A three-part mold, also known as a three-plate mold, is a specialized tool used in injection molding to produce plastic parts. Unlike a standard two-plate mold, which has a single parting line, a three-plate mold features an additional plate, creating two parting lines. This design allows for the automatic separation of the molded part from the cold runner system during ejection. The three-plate mold is particularly useful for complex parts that require multiple gates or precise control over the flow of material. It consists of three main plates: the cavity plate, the stripper plate, and the core plate, each serving a specific function in the molding process.
Key Points Explained:
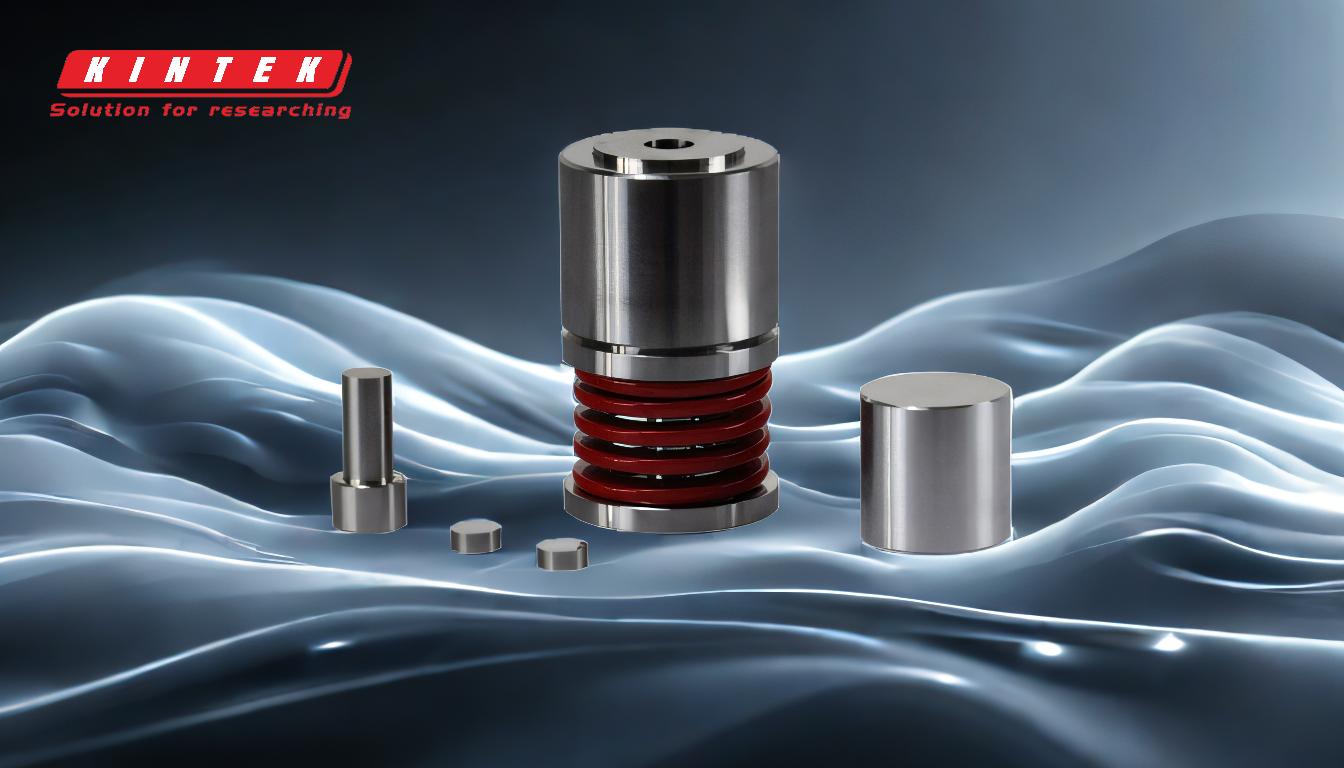
-
Definition and Structure of a Three-Part Mold
- A three-part mold is an injection molding tool with three main plates: the cavity plate, the stripper plate, and the core plate.
- The additional plate (stripper plate) creates two parting lines, unlike the single parting line in a two-plate mold.
-
Purpose of the Stripper Plate
- The stripper plate is positioned between the cavity and core plates.
- Its primary function is to separate the cold runner system from the molded part during ejection.
- This automatic separation reduces manual labor and increases efficiency in the production process.
-
Advantages of a Three-Part Mold
- Complex Part Design: Suitable for parts that require multiple gates or intricate geometries.
- Automated Runner Separation: Eliminates the need for manual removal of the runner system, reducing cycle time and labor costs.
- Precision: Allows for better control over the flow of material, resulting in higher-quality parts.
-
Comparison with Two-Part Molds
- Two-Part Molds: Consist of only two plates (cavity and core) with a single parting line.
- