Zeolite adsorbents are widely used in various industries due to their unique properties, such as high surface area, porosity, and selectivity. However, they also come with several disadvantages that can limit their effectiveness in certain applications. These include issues like limited selectivity for specific molecules, susceptibility to fouling, high cost, and challenges in regeneration. Additionally, zeolites may exhibit reduced performance under extreme conditions such as high temperatures or in the presence of certain chemicals. Understanding these limitations is crucial for selecting the right adsorbent for specific applications and ensuring optimal performance.
Key Points Explained:
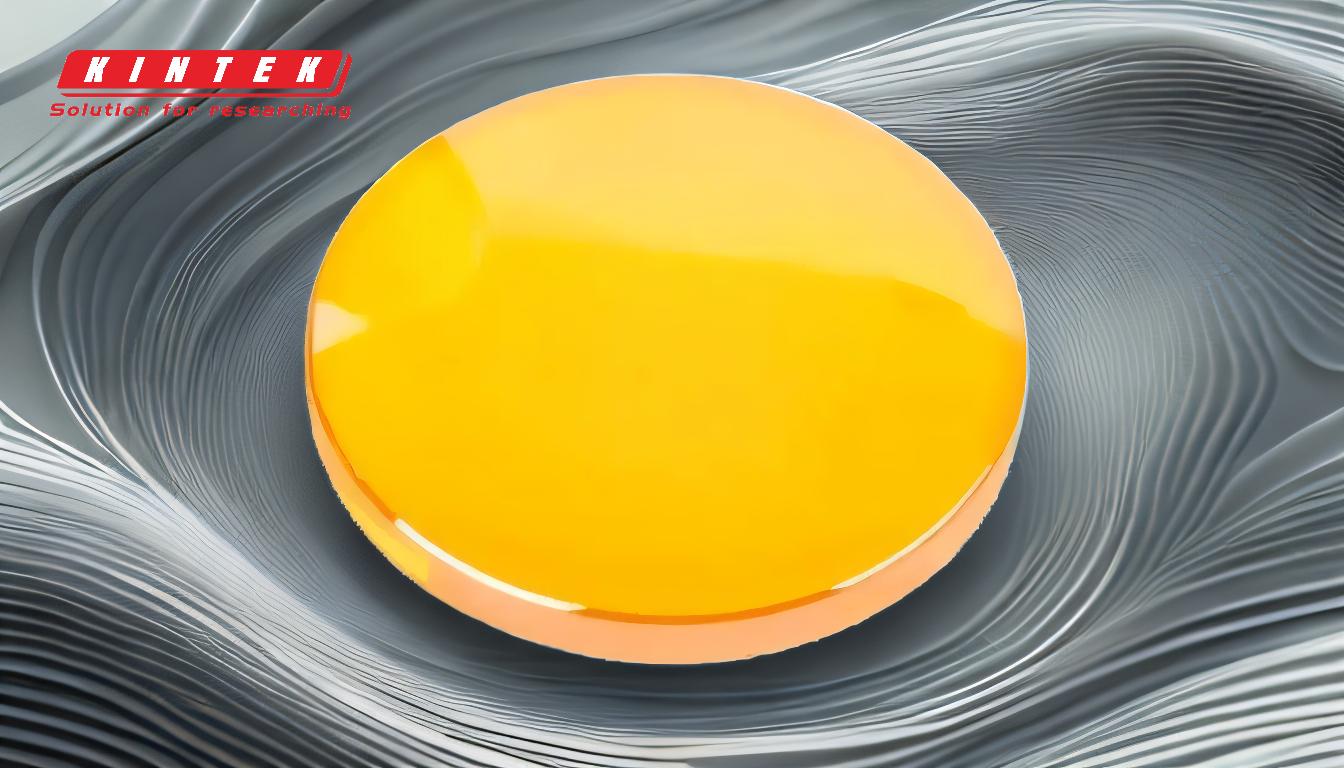
-
Limited Selectivity:
- Explanation: Zeolites are known for their molecular sieving properties, but their selectivity can be limited when dealing with molecules of similar size or shape. This can lead to the adsorption of unwanted molecules, reducing the efficiency of the process.
