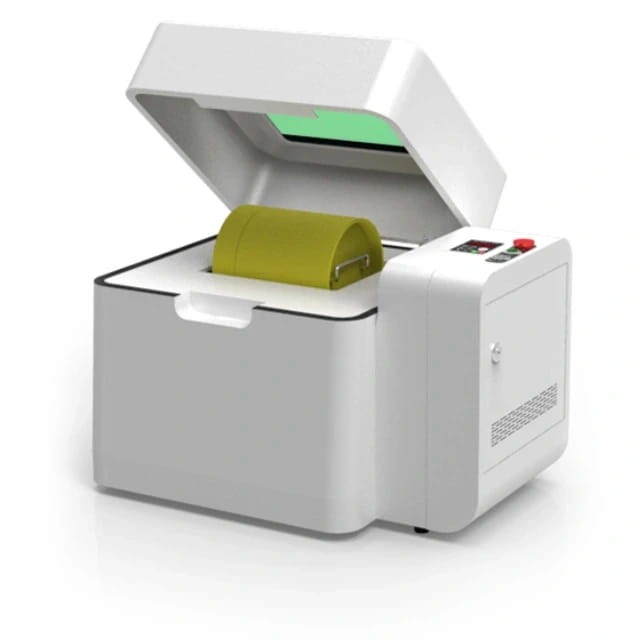
Milling Equipment
Laboratory Single Horizontal Jar Mill
Item Number : KT-JM3000
Price varies based on specs and customizations
- Processing principle
- Friction
- Application sample features
- Fine | Medium to low hardness | Brittle | Dry or low viscous
- Maximum injection size
- < 5 mm
- Sample particle size range
- 1-20um
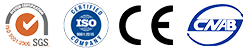
Shipping:
Contact us to get shipping details Enjoy On-time Dispatch Guarantee.
Why Choose Us
Reliable PartnerEasy ordering process, quality products, and dedicated support for your business success.
Introduction
KT-JM3000 is a mixing and grinding instrument for placing a ball milling tank with a volume of 3000ml or less. It adopts frequency conversion control to realize timing, constant speed, direction change, overload protection and other functions. It also has electric control of rubber roller movement, quick replacement of rubber rollers and safety protection cover. The product is small in size, light in weight, easy to operate, easy to use and long in service life. It is one of the products widely used in laboratory sample mixing and grinding.
Principle
The Single Horizontal Jar Mill operates by using a horizontal grinding chamber filled with grinding media. As the mill rotates, the media impacts and grinds the material, achieving efficient size reduction and dispersion through continuous, controlled motion. This method ensures minimal contamination and high-quality particle size distribution.
Applications
The Single Horizontal Jar Mill is a versatile piece of laboratory equipment designed for grinding and mixing materials in various research and industrial settings. This mill is particularly useful for applications that require fine particle size reduction and homogenization. Here are the main application areas of the Single Horizontal Jar Mill:
- Material Science: Used for grinding and preparing samples for analysis in material science research, including ceramics, composites, and metallic alloys.
- Pharmaceuticals: Essential for the fine grinding of pharmaceutical ingredients to ensure uniform particle size distribution, which is critical for drug efficacy and stability.
- Chemical Processing: Ideal for mixing and grinding chemicals in the production of fine chemicals, pigments, and catalysts.
- Food and Beverage Industry: Utilized for the grinding of food ingredients to achieve the desired texture and consistency in products like spices, powders, and instant mixes.
- Environmental Studies: Used for the preparation of soil and sediment samples for environmental analysis, ensuring that the samples are finely ground for accurate testing.
- Mineral Processing: Effective in the grinding of minerals and ores for further processing or analysis in the mining industry.
- Cosmetics: Helps in the preparation of cosmetic powders and creams by grinding and mixing various ingredients to the required fineness.
These applications highlight the Single Horizontal Jar Mill's role in facilitating precise and efficient grinding processes across multiple industries, contributing to the quality and consistency of final products.
