Sieving, while a widely used method for particle size analysis, has several notable disadvantages that can impact its accuracy, efficiency, and applicability. These limitations include issues with mesh variations, assumptions about particle shape, accuracy for fine materials, handling of elongated or flat particles, unsuitability for very small particles, potential particle size reduction, clogging, and limited resolution of particle size distribution. Additionally, sieving is time-consuming and only effective with dry particles. Understanding these drawbacks is crucial for selecting the appropriate method for particle size analysis and ensuring reliable results.
Key Points Explained:
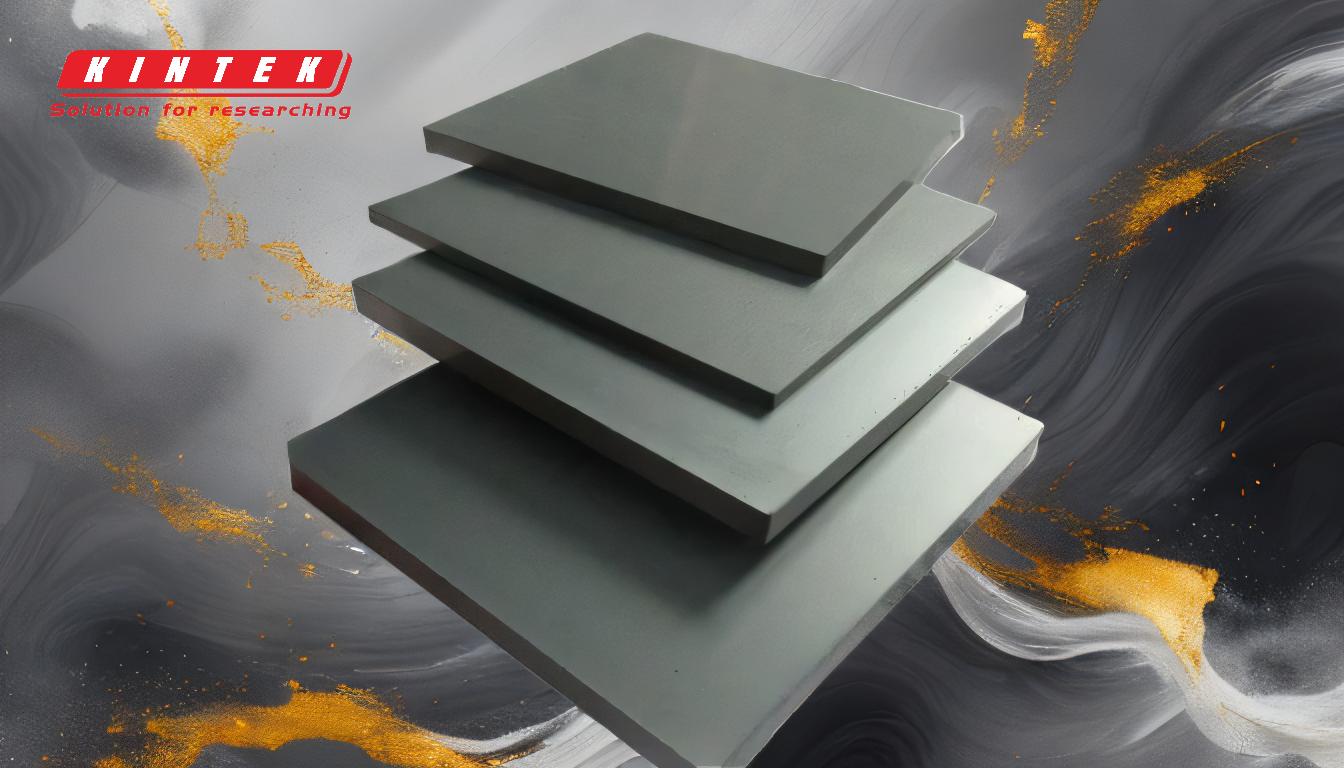
-
Variations in Mesh Weave:
- Explanation: The weave of the mesh material in sieves can vary, leading to inconsistencies in the size of the openings. This variation can affect the reproducibility of test results, as different sieves may yield slightly different particle size distributions.
- Impact: Users must account for these variations in data presentation and analysis, which can complicate the interpretation of results and reduce the reliability of the sieving method.
-
Assumption of Particle Shape:
- Explanation: Sieving assumes that all particles are round or nearly spherical. However, this is not always the case, as particles can be elongated, flat, or irregularly shaped.
- Impact: This assumption can lead to unreliable mass-based results, especially for elongated and flat particles, which may not pass through the sieve openings as expected, skewing the particle size distribution.
