A diffusion pump is a critical component in achieving high vacuum levels, particularly in applications requiring ultra-high vacuum environments. Its operation relies on the use of diffusion pump oil and a heater to create a vapor jet that captures and removes air molecules, all without any moving parts. This design ensures durability, reliability, and the ability to produce vacuum levels ranging from 10^-2 to 10^-10 torr. Key characteristics include its no-moving-parts design, high vacuum capability, and suitability for applications like electron-beam microscopy, vacuum deposition, and vacuum furnaces. Below, we explore these characteristics in detail.
Key Points Explained:
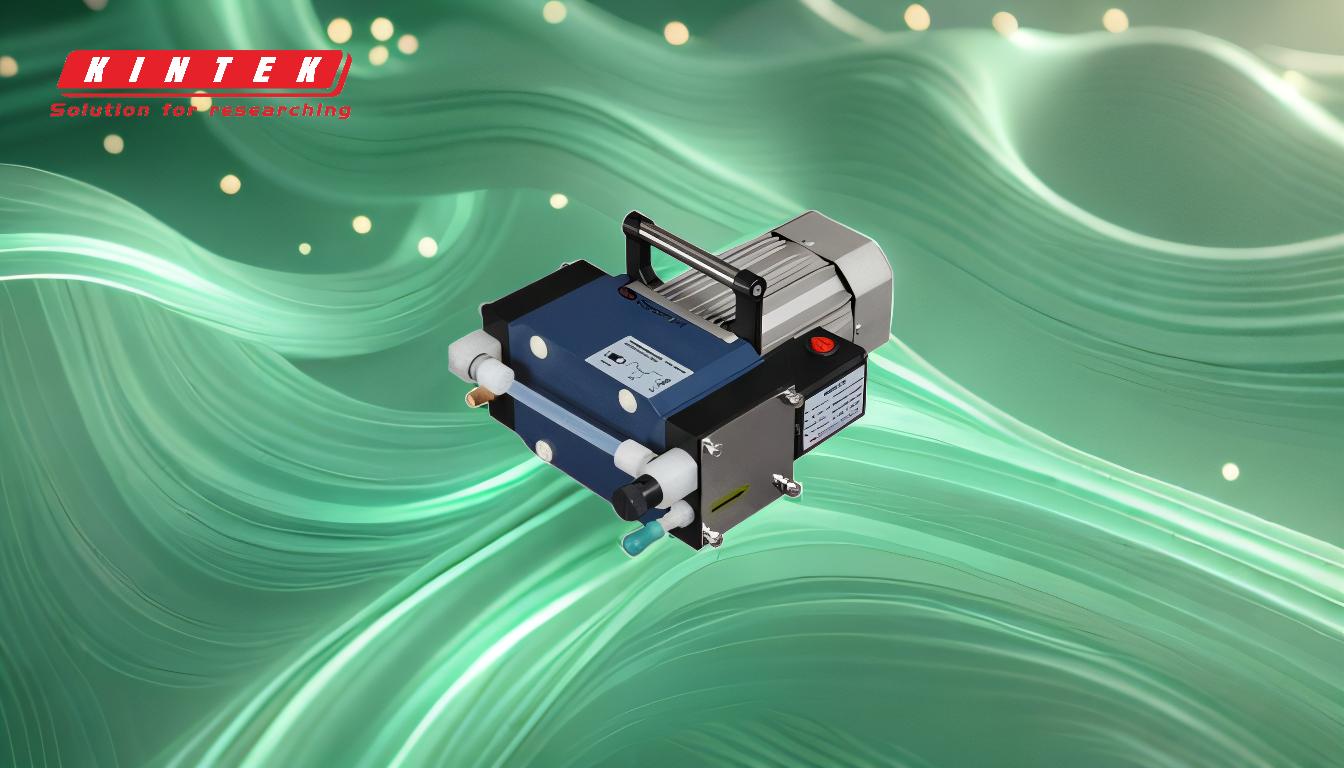
-
No Moving Parts
- Diffusion pumps operate without any mechanical components such as pistons, fins, or lobes. This design eliminates wear and tear, making them highly durable and reliable over long periods of operation.