Features
The Single Horizontal Jar Mill is a versatile and efficient tool designed for wet grinding processes, offering a range of benefits that enhance laboratory operations. This mill is particularly advantageous due to its horizontal configuration, which optimizes the use of grinding media and reduces operational costs. Here are the key features that make the Single Horizontal Jar Mill a standout choice for various applications:
- Efficient Media Utilization: The horizontal design allows for highly efficient use of media, even with sizes as small as 0.25 mm, ensuring fine grinding without excessive media consumption.
- Reduced Product Loss: With its optimized grinding mechanism, the mill minimizes product loss, contributing to higher yields and cost savings.
- Enhanced Product Quality: The mill provides maximum color strength, gloss durability, and yield, making it ideal for applications requiring high-quality end products.
- Time and Cost Savings: Process times can be reduced by up to 300%, and raw material costs can be decreased by about 5%, significantly improving operational efficiency.
- Minimal Contamination and Maintenance: The mill is designed to resist abrasion and requires relatively low maintenance, ensuring clean and efficient operation with minimal downtime.
- Consistent Performance: The predictable and consistent performance of the Single Horizontal Jar Mill makes it a reliable choice for laboratories needing precise and repeatable results.
These features not only streamline the grinding process but also enhance the overall productivity and efficiency of laboratory operations, making the Single Horizontal Jar Mill an essential tool for any modern laboratory.
Detail & Parts
Advantages
The Single Horizontal Jar Mill offers a range of advantages that make it a superior choice for laboratory and small-scale production environments. Here are some of the key benefits:
- Efficient Wet Grinding: Unlike vertical mills, horizontal mills are specifically designed for wet grinding processes. They utilize a horizontal tubular grinding chamber with an agitator shaft and disks, which efficiently transfers energy to the fluid, enhancing the grinding process.
- Precise Media Utilization: Horizontal mills can use media as small as 0.25 mm and as large as 2 mm, ensuring highly efficient use of media and leading to significant reductions in product loss and raw material costs.
- Enhanced Product Quality: These mills provide maximum color strength, gloss durability, and yield, improving the overall quality of the end product.
- Reduced Processing Time: Horizontal mills can reduce process time by up to 300%, making them highly time-efficient and suitable for applications requiring quick turnaround.
- Cost Savings: By reducing raw material costs by about 5% and minimizing solvent loss, these mills offer substantial cost savings in the long run.
- Minimal Contamination: The design of horizontal mills minimizes contamination risks, ensuring clean-up is easier and cross-contamination is reduced.
- Low Maintenance and Operation Costs: With relatively low operation, control, and maintenance requirements, horizontal mills are a cost-effective solution for grinding needs.
- Consistent Performance: The predictable and consistent performance of horizontal mills makes them ideal for applications requiring precise and repeatable results.
- Resilience to Abrasion: The construction of these mills is robust, resisting abrasion and ensuring longevity and reliability.
These advantages highlight the Single Horizontal Jar Mill's effectiveness in various applications, particularly in wet grinding scenarios where precision, efficiency, and cost-effectiveness are paramount.
Functions
- Continuous grinding
- Intermittent grinding
- Alternate grinding
- Emergency stop, timing
- Overload and dangerous operation protection
- LED Lighting
- Protective Cover
- Heat Dissipation
Technical specifications
Processing principle | Friction |
Application sample features | Fine | Medium to low hardness | Brittle | Dry or low viscous |
Processing type | grinding | mixing |
Maximum injection size | < 5 mm |
Sample particle size range | 1-20um |
Number of ball mill jars | 1 |
The largest ball milling tank volume available | 3000ml |
Available minimum milling jar volume | 250ml |
Ball mill tank optional material | Zirconia | Tungsten Carbide | Agate | Nylon Stainless Steel | Polyurethane etc |
Grinding media optional type | Spherical | Cylindrical |
Grinding ball optional material | Zirconia | Tungsten Carbide | Agate | Stainless Steel | Corundum |
Grinding method | Dry grinding | wet grinding |
Number of rubber rollers: | 2 sticks |
Rubber roller speed | 900 r/min |
Rubber roller cover material | Polyurethane |
Rubber roller movement method | electric control |
net weight | 48kg |
Dimensions | 680*430*430mm |
Protection class: | IP65 |
standard | CE |
Warnings
Operator safety is the top important issue! Please operate the equipment with cautions. Working with inflammable& explosive or toxic gases is very dangerous, operators must take all necessary precautions before starting the equipment. Working with positive pressure inside the reactors or chambers is dangerous, operator must fellow the safety procedures strictly. Extra caution must also be taken when operating with air-reactive materials, especially under vacuum. A leak can draw air into the apparatus and cause a violent reaction to occur.
