Plasma Enhanced Chemical Vapor Deposition (PECVD) is a widely used technique for depositing thin films at relatively low temperatures, but it comes with several drawbacks. These include issues related to film quality, equipment complexity, and process control. Key concerns include unintended ion bombardment, hydrogen-related reactions, film stability, and equipment maintenance challenges. While some of these issues can be mitigated with advanced techniques like remote plasma or combined power supplies, they remain significant challenges for PECVD processes.
Key Points Explained:
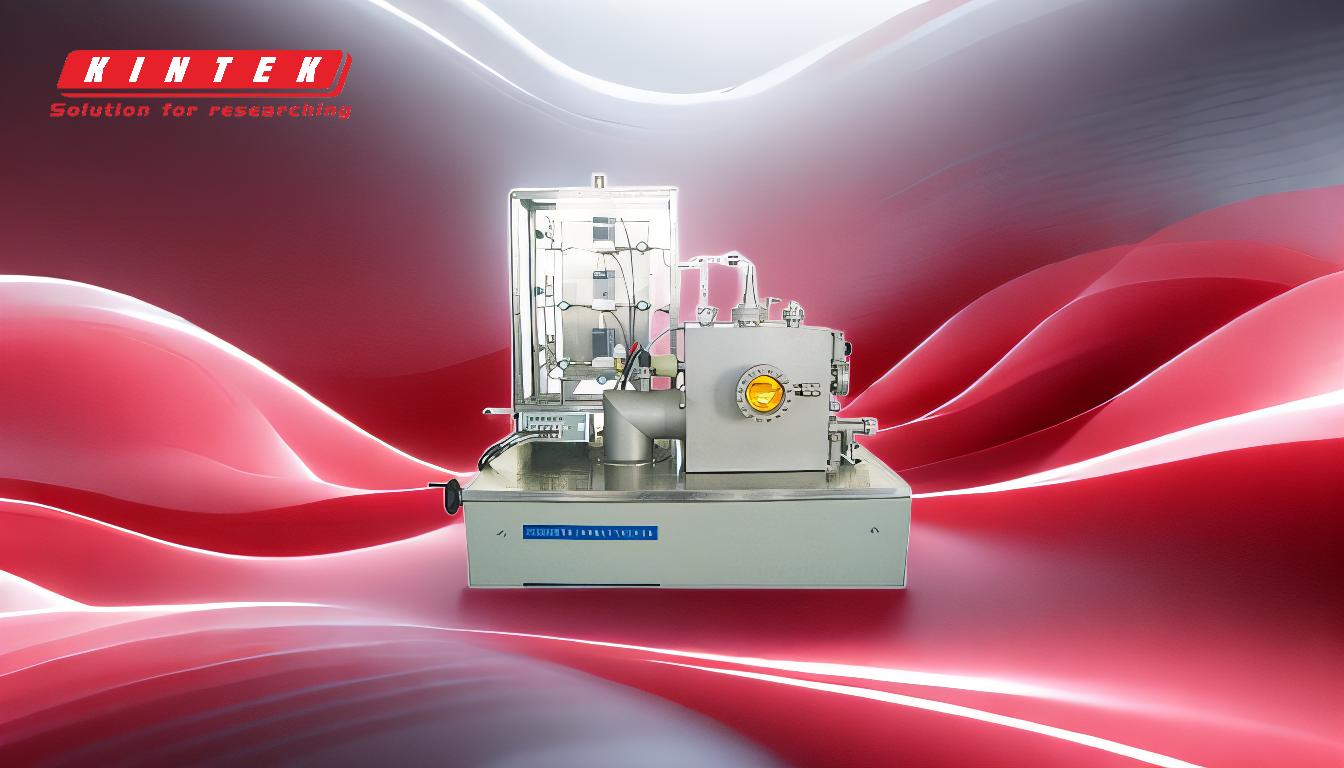
-
Unintended Ion Bombardment and Surface Damage:
- In conventional PECVD, high-energy ions in the plasma can collide with the substrate surface, leading to near-surface damage.
