The sputtering process, while widely used for thin-film deposition, has several notable disadvantages. These include low deposition rates, high capital and operational costs, film contamination risks, and challenges in material compatibility. Additionally, sputtering can lead to inefficient material usage, non-uniform film thickness, and difficulties in integrating with certain fabrication processes like lift-off. The process also generates significant heat, requiring robust cooling systems, and is less effective for insulating materials. These drawbacks make sputtering less suitable for specific applications, particularly those requiring high precision, cost-effectiveness, or compatibility with sensitive materials.
Key Points Explained:
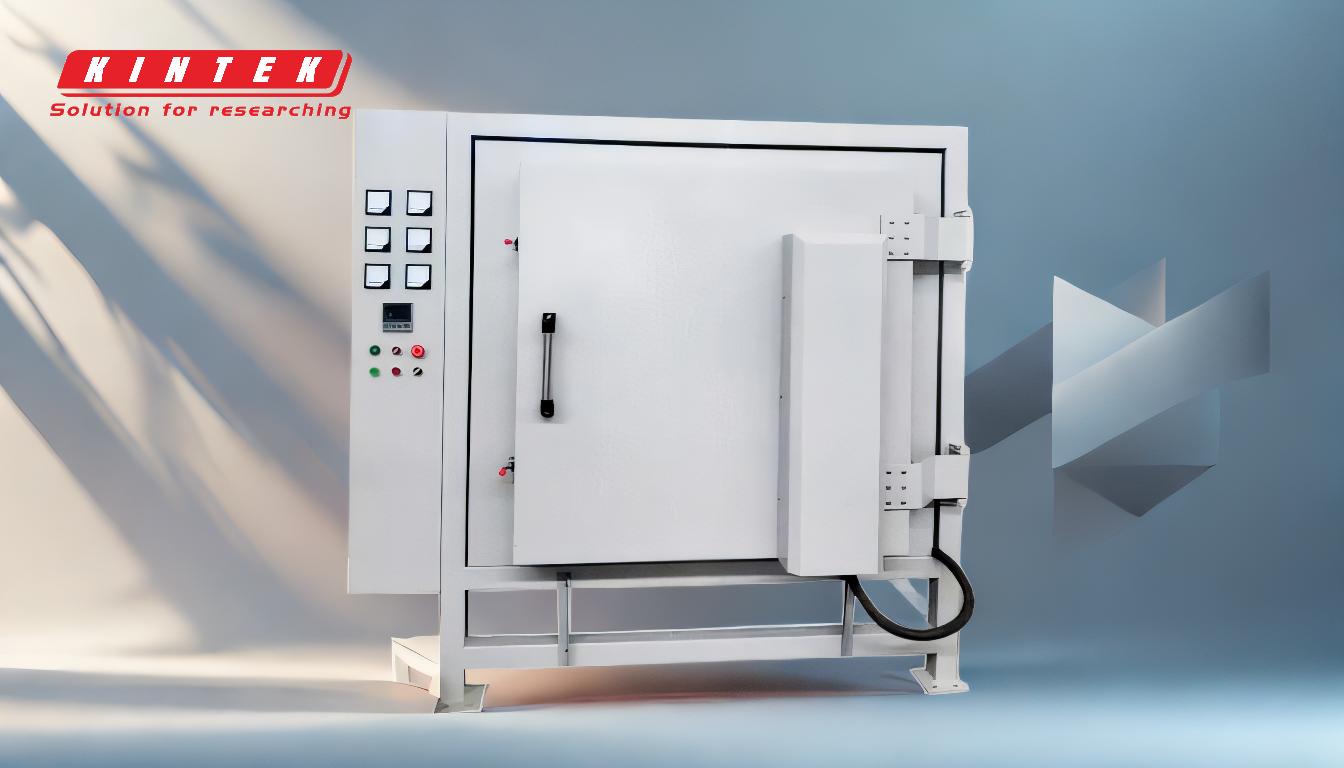
-
Low Deposition Rates
- Sputtering generally has lower deposition rates compared to other methods like thermal evaporation.
