Sieve shaker machines are widely used for particle size analysis due to their simplicity, cost-effectiveness, and ability to provide reproducible results. However, they have several notable disadvantages that can affect their accuracy, reliability, and suitability for certain materials. These include limitations in handling fine particles, assumptions about particle shape, challenges with elongated or flat particles, unsuitability for very small particles, potential particle size reduction during sieving, and issues related to sieve clogging and distortion. Understanding these drawbacks is crucial for users to make informed decisions and ensure proper maintenance and handling of the equipment.
Key Points Explained:
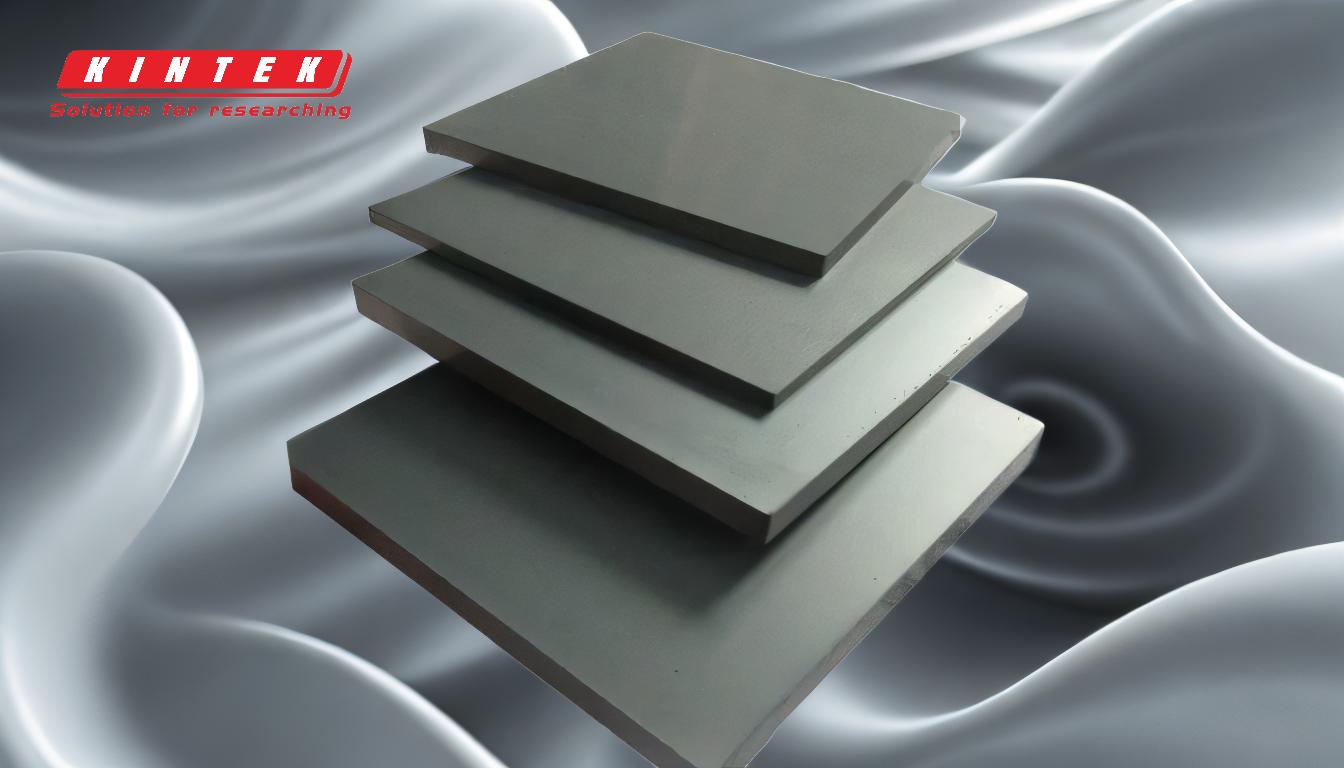
-
Reduced Accuracy for Fine Materials:
- Sieve shakers are less accurate for materials finer than 100 mesh (approximately 150 µm). This is because finer particles tend to agglomerate or adhere to the sieve mesh, leading to inaccurate results. Additionally, the vibration or motion of the shaker may not be sufficient to effectively separate these fine particles, causing them to remain on the sieve surface.