Designed for You
KinTek provide deep custom made service and equipment to worldwide customers, our specialized teamwork and rich experienced engineers are capable to undertake the custom tailoring hardware and software equipment requirements, and help our customer to build up the exclusive and personalized equipment and solution!
Would you please drop your ideas to us, our engineers are ready for you now!
4.8
out of
5
With its user-friendly design, this mill is so easy to use, even for beginners!
4.9
out of
5
The quality of the jar mill is top-notch, ensuring durable and long-lasting performance!
4.7
out of
5
This jar mill is a lifesaver! It's so efficient and convenient, making my research work a breeze!
4.9
out of
5
The technological advancements in this mill are remarkable. It's a game-changer for our laboratory!
4.6
out of
5
This jar mill is worth every penny. Its high-quality materials and construction ensure years of reliable service.
4.8
out of
5
The speed of delivery was incredibly fast. I had the jar mill in my lab in no time!
4.7
out of
5
This jar mill is a true value for money. Its exceptional performance and durability make it an unbeatable choice.
4.9
out of
5
The milling jars available in various materials provide great flexibility for different grinding needs.
4.6
out of
5
The adjustable speed drive allows for precise control over the grinding process, ensuring optimal results.
4.8
out of
5
The safety features, like overload protection, give me peace of mind while operating this jar mill.
4.7
out of
5
The compact design of this jar mill saves valuable bench space in my laboratory.
4.9
out of
5
The low noise operation of this jar mill creates a pleasant working environment in our lab.
4.6
out of
5
The versatility of this jar mill allows me to grind a wide range of materials with ease.
4.8
out of
5
The intuitive control panel makes operating this jar mill a breeze, even for new users.
4.7
out of
5
The after-sales support from KINTEK SOLUTION is exceptional, ensuring prompt assistance whenever needed.
Products
Laboratory Single Horizontal Jar Mill
REQUEST A QUOTE
Our professional team will reply to you within one business day. Please feel free to contact us!
Related Products
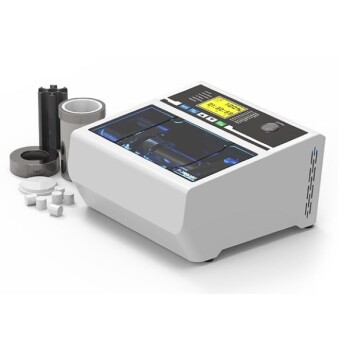
Laboratory Micro Horizontal Jar Mill for Precision Sample Preparation in Research and Analysis
Discover the Micro Horizontal Jar Mill for precise sample preparation in research and analysis. Ideal for XRD, geology, chemistry, and more.
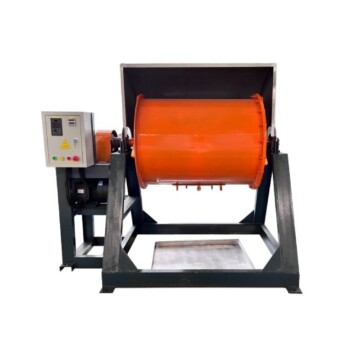
Stainless Steel Laboratory Ball Mill for Dry Powder and Liquid with Ceramic Polyurethane Lining
Discover the versatile stainless steel dry powder/liquid horizontal ball mill with ceramic/polyurethane lining. Ideal for ceramic, chemical, metallurgical, and building materials industries. High grinding efficiency and uniform particle size.
