A rubber mixer, specifically an internal mixer, is a critical piece of equipment in the production of rubber compounds, such as those used in tires and general rubber products. Its primary function is to uniformly disperse fillers, additives, and other raw materials into the rubber polymer through high shear forces generated by rotating rotors. This process ensures thorough mixing, reduces viscosity, and enhances the material's properties for further processing. The operation involves precise material measurement, controlled temperature management, and sequential addition of ingredients to achieve consistent and high-quality rubber compounds.
Key Points Explained:
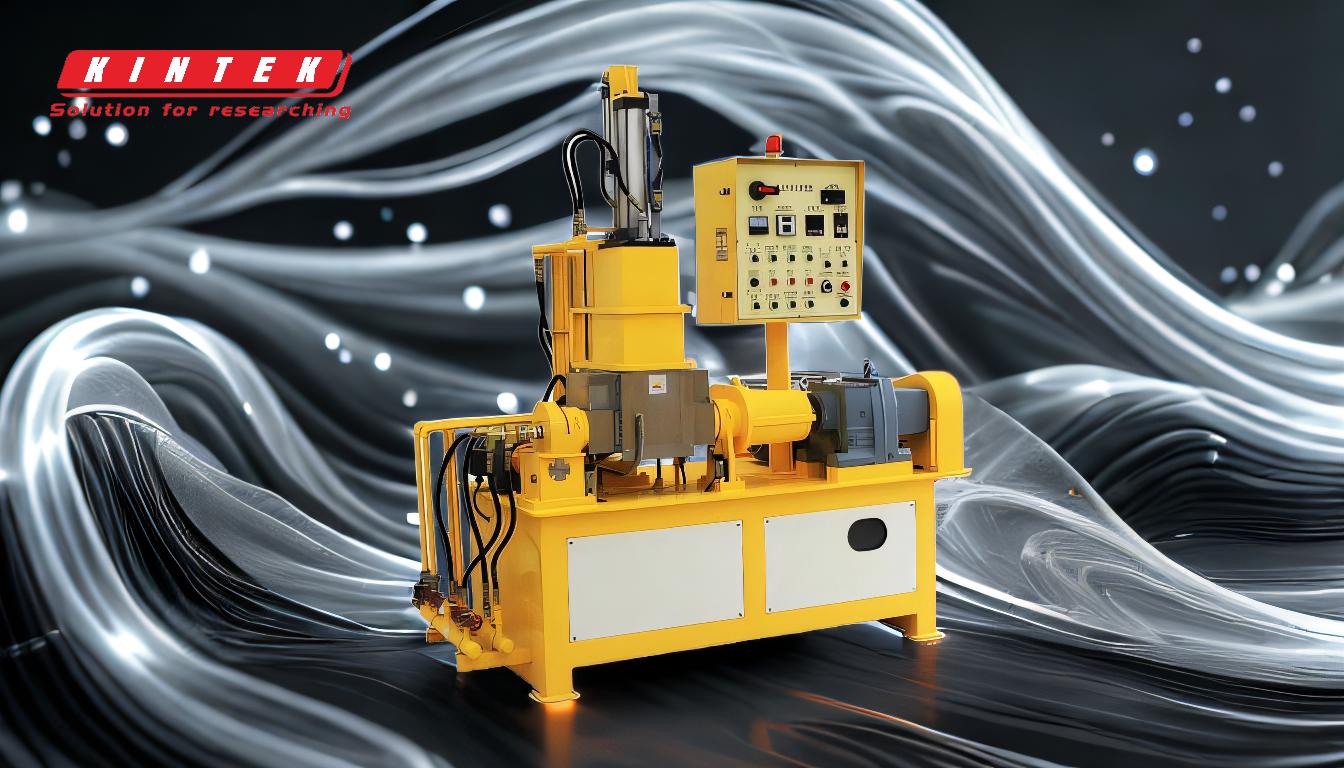
-
Purpose of a Rubber Mixer:
- A rubber mixer is designed to blend rubber polymers with various compounding agents, such as fillers, carbon black, and softeners, to create a homogeneous mixture.
- This process is essential for ensuring the final product has the desired physical and chemical properties, such as elasticity, strength, and durability.
-
Mechanism of Mixing:
- The internal mixer uses two rotors that rotate relative to each other within a sealed chamber.
- The rotors generate high shear forces, which break down the rubber and disperse the compounding agents uniformly.
- The mechanical action of the rotors also generates heat, which reduces the rubber's viscosity and improves its ability to wet and adhere to the compounding agents.
-
Key Components and Their Functions:
- Mixing Chamber: A sealed compartment where raw materials are added and mixed.
- Rotors: Blades or ridges that rotate to create shear forces, ensuring thorough mixing.
- Temperature Control System: Monitors and regulates the heat generated during mixing to prevent overheating or under-processing.
- Weighing System: Ensures accurate measurement of raw materials for consistent compound quality.
-
Operational Steps:
- Material Calculation: Determine the amount of materials to be mixed based on the chamber capacity and filling factor (typically 0.6-0.7).
- Preheating: Warm up the mixer to the desired temperature to prepare for mixing.
- Sequential Addition: Add raw rubber first, followed by small materials, fillers (e.g., carbon black), and liquid softeners.
- Temperature Monitoring: Continuously monitor and adjust the temperature to ensure optimal mixing conditions.
- Post-Mixing Processing: Transfer the mixed rubber to an open mill for further processing, such as adding sulfur and cooling.
-
Importance of Temperature Control:
- Heat generated during mixing reduces the rubber's viscosity, making it easier to disperse fillers and additives.
- Excessive heat can degrade the rubber, while insufficient heat may result in poor dispersion and mixing.
-
Applications of Mixed Rubber Compounds:
- Mixed rubber compounds are used in the production of tires, industrial rubber products, seals, gaskets, and other rubber-based items.
- The uniformity and quality of the mixed compound directly impact the performance and durability of the final product.
-
Advantages of Internal Mixers:
- Efficiency: High shear forces ensure rapid and thorough mixing.
- Consistency: Precise control over material addition and temperature ensures uniform compound quality.
- Versatility: Suitable for a wide range of rubber formulations and applications.
-
Challenges and Considerations:
- Energy Consumption: The mixing process requires significant energy, particularly for large-scale operations.
- Maintenance: Regular maintenance of rotors, seals, and temperature control systems is necessary to ensure optimal performance.
- Material Handling: Proper handling and storage of raw materials are critical to prevent contamination and ensure accurate weighing.
By understanding the role and operation of a rubber mixer, manufacturers can optimize their processes to produce high-quality rubber compounds efficiently and consistently.
Summary Table:
Aspect | Details |
---|---|
Purpose | Blends rubber polymers with fillers, carbon black, and softeners. |
Mechanism | Uses rotating rotors to generate high shear forces for uniform mixing. |
Key Components | Mixing chamber, rotors, temperature control system, weighing system. |
Operational Steps | Material calculation, preheating, sequential addition, temperature control. |
Applications | Tires, industrial rubber products, seals, gaskets, and more. |
Advantages | Efficiency, consistency, versatility. |
Challenges | Energy consumption, maintenance, material handling. |
Optimize your rubber mixing process with expert guidance—contact us today!