-
Assumption of Particle Shape:
- Sieve analysis assumes that all particles are round or nearly spherical. However, in reality, particles can have irregular shapes, such as elongated or flat forms. This assumption can lead to unreliable mass-based results, as non-spherical particles may not pass through the sieve openings in the same way as spherical particles, skewing the size distribution data.
-
Unsuitability for Elongated and Flat Particles:
- Elongated or flat particles can cause further inaccuracies in sieve analysis. These particles may align themselves in a way that allows them to pass through sieve openings that are smaller than their actual dimensions, leading to incorrect sizing results. This issue is particularly problematic for materials like fibers or flakes.
-
Unsuitability for Particles Smaller Than 50 µm:
- Sieve shakers are generally not suitable for analyzing particles smaller than 50 µm. At this scale, other methods like laser diffraction or sedimentation are more appropriate. The limitations of sieve shakers for such fine particles are due to the difficulty in achieving effective separation and the increased likelihood of particle agglomeration.
-
Potential Particle Size Reduction:
- During the sieving process, there is a risk of further reduction in particle size due to the mechanical action of the shaker. This can occur if particles are fragile or brittle, leading to unintended fragmentation. Such changes in particle size can introduce errors in the analysis, as the original size distribution is altered.
-
Sieve Clogging and Distortion:
- Improper handling or maintenance of sieves can lead to clogging or distortion of the mesh. Clogging occurs when particles become trapped in the sieve openings, reducing the effective area for sieving and slowing down the process. Distortion can happen if the sieve is subjected to excessive force or improper cleaning, affecting the uniformity of the mesh openings and leading to inconsistent results.
-
Variability in Mesh Weave:
- Test sieves can have variations in the weave of the mesh material, which can affect the reproducibility of results. These variations must be accounted for during data analysis, as they can introduce inconsistencies in the size distribution measurements.
-
Maintenance and Handling Requirements:
- Sieve shakers and their components require careful handling and regular maintenance to ensure accurate and reliable results. Neglecting proper cleaning, storage, or calibration can lead to issues such as clogging, distortion, or wear and tear, which can compromise the performance of the equipment.
By understanding these disadvantages, users can take appropriate measures to mitigate their impact, such as using alternative methods for fine or irregularly shaped particles, ensuring proper sieve maintenance, and accounting for mesh variability in data analysis. This awareness is essential for achieving accurate and reliable particle size analysis results.
Summary Table:
Disadvantage | Description |
---|---|
Reduced Accuracy for Fine Materials | Less accurate for particles finer than 100 mesh (150 µm) due to agglomeration and ineffective separation. |
Assumption of Particle Shape | Assumes spherical particles; irregular shapes (elongated/flat) skew size distribution results. |
Unsuitability for Elongated/Flat Particles | Elongated or flat particles may pass through smaller openings, leading to incorrect sizing. |
Unsuitability for Particles < 50 µm | Not suitable for particles smaller than 50 µm; alternative methods like laser diffraction are recommended. |
Potential Particle Size Reduction | Fragile or brittle particles may break during sieving, altering the original size distribution. |
Sieve Clogging and Distortion | Improper handling can cause clogging or mesh distortion, reducing sieving efficiency and accuracy. |
Variability in Mesh Weave | Mesh weave inconsistencies can affect reproducibility and accuracy of results. |
Maintenance and Handling Requirements | Regular cleaning, storage, and calibration are essential to prevent performance issues. |
Need help choosing the right particle size analysis method? Contact our experts today for personalized advice!