-
Accuracy for Fine Materials:
- Explanation: Sieving is less accurate for materials finer than 100 mesh (approximately 150 µm). Fine particles can clump together or adhere to the sieve mesh, making it difficult to achieve a true representation of their size distribution.
- Impact: This limitation can result in inaccurate data for fine materials, necessitating the use of alternative methods for precise particle size analysis.
-
Handling of Elongated and Flat Particles:
- Explanation: Elongated and flat particles may not behave as expected during sieving, leading to unreliable mass-based results. These particles can either pass through the sieve openings more easily or become trapped, depending on their orientation.
- Impact: The presence of such particles can distort the particle size distribution, making it challenging to obtain accurate and reproducible results.
-
Unsuitability for Very Small Particles:
- Explanation: Sieving is unsuitable for particles smaller than 50 µm. At this size, particles can become airborne, adhere to the sieve mesh, or pass through the openings without being accurately counted.
- Impact: This limitation restricts the applicability of sieving for very fine materials, requiring the use of more specialized techniques like laser diffraction or sedimentation analysis.
-
Potential Further Reduction in Particle Size:
- Explanation: During the sieving process, particles can undergo further size reduction due to mechanical agitation or friction. This can alter the original particle size distribution.
- Impact: The potential for particle size reduction introduces errors in the analysis, as the measured particle sizes may not reflect the true sizes of the original particles.
-
Clogging and Distortion of Sieves:
- Explanation: Sieves can become clogged with particles, especially if the material is sticky or contains moisture. Additionally, sieves can become distorted if not handled and maintained properly.
- Impact: Clogging and distortion can lead to inaccurate results and may require frequent cleaning or replacement of sieves, increasing the time and cost of analysis.
-
Limited Resolution of Particle Size Distribution:
- Explanation: Sieve analysis typically provides a limited number of size fractions, often up to 8 sieves. This restricts the resolution of the particle size distribution, as the data points are spread over a few size ranges.
- Impact: The limited resolution can make it difficult to detect subtle variations in particle size, which may be important for certain applications.
-
Time-Consuming Process:
- Explanation: Sieving can be a time-consuming process, especially when dealing with large sample sizes or materials that require extended shaking to achieve proper separation.
- Impact: The time required for sieving can be a significant drawback in situations where rapid analysis is needed, potentially delaying decision-making processes.
-
Effective Only with Dry Particles:
- Explanation: Sieving is only effective with dry particles. Moisture can cause particles to clump together or adhere to the sieve mesh, preventing accurate size separation.
- Impact: This limitation necessitates the drying of samples before analysis, adding an extra step to the process and potentially altering the properties of the particles.
In summary, while sieving is a straightforward and widely used method for particle size analysis, it has several disadvantages that can affect its accuracy, efficiency, and applicability. These limitations must be carefully considered when selecting a method for particle size analysis, especially for materials that are fine, irregularly shaped, or require high-resolution data. Alternative methods may be necessary to achieve the desired level of accuracy and reliability in certain cases.
Summary Table:
Disadvantage | Explanation | Impact |
---|---|---|
Variations in Mesh Weave | Inconsistent sieve openings affect reproducibility. | Complicates data interpretation and reduces reliability. |
Assumption of Particle Shape | Sieving assumes spherical particles, ignoring irregular shapes. | Skews results for elongated or flat particles. |
Accuracy for Fine Materials | Less accurate for particles finer than 100 mesh (~150 µm). | Inaccurate data for fine materials; alternative methods needed. |
Handling of Elongated and Flat Particles | Irregular particles may not pass through sieves as expected. | Distorts particle size distribution and reduces reproducibility. |
Unsuitability for Very Small Particles | Ineffective for particles smaller than 50 µm. | Requires specialized techniques for fine particle analysis. |
Potential Particle Size Reduction | Mechanical agitation during sieving may reduce particle size. | Alters original particle size distribution, introducing errors. |
Clogging and Distortion of Sieves | Sticky or moist particles can clog or distort sieves. | Increases maintenance time and costs, leading to inaccurate results. |
Limited Resolution of Size Distribution | Typically provides only up to 8 size fractions. | Low resolution makes detecting subtle size variations difficult. |
Time-Consuming Process | Extended shaking required for large samples or difficult materials. | Delays analysis and decision-making processes. |
Effective Only with Dry Particles | Moisture causes clumping or adhesion to sieve mesh. | Requires sample drying, adding extra steps and potentially altering results. |
Need a more accurate particle size analysis method? Contact our experts today to find the right solution for your needs!