Ball mills are widely used in various industries for grinding and mixing materials, but they come with several limitations that can affect their efficiency, operational costs, and suitability for certain applications. These limitations include slow processing speeds, high energy consumption, noise and vibration issues, contamination risks, and challenges in handling specific materials. Additionally, ball mills are often bulky and heavy, making them less convenient for some operations. Understanding these limitations is crucial for equipment purchasers to make informed decisions and explore alternative solutions when necessary.
Key Points Explained:
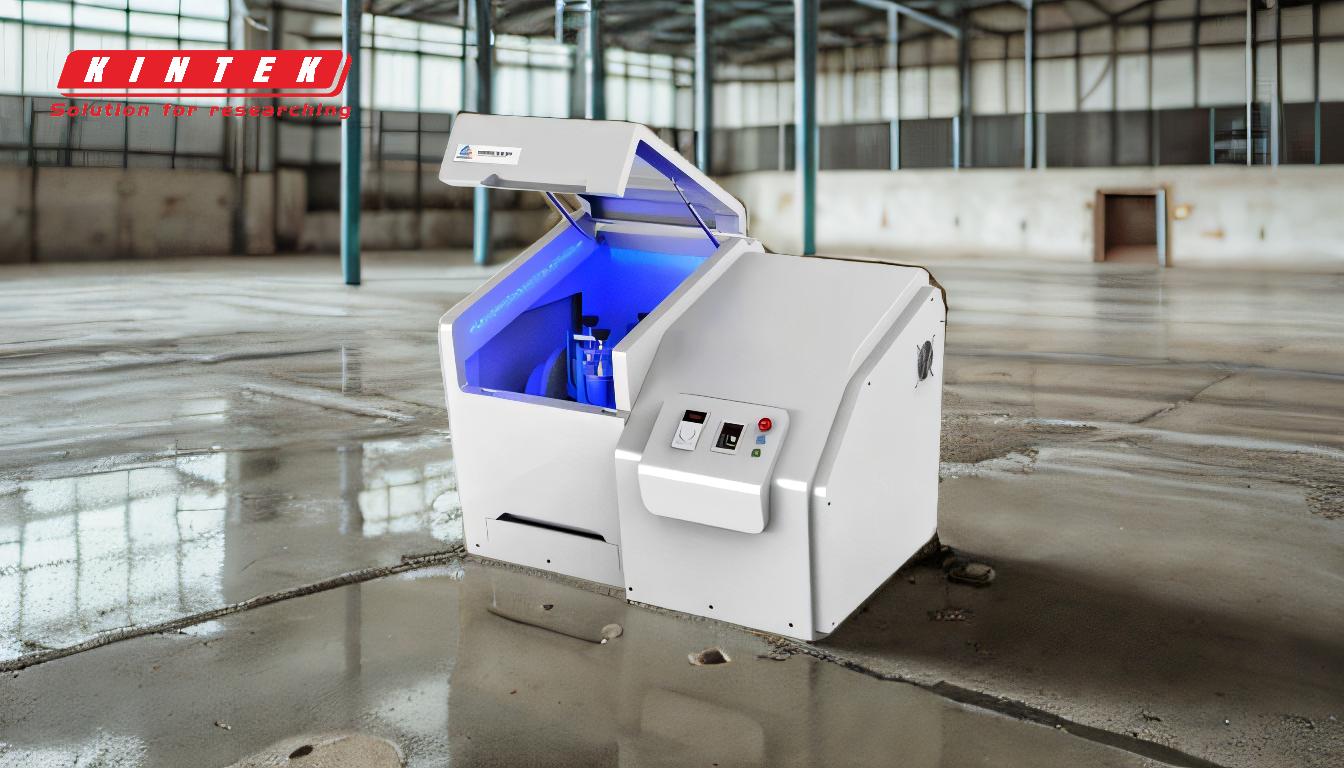
-
Slow Processing Speed:
- Ball mills are known for their relatively slow grinding process. This is due to the reliance on the cascading and tumbling motion of grinding media to break down materials. The slow speed can be a significant drawback in industries where high throughput or rapid processing is required. For example, in large-scale mining operations, the slow grinding rate can lead to bottlenecks in production.
