Sputter coating, while widely used in various applications such as SEM sample preparation and thin film deposition, has several disadvantages that can affect its efficiency, cost, and the quality of the final product. These drawbacks include issues related to contamination, material limitations, process complexity, and equipment costs. Understanding these disadvantages is crucial for making informed decisions about whether sputter coating is the right technique for a specific application.
Key Points Explained:
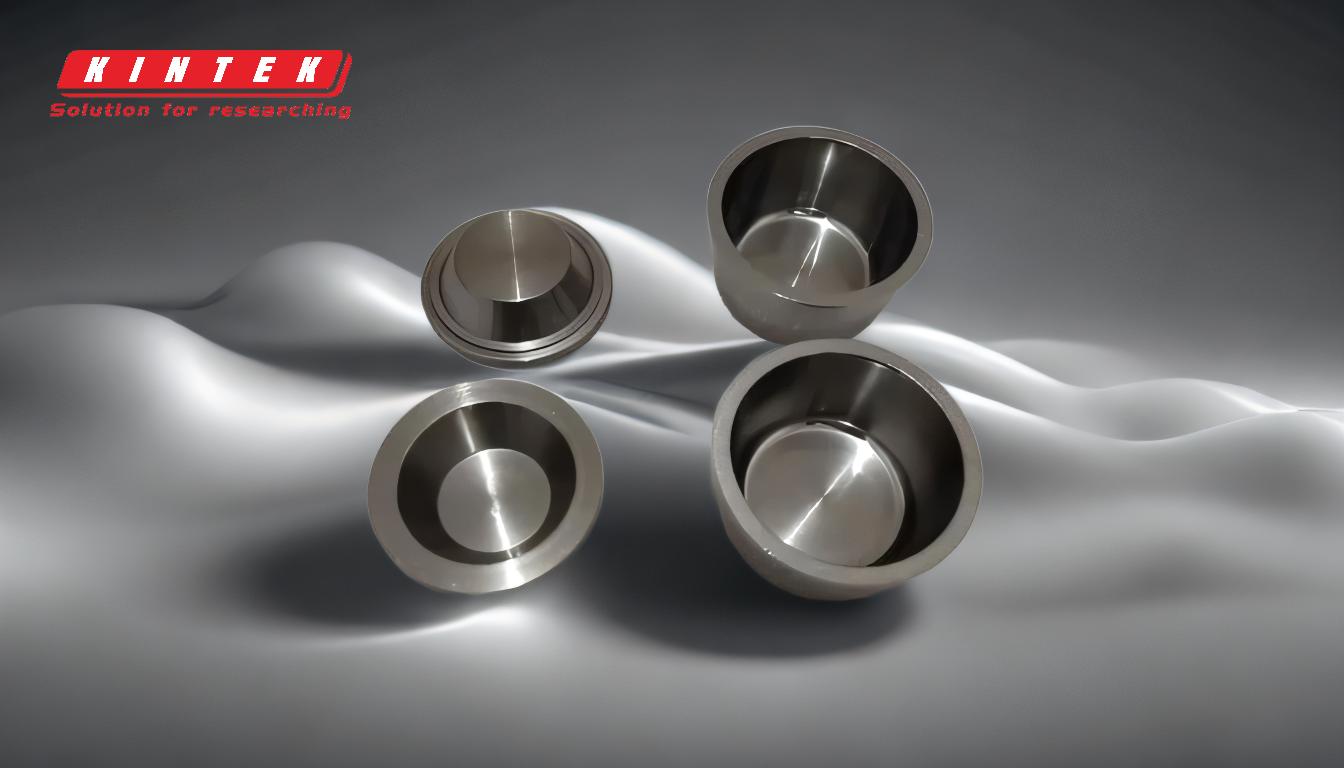
-
Film Contamination Risks:
- Impurity Diffusion: During the sputtering process, impurities from the target material or the environment can diffuse into the film, leading to contamination. This is particularly problematic in applications requiring high-purity films.
- Gaseous Contaminants: The plasma used in sputtering can activate gaseous contaminants, which then become incorporated into the film, further increasing the risk of contamination.
-
Material Limitations:
- Melting Temperature Constraints: The selection of coating materials is limited by their melting temperatures. Materials with very high melting points may not be suitable for sputter coating, restricting the range of materials that can be used.
- Target Poisoning in Reactive Sputtering: In reactive sputter deposition, the gas composition must be carefully controlled to prevent the target material from reacting with the gas, which can lead to target poisoning and reduced deposition rates.
-
Process Complexity and Control:
- Parameter Optimization: Sputter coating requires careful optimization of parameters such as pressure, power, and gas composition. This can be time-consuming and may require significant expertise.
- Layer-by-Layer Growth Control: Achieving precise control over layer-by-layer growth is challenging compared to other deposition methods like pulsed laser deposition. This can affect the quality and uniformity of the film.
-
Equipment and Operational Costs:
- Expensive Targets: Sputtering targets are often costly, and the material use can be inefficient, leading to higher operational costs.
- Cooling Requirements: A significant portion of the energy used in sputtering is converted into heat, necessitating cooling systems. This not only increases energy costs but also reduces the production rate.
-
Film Quality and Uniformity:
- Non-Uniform Deposition Flux: The deposition flux in sputtering is often non-uniform, requiring the use of moving fixtures to achieve uniform film thickness. This adds complexity to the process.
- Altered Surface Topography: In some cases, sputter coating can alter the surface topography of the sample, which may be undesirable in applications where surface integrity is critical.
- Loss of Atomic Number-Contrast: The coating material can replace the original surface, leading to a loss of atomic number-contrast, which can be a significant drawback in SEM imaging.
-
Integration with Other Processes:
- Lift-Off Process Challenges: Sputter deposition is difficult to combine with lift-off processes for film structuring due to the diffuse transport of sputtered atoms. This can lead to contamination issues and makes full shadowing impossible.
- Inert Gas Impurities: Inert sputtering gases can become impurities in the growing film, affecting its properties and performance.
In summary, while sputter coating offers several advantages, such as the ability to deposit a wide range of materials and achieve good adhesion, it also comes with significant disadvantages. These include contamination risks, material limitations, process complexity, high equipment and operational costs, challenges in achieving uniform film quality, and difficulties in integrating with other processes. Careful consideration of these factors is essential when deciding whether sputter coating is the appropriate technique for a given application.
Summary Table:
Disadvantages of Sputter Coating | Key Challenges |
---|---|
Film Contamination Risks | Impurity diffusion, gaseous contaminants |
Material Limitations | Melting temperature constraints, target poisoning |
Process Complexity | Parameter optimization, layer-by-layer growth control |
High Equipment Costs | Expensive targets, cooling requirements |
Film Quality Issues | Non-uniform deposition, altered surface topography |
Integration Challenges | Lift-off process difficulties, inert gas impurities |
Need help deciding if sputter coating is right for your application? Contact our experts today for tailored advice!