- Impact: In applications where high purity is required, such as in gas separation or purification processes, the limited selectivity of zeolites can be a significant drawback.
-
Susceptibility to Fouling:
- Explanation: Zeolites can become fouled by the adsorption of large molecules or impurities that block their pores. This fouling can reduce the effective surface area and adsorption capacity of the zeolite.
- Impact: Fouling can lead to frequent maintenance and replacement of the adsorbent, increasing operational costs and downtime.
-
High Cost:
- Explanation: The production and processing of zeolites can be expensive due to the need for high-purity raw materials and specialized synthesis methods. Additionally, the cost of regenerating spent zeolites can be significant.
- Impact: The high cost of zeolites can be a barrier to their use in large-scale applications or in industries with tight budget constraints.
-
Challenges in Regeneration:
- Explanation: Regenerating zeolites often requires high temperatures or the use of chemicals, which can be energy-intensive and costly. Moreover, repeated regeneration can lead to the degradation of the zeolite structure, reducing its adsorption capacity over time.
- Impact: The difficulty in regenerating zeolites can limit their long-term usability and increase the overall cost of the adsorption process.
-
Reduced Performance Under Extreme Conditions:
- Explanation: Zeolites may exhibit reduced adsorption performance under extreme conditions such as high temperatures, high pressures, or in the presence of certain chemicals. For example, some zeolites may lose their structural integrity or become less selective under these conditions.
- Impact: This limitation can restrict the use of zeolites in certain industrial processes that operate under harsh conditions.
-
Limited Hydrothermal Stability:
- Explanation: Some zeolites are not stable in the presence of water vapor at high temperatures, which can lead to structural degradation and loss of adsorption capacity.
- Impact: This can be a significant limitation in applications involving steam or high humidity environments, such as in certain gas separation processes.
-
Difficulty in Handling and Disposal:
- Explanation: Spent zeolites, especially those contaminated with hazardous substances, can be difficult to handle and dispose of safely. This can pose environmental and regulatory challenges.
- Impact: The need for proper disposal methods can add to the overall cost and complexity of using zeolites as adsorbents.
-
Limited Availability of Specific Zeolite Types:
- Explanation: Not all types of zeolites are readily available, and some may require custom synthesis, which can be time-consuming and expensive.
- Impact: The limited availability of specific zeolite types can restrict their use in specialized applications where a particular type of zeolite is required.
In summary, while zeolite adsorbents offer many advantages, their disadvantages must be carefully considered when selecting an adsorbent for a specific application. Factors such as cost, selectivity, fouling, and regeneration challenges can significantly impact the overall effectiveness and feasibility of using zeolites in various industrial processes.
Summary Table:
Disadvantage | Explanation | Impact |
---|---|---|
Limited Selectivity | Zeolites may adsorb unwanted molecules due to similar size or shape. | Reduces efficiency in high-purity applications like gas separation. |
Susceptibility to Fouling | Large molecules or impurities block pores, reducing surface area and capacity. | Increases maintenance costs and downtime. |
High Cost | Expensive production, processing, and regeneration. | Limits use in large-scale or budget-constrained industries. |
Challenges in Regeneration | Requires high temperatures or chemicals, leading to structural degradation. | Increases long-term costs and reduces usability. |
Reduced Performance Under Extreme Conditions | Performance declines at high temperatures or pressures. | Restricts use in harsh industrial environments. |
Limited Hydrothermal Stability | Structural degradation in high humidity or steam. | Limits use in steam or high-humidity applications. |
Difficulty in Handling and Disposal | Spent zeolites contaminated with hazardous substances are hard to dispose. | Adds to costs and regulatory challenges. |
Limited Availability of Specific Zeolite Types | Custom synthesis is time-consuming and expensive. | Restricts use in specialized applications requiring specific zeolite types. |
Need help selecting the right adsorbent for your application? Contact our experts today for tailored solutions!