- This limitation is particularly pronounced for materials such as SiO2, where achieving desired film thicknesses can be time-consuming.
- Slow deposition rates can increase production time and costs, making sputtering less efficient for high-throughput applications.
-
High Capital and Operational Costs
- Sputtering equipment is expensive, requiring significant upfront investment.
- Maintenance costs are also high due to the need for specialized vacuum systems and cooling mechanisms to manage heat generated during the process.
- The targets used in sputtering are often costly, and material utilization can be inefficient, further increasing expenses.
-
Film Contamination Risks
- Sputtering operates under a lower vacuum range compared to evaporation, increasing the likelihood of impurities entering the substrate.
- Gaseous contaminants in the plasma can become activated, leading to contamination of the deposited film.
- Reactive sputtering requires precise control of gas composition to avoid target poisoning, adding complexity and risk.
-
Non-Uniform Film Thickness
- The deposition flux distribution in sputtering is often non-uniform, necessitating the use of moving fixtures to achieve consistent film thickness.
- This adds complexity to the process and can lead to inconsistencies in film quality if not carefully managed.
-
Heat Generation and Substrate Heating
- Most of the energy incident on the target is converted into heat, which must be effectively removed to prevent damage to the substrate or equipment.
- High substrate heating effects can limit the types of materials that can be coated, particularly those sensitive to temperature.
-
Material Compatibility Issues
- Sputtering is not suitable for insulating materials, as they can accumulate charge and disrupt the process.
- Organic solids and other sensitive materials may degrade under ionic bombardment, limiting the range of materials that can be effectively sputtered.
-
Challenges in Integration with Lift-Off Processes
- The diffuse transport of sputtered atoms makes it difficult to achieve full shadowing, complicating the integration of sputtering with lift-off processes for film structuring.
- This can lead to contamination issues and reduce the precision of the final product.
-
Difficulty in Active Control for Layer-by-Layer Growth
- Compared to methods like pulsed laser deposition, sputtering offers less control over layer-by-layer growth.
- This limitation can affect the quality and uniformity of multilayer films, particularly in applications requiring precise atomic-level control.
-
Inert Gas Impurities
- Inert sputtering gases, such as argon, can become trapped in the growing film as impurities.
- These impurities can affect the mechanical, electrical, or optical properties of the deposited film, potentially compromising its performance.
-
Process Parameter Limitations
- Sputtering is constrained by the realities of vacuum systems, which limit the range of process parameters that can be used.
- This can restrict the versatility of the process and make it less adaptable to specific application requirements.
In summary, while sputtering is a versatile and widely used technique for thin-film deposition, its disadvantages—such as low deposition rates, high costs, contamination risks, and material compatibility issues—can limit its suitability for certain applications. Careful consideration of these drawbacks is essential when selecting a deposition method for specific industrial or research needs.
Summary Table:
Disadvantage | Key Details |
---|---|
Low Deposition Rates | Slower than thermal evaporation; increases production time and costs. |
High Capital and Operational Costs | Expensive equipment, high maintenance, and inefficient material usage. |
Film Contamination Risks | Lower vacuum range increases impurity risks; reactive sputtering adds complexity. |
Non-Uniform Film Thickness | Requires moving fixtures; can lead to inconsistent film quality. |
Heat Generation | High heat requires robust cooling systems; limits temperature-sensitive materials. |
Material Compatibility Issues | Unsuitable for insulators and sensitive materials; degradation risks. |
Integration Challenges | Difficulties with lift-off processes; contamination and precision issues. |
Limited Layer-by-Layer Control | Less control compared to pulsed laser deposition; affects multilayer uniformity. |
Inert Gas Impurities | Argon impurities can compromise film properties. |
Process Parameter Limitations | Vacuum system constraints restrict versatility and adaptability. |
Need a better thin-film deposition solution? Contact us today to explore alternatives!