Injection molding is a manufacturing process used to produce parts by injecting molten material into a mold. The process is highly efficient and can be broken down into four main stages: clamping, injection, cooling, and ejection. Each stage plays a critical role in ensuring the final product meets the desired specifications. The entire cycle typically lasts between 2 seconds to 2 minutes, depending on the complexity of the part and the material used. Below, we will explore each stage in detail to provide a comprehensive understanding of the injection molding process.
Key Points Explained:
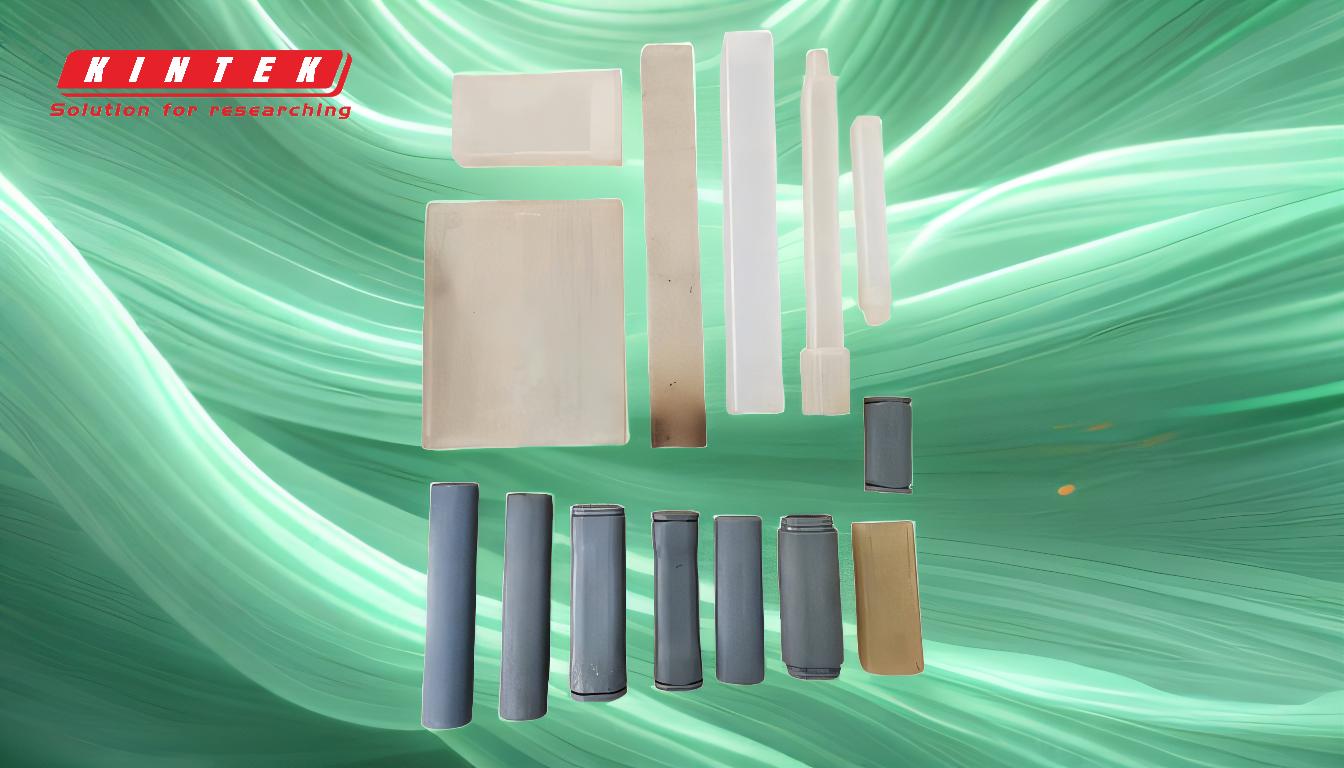
-
Clamping Stage
- Purpose: The clamping stage involves securing the two halves of the mold together to prepare for the injection of molten material.
-
Process:
- The mold consists of two halves: the stationary half (attached to the injection molding machine) and the moving half (which opens and closes).
- A clamping unit applies pressure to hold the mold halves tightly together during the injection process.
- The clamping force must be sufficient to withstand the pressure of the injected material, preventing any leakage or deformation of the mold.
- Importance: Proper clamping ensures the mold remains closed and stable, which is critical for producing high-quality parts with precise dimensions.
-
Injection Stage
- Purpose: In this stage, molten material is injected into the mold cavity to form the desired part.
-
Process:
- The material (usually plastic pellets) is fed into a heated barrel, where it is melted and homogenized.
- A reciprocating screw or plunger pushes the molten material into the mold cavity under high pressure.
- The material fills the cavity, taking the shape of the mold.
-
Factors to Consider:
- Injection pressure, speed, and temperature must be carefully controlled to ensure the material fills the mold completely and uniformly.
- Overfilling or underfilling the mold can lead to defects such as warping, sink marks, or incomplete parts.
- Importance: The injection stage determines the initial shape and integrity of the part, making it a critical step in the process.
-
Cooling Stage
- Purpose: After the mold is filled, the material must cool and solidify to maintain its shape.
-
Process:
- Cooling begins as soon as the material is injected into the mold.
- The mold is designed with cooling channels through which a coolant (usually water) circulates to dissipate heat.
- The cooling time depends on the material properties, part thickness, and mold design.
-
Factors to Consider:
- Insufficient cooling can lead to deformation or internal stresses in the part.
- Excessive cooling can increase cycle time, reducing production efficiency.
- Importance: Proper cooling ensures the part solidifies correctly, maintaining dimensional accuracy and structural integrity.
-
Ejection Stage
- Purpose: Once the part has cooled and solidified, it is ejected from the mold.
-
Process:
- The mold opens, and ejector pins or plates push the part out of the mold cavity.
- The part is then removed from the machine, either manually or automatically.
-
Factors to Consider:
- Ejection must be done carefully to avoid damaging the part or the mold.
- Proper mold design, including the placement of ejector pins, is crucial to ensure smooth ejection.
- Importance: The ejection stage completes the cycle, allowing the mold to be prepared for the next injection.
Additional Considerations for Equipment and Consumables Purchasers:
- Material Selection: The type of material used (e.g., thermoplastics, thermosetting polymers) affects the molding process and final product properties.
- Mold Design: A well-designed mold with proper cooling channels and ejection mechanisms is essential for efficient production.
- Machine Specifications: The injection molding machine must have adequate clamping force, injection pressure, and cooling capacity to handle the specific requirements of the part.
- Cycle Time Optimization: Reducing cycle time while maintaining quality is key to improving production efficiency and reducing costs.
By understanding these stages and their importance, equipment and consumables purchasers can make informed decisions to optimize the injection molding process for their specific needs.
Summary Table:
Stage | Purpose | Key Process | Importance |
---|---|---|---|
Clamping | Secure mold halves for injection | Apply clamping force to hold mold tightly; prevent leakage or deformation | Ensures mold stability and precise part dimensions |
Injection | Inject molten material into the mold cavity | Melt material, push into mold under high pressure; control pressure, speed, and temperature | Determines part shape and integrity; critical for defect-free results |
Cooling | Solidify material to maintain shape | Circulate coolant through mold channels; control cooling time based on material and part thickness | Ensures dimensional accuracy and structural integrity; prevents deformation |
Ejection | Remove solidified part from the mold | Open mold and use ejector pins/plates to push out the part; ensure smooth ejection | Completes the cycle; prepares mold for the next injection |
Ready to optimize your injection molding process? Contact our experts today for tailored solutions!