- The absence of moving parts also reduces maintenance requirements and minimizes the risk of mechanical failure, which is particularly advantageous in high-vacuum applications where downtime can be costly.
-
High Vacuum Capability
- Diffusion pumps are capable of achieving extremely low pressures, ranging from 10^-2 to 10^-10 torr. This makes them suitable for applications requiring ultra-high vacuum environments, such as electron-beam microscopy and semiconductor manufacturing.
- The ability to produce such high vacuum levels is due to the efficient capture and removal of air molecules by the vapor jet mechanism.
-
Operation Mechanism
- The pump operates using two key elements: diffusion pump oil and a heater. The heater heats the boilerplate, causing the oil to boil and produce vapor.
- The vapor rises through a vertically tapered stack with jet openings, creating an umbrella-like vapor jet that captures air molecules.
- Cool condensing coils on the pump’s exterior help the oil vapor condense and flow back downward, while the captured air is released at the base of the pump.
-
Differential Pressure and High Vacuum Creation
- The top of the pump connects to the vacuum chamber, while the base is connected to a backing pump. The differential pressure between the top and bottom of the pump creates the high vacuum in the chamber.
- This pressure gradient ensures efficient removal of air molecules and maintains the desired vacuum level.
-
Versatility in Applications
- Diffusion pumps are widely used in industries requiring high vacuum levels, such as:
- Electron-beam microscopy: Provides the ultra-high vacuum environment needed for precise imaging.
- Vacuum deposition: Ensures clean and controlled deposition of materials in thin-film coating processes.
- Vacuum furnaces: Maintains the vacuum environment necessary for heat treatment processes.
- Diffusion pumps are widely used in industries requiring high vacuum levels, such as:
-
Variety in Sizes
- Diffusion pumps are available in various sizes, allowing them to be tailored to specific applications and vacuum chamber requirements.
- The scalability of these pumps makes them adaptable to both small-scale laboratory setups and large industrial systems.
-
Reliability and Durability
- The no-moving-parts design, combined with the use of robust materials, ensures long-term reliability and minimal maintenance.
- This makes diffusion pumps a cost-effective solution for high-vacuum applications, as they offer consistent performance over extended periods.
-
Energy Efficiency
- The operation of a diffusion pump relies primarily on the heater to boil the oil and create the vapor jet. This process is energy-efficient compared to mechanical pumps, which require continuous mechanical motion.
- The condensing coils also contribute to energy efficiency by recycling the oil vapor, reducing the need for additional energy input.
-
Environmental Considerations
- Diffusion pumps use specialized oils that are designed to operate at high temperatures and in vacuum environments. These oils are typically chosen for their low vapor pressure and chemical stability, minimizing environmental impact.
- Proper disposal and handling of the oil are essential to ensure environmental safety.
-
Integration with Other Vacuum Systems
- Diffusion pumps are often used in conjunction with backing pumps, such as rotary vane or scroll pumps, to achieve the desired vacuum levels.
- The integration of these systems requires careful design to ensure compatibility and optimal performance.
In summary, the important characteristics of a diffusion pump include its no-moving-parts design, high vacuum capability, efficient operation mechanism, and versatility across various applications. These features make it a reliable and durable choice for industries requiring ultra-high vacuum environments.
Summary Table:
Characteristic | Description |
---|---|
No Moving Parts | Durable, reliable, and low-maintenance design with no mechanical wear. |
High Vacuum Capability | Achieves pressures from 10^-2 to 10^-10 torr, ideal for ultra-high vacuum needs. |
Operation Mechanism | Uses diffusion pump oil and a heater to create a vapor jet for air molecule capture. |
Versatility | Suitable for electron-beam microscopy, vacuum deposition, and vacuum furnaces. |
Energy Efficiency | Heater-based operation and condensing coils ensure energy-efficient performance. |
Environmental Safety | Uses specialized oils with low vapor pressure and chemical stability. |
Looking for a reliable diffusion pump for your high vacuum needs? Contact us today to find the perfect solution!