Roller mills, while widely used in various industries for grinding and processing materials, have several disadvantages that can impact their efficiency, cost-effectiveness, and suitability for certain applications. These drawbacks include high initial investment costs, significant energy consumption, limitations in processing certain types of materials, and maintenance challenges. Additionally, roller mills may not be ideal for materials that require fine or ultra-fine grinding, and they can produce heat during operation, which may affect heat-sensitive materials. Below, we explore these disadvantages in detail to provide a comprehensive understanding of the limitations associated with roller mills.
Key Points Explained:
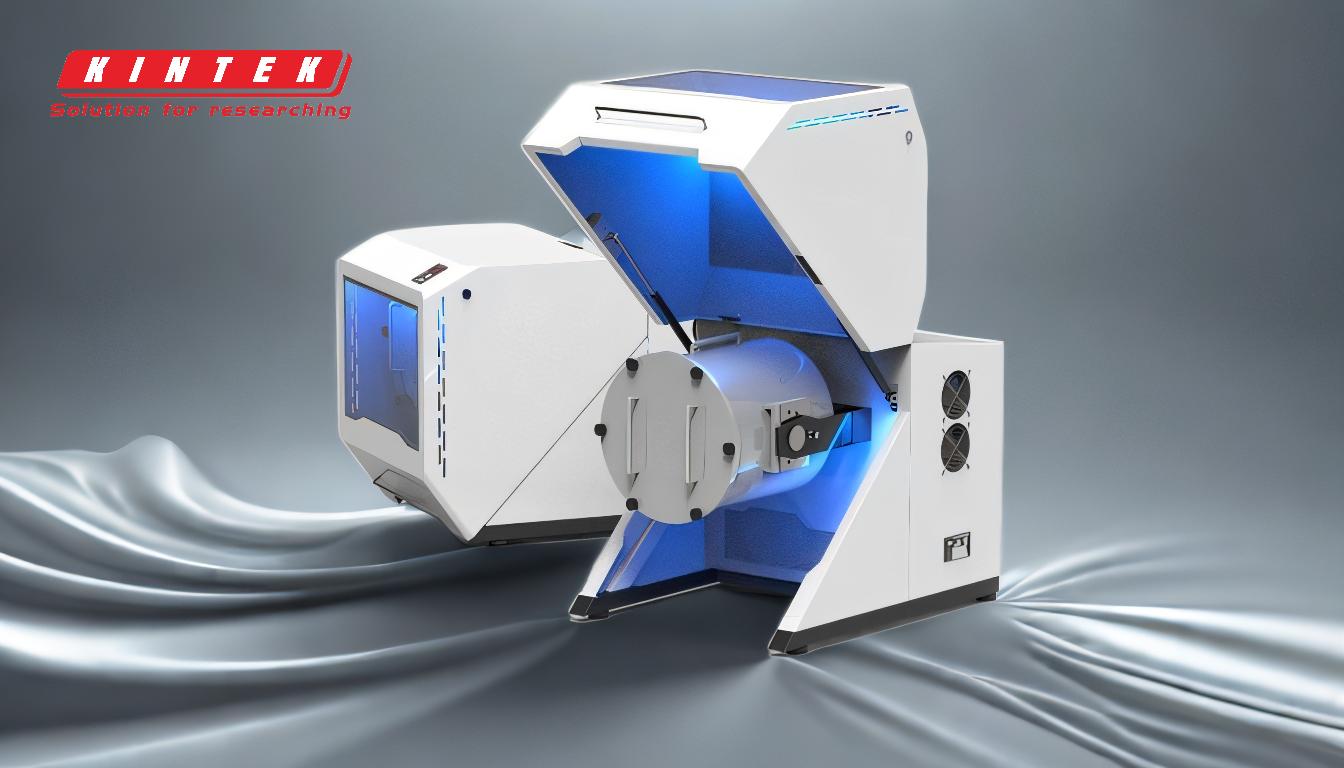
-
High Initial Investment Costs
- Roller mills require a significant upfront investment due to the complexity of their design and the need for robust construction to handle heavy-duty grinding tasks.
- The cost of purchasing and installing roller mills can be prohibitive for small-scale operations or businesses with limited budgets.
-
High Energy Consumption
- Roller mills are energy-intensive machines, particularly when used for grinding hard or abrasive materials.
- The energy demands can lead to increased operational costs, making them less economical for certain applications compared to alternative grinding technologies.
-
Material Limitations
- Roller mills may not be suitable for processing materials that are elastic, sticky, wet, or heat-sensitive.
- For example, sticky or wet materials can clog the rollers, while heat-sensitive materials may degrade due to the heat generated during grinding.
- Light or fluffy materials may not be effectively processed, as they require specialized milling techniques like jet milling.
-
Maintenance Challenges
- The rollers and other components of roller mills are subject to wear and tear, especially when grinding abrasive materials.
- Regular maintenance is required to ensure optimal performance, which can increase downtime and operational costs.
- Replacing worn-out parts can be expensive and time-consuming.
-
Heat Generation During Operation
- The friction between the rollers and the material being processed can generate significant heat, which may adversely affect heat-sensitive materials.
- This heat generation can also lead to thermal expansion of the rollers, potentially affecting the precision of the grinding process.
-
Limited Suitability for Fine or Ultra-Fine Grinding
- Roller mills are generally better suited for coarse or medium grinding tasks.
- Achieving fine or ultra-fine particle sizes may require additional processing steps or alternative milling technologies, such as jet milling or ball milling.
-
Noise and Vibration
- Roller mills can produce significant noise and vibration during operation, which may require additional measures to mitigate, such as soundproofing or vibration dampening systems.
- This can increase the complexity and cost of installation and operation.
-
Space Requirements
- Roller mills are typically large and require substantial floor space for installation and operation.
- This can be a limitation for facilities with limited space or those looking to optimize their layout for efficiency.
-
Environmental Considerations
- The high energy consumption of roller mills contributes to a larger carbon footprint, which may be a concern for environmentally conscious businesses.
- Dust generation during grinding can also pose environmental and health hazards, requiring effective dust collection and filtration systems.
-
Alternative Technologies May Be More Suitable
- For certain applications, alternative grinding technologies such as jet milling, ball milling, or hammer milling may offer advantages over roller mills.
- For example, jet milling is better suited for fine or ultra-fine grinding of heat-sensitive or light materials, while hammer mills may be more cost-effective for coarse grinding tasks.
In conclusion, while roller mills are versatile and widely used, their disadvantages—such as high costs, energy demands, material limitations, and maintenance challenges—make them less suitable for certain applications. Businesses should carefully evaluate their specific needs and consider alternative technologies when roller mills do not align with their operational goals or constraints.
Summary Table:
Disadvantage | Key Details |
---|---|
High Initial Investment Costs | Significant upfront costs due to complex design and robust construction. |
High Energy Consumption | Energy-intensive, leading to increased operational costs. |
Material Limitations | Not suitable for elastic, sticky, wet, or heat-sensitive materials. |
Maintenance Challenges | Regular wear and tear, requiring costly and time-consuming maintenance. |
Heat Generation During Operation | Friction generates heat, affecting heat-sensitive materials and roller precision. |
Limited Suitability for Fine Grinding | Better suited for coarse or medium grinding; fine grinding requires alternatives. |
Noise and Vibration | Requires soundproofing or vibration dampening, increasing costs. |
Space Requirements | Large size requires substantial floor space. |
Environmental Considerations | High energy use and dust generation pose environmental and health risks. |
Alternative Technologies | Jet milling, ball milling, or hammer milling may be better for specific tasks. |
Need help choosing the right milling solution for your needs? Contact our experts today!