- This ion bombardment can increase the recombination rate in the affected region, negatively impacting the quality of the deposited film.
- Remote or downstream plasma configurations can help mitigate this issue by reducing direct ion bombardment.
-
Hydrogen-Related Reactions:
- PECVD processes often involve hydrogen-containing precursors, which can lead to unintended reactions.
- For example, hydrogen in plasma nitrides can react with silicon or nitrogen, affecting properties such as UV absorption, stability, mechanical stress, and electrical conductivity.
- These reactions can compromise the performance of the deposited films, especially in sensitive applications like semiconductor devices.
-
Film Stability Issues:
- Films deposited by PECVD may suffer from stability problems, such as film bursting or delamination.
- These issues are often linked to the presence of residual stresses or impurities in the film, which can arise from the plasma environment.
- Ensuring proper process parameters and post-deposition treatments can help improve film stability.
-
Equipment Complexity and Maintenance:
- PECVD systems are relatively complex and require high maintenance and debugging.
- Common problems include inability to glow, unstable glow, poor film quality, low sedimentation rate, and unstable reaction chamber pressure.
- Regular checks and adjustments of the RF power supply, gas flow, cleanliness of cavity plates, vacuum system, and other components are necessary to maintain optimal performance.
-
Arc Phenomenon in DC-PECVD:
- DC-PECVD systems are prone to the "arc" phenomenon, where unwanted electrical discharges occur on the workpiece.
- This can lead to localized damage and poor film quality.
- Using a combined power supply of pulse and DC power can help mitigate this issue by providing high-voltage pulses to extinguish arcs while maintaining a stable low-voltage DC supply for deposition.
-
Weaker Barrier Properties and Abrasion Resistance:
- Compared to traditional CVD, PECVD films often exhibit weaker barrier properties, which are highly dependent on film thickness, number of layers, and plasma type.
- PECVD materials are often softer and have limited abrasion resistance, making them more susceptible to damage during handling or rework.
- This can limit their suitability for applications requiring robust mechanical properties.
-
Health and Environmental Concerns:
- Some PECVD coatings may contain halogens or other hazardous materials, posing health and environmental risks.
- Proper handling, disposal, and mitigation strategies are necessary to address these concerns.
-
Process Control Challenges:
- Conventional PECVD lacks precise control over the species present in the reactor, leading to variability in film composition and properties.
- Advanced techniques, such as remote plasma or downstream configurations, can improve control but add complexity to the system.
In summary, while PECVD offers significant advantages in terms of low-temperature deposition and versatility, it also presents several challenges. These include issues related to ion bombardment, hydrogen reactions, film stability, equipment maintenance, and process control. Addressing these drawbacks often requires advanced techniques and careful process optimization, which can increase the complexity and cost of PECVD systems.
Summary Table:
Challenge | Description | Mitigation Strategies |
---|---|---|
Unintended Ion Bombardment | High-energy ions damage substrate surfaces, reducing film quality. | Use remote or downstream plasma configurations. |
Hydrogen-Related Reactions | Hydrogen reactions affect UV absorption, stability, and conductivity. | Optimize precursor selection and process parameters. |
Film Stability Issues | Films may burst or delaminate due to residual stresses or impurities. | Improve process control and apply post-deposition treatments. |
Equipment Complexity | High maintenance and debugging required for RF power, gas flow, and vacuum. | Regular system checks and component adjustments. |
Arc Phenomenon in DC-PECVD | Unwanted electrical discharges cause localized damage. | Use combined pulse and DC power supplies. |
Weaker Barrier Properties | Films have weaker barrier properties and abrasion resistance. | Optimize film thickness, layers, and plasma type. |
Health and Environmental Concerns | Hazardous materials in coatings pose risks. | Implement proper handling, disposal, and mitigation strategies. |
Process Control Challenges | Limited control over film composition and properties. | Use advanced techniques like remote plasma or downstream configurations. |
Struggling with PECVD challenges? Contact our experts today for tailored solutions and advanced techniques!