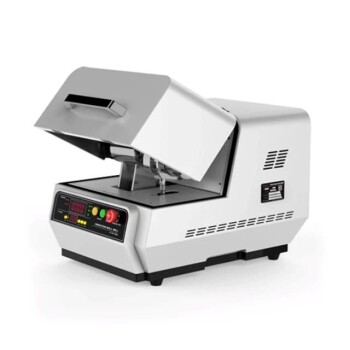
High Energy Vibratory Laboratory Ball Mill Grinding Mill Single Tank Type
High-energy vibration ball mill is a small desktop laboratory grinding instrument.It can be ball-milled or mixed with different particle sizes and materials by dry and wet methods.
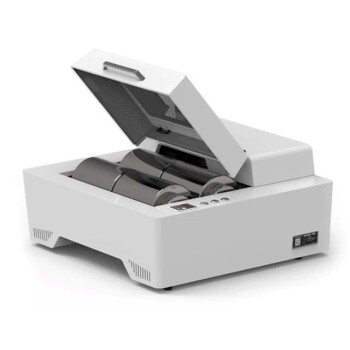
Laboratory Four-Body Horizontal Jar Mill
The four-body horizontal tank mill ball mill can be used with four horizontal ball mill tanks with a volume of 3000ml. It is mostly used for mixing and grinding laboratory samples.
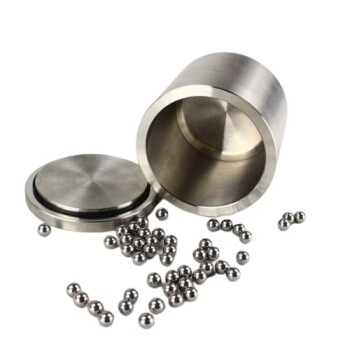
Laboratory Ball Mill Jar Mill with Metal Alloy Grinding Jar and Balls
Grind and mill with ease using metal alloy grinding jars with balls. Choose from 304/316L stainless steel or tungsten carbide and optional liner materials. Compatible with various mills and features optional functions.
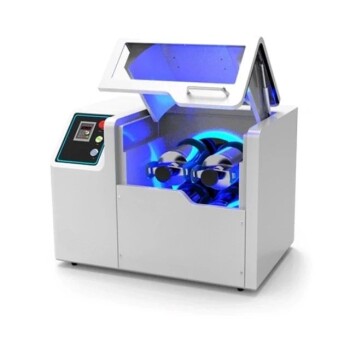
High Energy Planetary Ball Mill for Laboratory Horizontal Tank Type Milling Machine
KT-P4000H uses the unique Y-axis planetary motion trajectory, and utilizes the collision, friction and gravity between the sample and the grinding ball to have a certain anti-sinking ability, which can obtain better grinding or mixing effects and further improve the sample output.
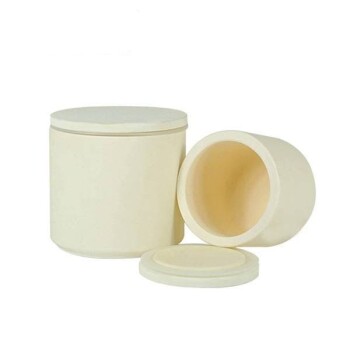
Laboratory Jar Ball Mill with Alumina Zirconia Grinding Jar and Balls
Grind to perfection with alumina/zirconia grinding jars and balls. Available in volume sizes from 50ml to 2500ml, compatible with various mills.
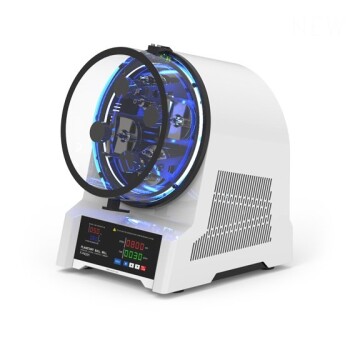
Laboratory Horizontal Planetary Ball Mill Milling Machine
Improve sample uniformity with our Horizontal Planetary Ball Mills. KT-P400H reduces sample deposition and KT-P400E has multi-directional capabilities. Safe, convenient and efficient with overload protection.