-
High Energy Consumption:
- Ball mills consume a significant amount of energy, primarily due to the wear of grinding balls and the mill's internal lining, friction, and the heat generated during operation. This high energy consumption not only increases operational costs but also has environmental implications, especially in industries striving for sustainability. The wear of balls and wall armor further exacerbates energy inefficiency, as frequent replacements are needed.
-
Noise and Vibration:
- The operation of ball mills is often accompanied by strong vibrations and noise, which can be disruptive in industrial settings. While the use of rubber balls can mitigate some of the noise, it does not eliminate the issue entirely. Excessive noise and vibration can lead to worker discomfort, increased maintenance requirements, and potential structural damage to the mill or surrounding equipment.
-
Contamination Risks:
- The wear inside the cylinders of ball mills can lead to contamination of the processed materials. As the grinding media and mill liners wear down, particles from these components can mix with the material being ground. This is particularly problematic in industries where material purity is critical, such as pharmaceuticals or food processing. Contamination can compromise product quality and lead to additional costs for purification or disposal.
-
Limited Capacity for Specific Materials:
- Ball mills are not well-suited for grinding soft, tacky, or fibrous materials. These materials can clog the mill or adhere to the grinding media, reducing efficiency and potentially damaging the equipment. For example, in the processing of certain polymers or agricultural products, the limitations of ball mills may necessitate the use of alternative grinding technologies.
-
Bulkiness and Weight:
- Ball mills are often large and heavy, making them difficult to handle and transport. This can be a significant limitation in operations where space is limited or where equipment needs to be moved frequently. The unhandiness of ball mills can also complicate installation and maintenance processes, leading to increased downtime and labor costs.
-
Challenges in Achieving Fine Particle Sizes:
- While ball mills are effective for coarse grinding, achieving very fine particle sizes can be challenging. Traditional ball mills are often limited to producing particles around 5 microns in size. For applications requiring ultra-fine grinding, such as in the production of certain ceramics or advanced materials, alternative milling technologies like vertical mills or jet mills may be more suitable.
-
Fluidizing Issues in Vertical Mills:
- Although not a direct limitation of horizontal ball mills, it's worth noting that vertical mills, which are sometimes considered as alternatives, face their own set of challenges. Vertical mills are limited in media volume charge and can experience fluidizing issues when using finer grinding media. These limitations can affect the overall efficiency and effectiveness of the grinding process, making it important to carefully evaluate the specific requirements of each application.
In conclusion, while ball mills are versatile and widely used, their limitations must be carefully considered when selecting equipment for specific applications. Factors such as processing speed, energy consumption, noise, contamination risks, material compatibility, and the need for fine grinding should all be evaluated. For some applications, alternative grinding technologies may offer more efficient and effective solutions. Equipment purchasers should weigh these limitations against the specific needs of their operations to make the most informed decision.
Summary Table:
Limitation | Impact |
---|---|
Slow Processing Speed | Bottlenecks in high-throughput industries like mining. |
High Energy Consumption | Increased operational costs and environmental concerns. |
Noise and Vibration | Worker discomfort, maintenance needs, and potential structural damage. |
Contamination Risks | Compromised material purity, especially in pharmaceuticals and food. |
Limited Capacity for Soft Materials | Clogging and inefficiency with soft, tacky, or fibrous materials. |
Bulkiness and Weight | Difficult to handle, transport, and install; increases downtime. |
Challenges in Fine Grinding | Limited to particles around 5 microns; alternatives needed for finer sizes. |
Fluidizing Issues in Vertical Mills | Media volume and fluidizing challenges in vertical mill alternatives. |
Need help choosing the right grinding equipment? Contact our experts today for tailored solutions!