasing downtime.
-
Potential Contamination Due to Wear and Tear
- The continuous wear of grinding balls and the internal lining of the mill can lead to contamination of the processed material.
- This is particularly problematic in industries requiring high-purity products, such as pharmaceuticals or food processing.
- Contamination can compromise product quality and safety, leading to additional costs for filtration or purification processes.
-
Large Size and Weight
- Ball mills are often bulky and heavy, making them difficult to transport and install.
- Their unhandiness can pose logistical challenges, especially in facilities with limited space or those requiring frequent relocation of equipment.
- The large size also limits their use in smaller-scale operations or applications where portability is essential.
-
Limited Capacity for Handling Large Quantities
- Ball mills have a limited capacity for processing large quantities of material efficiently.
- Scaling up production often requires multiple mills, which increases capital and operational expenses.
- This limitation makes ball mills less suitable for industries with high-volume processing needs.
By understanding these disadvantages, equipment purchasers can better evaluate whether a ball mill is the right choice for their specific application or if alternative grinding methods should be considered.
Summary Table:
Disadvantage | Impact |
---|---|
Slow Processing Speed | Bottlenecks in production, increased costs, and delays. |
High Energy Consumption | Reduced cost-effectiveness, especially for large-scale operations. |
Noise and Vibration | Disruptive in industrial settings, increases maintenance costs. |
Material Handling Limitations | Unsuitable for soft, tacky, fibrous, or heat-sensitive materials. |
Contamination Risks | Compromises product quality, especially in high-purity industries. |
Large Size and Weight | Logistical challenges, limited portability. |
Limited Capacity for Large Quantities | Requires multiple mills, increasing costs for high-volume operations. |
Need help choosing the right grinding solution? Contact our experts today for tailored advice!