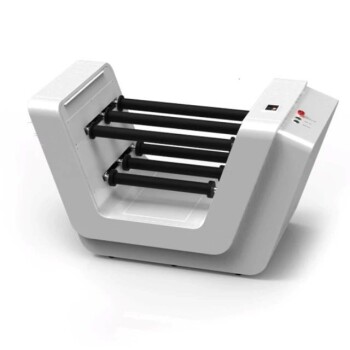
Laboratory Ten-Body Horizontal Jar Mill for Lab Use
The Ten-body horizontal jar mill is for 10 ball mill pots (3000ml or less). It has frequency conversion control, rubber roller movement, and PE protective cover.
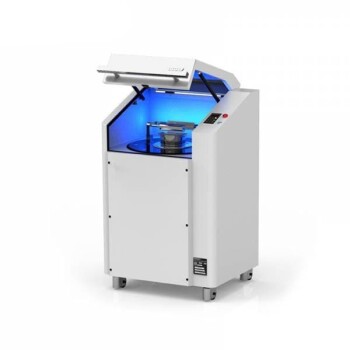
Vibration Mill for Efficient Sample Preparation, Suitable for Crushing and Grinding a Variety of Materials with Analytical Precision. Supports Dry / Wet / Cryogenic Grinding and Vacuum/Inert Gas Protection.
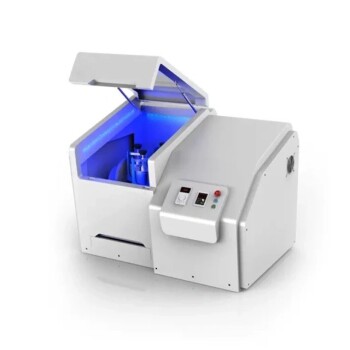
High-Energy Omnidirectional Planetary Ball Mill Milling Machine for Laboratory
The KT-P4000E is a new product derived from the vertical high-energy planetary ball mill with a 360° swivel function. Experience faster, uniform, and smaller sample output results with 4 ≤1000ml ball mill jars.
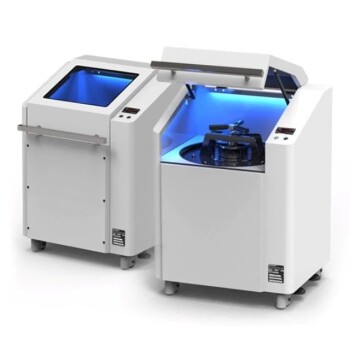
Laboratory Disc Cup Vibratory Mill for Sample Grinding
The vibrating disc mill is suitable for non-destructive crushing and fine grinding of samples with large particle sizes, and can quickly prepare samples with analytical fineness and purity.
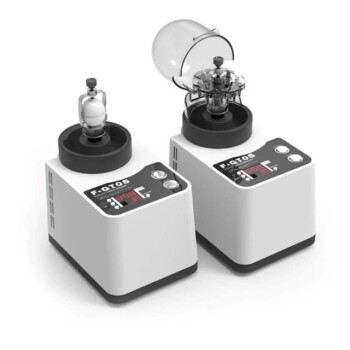
Laboratory Micro Tissue Grinding Mill Grinder
KT-MT10 is a miniature ball mill with a compact structure design. The width and depth are only 15X21 cm, and the total weight is only 8 kg. It can be used with a minimum 0.2ml centrifuge tube or a maximum 15ml ball mill jar.
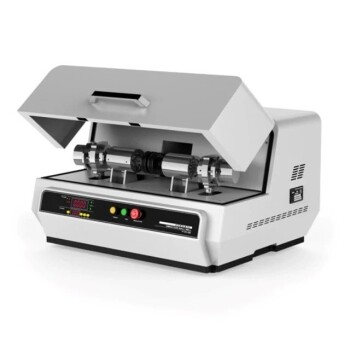
High Energy Vibratory Laboratory Ball Mill Double Tank Type
High-energy vibration ball mill is a small desktop laboratory grinding instrument. It uses 1700r/min high-frequency three-dimensional vibration to make the sample achieve the result of grinding or mixing.
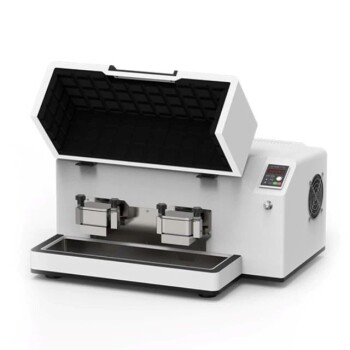
High Energy Vibratory Ball Mill for Lab Use
The high-energy vibrating ball mill is a high-energy oscillating and impacting multifunctional laboratory ball mill. The table-top type is easy to operate, small in size, comfortable and safe.
Related Articles
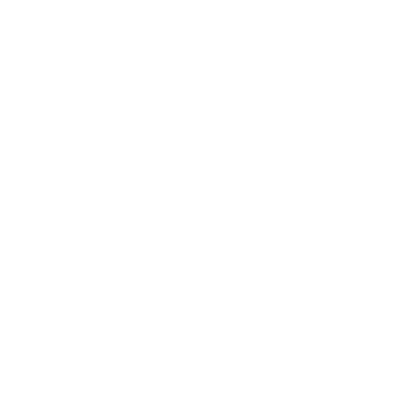
Planetary Ball Mills: Research Tools for Efficient Mixing and Nanoscale Grinding
Planetary ball mills are indispensable tools in modern laboratories, serving a crucial role in the mixing, fine grinding, and preparation of small samples. These mills are particularly adept at dispersing nanomaterials and facilitating the development and small-scale production of high-tech materials.
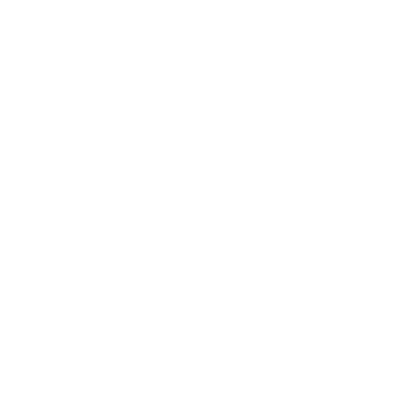
Advantages of Planetary Ball Mill in Laboratory Applications
Discover the advantages of using planetary ball mills in laboratory settings. Learn about its ability to produce fine powder, suitability for toxic materials, wide range of applications, continuous operation, and usage for milling abrasive materials. Explore how planetary ball mills differ from traditional milling machines and their function in creating ultrafine and nano-sized materials.
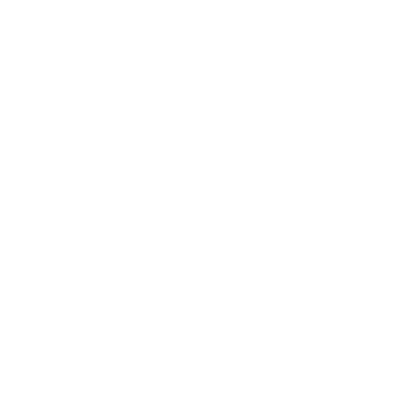
Manual Hydraulic Presses for Laboratory Use: A Comprehensive Guide
Explore the intricacies of manual hydraulic presses in labs, including operation, benefits, and comparison with automatic models. Ideal for those seeking detailed insights on sample preparation and cost-effectiveness.
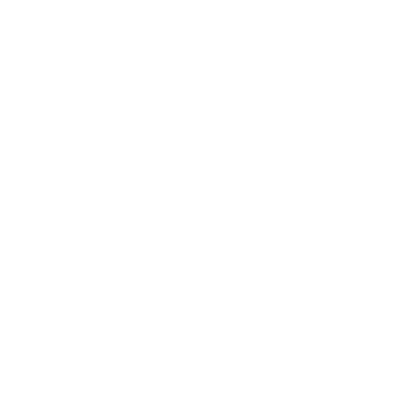
Comprehensive Guide to Filter Press Pilot Testing
Filter press pilot testing serves the purpose of collecting data necessary for accurately sizing a full-scale filter press system. This data includes various parameters such as cake solids, cake density, total processing time, processing time for each step, slurry feed solids, slurry pH, chemical conditioning dosages, and maximum operating pressure for each process step. Additionally, other data like filtrate suspended solids, slurry pH, and specific chemical analysis required by the process may also be collected.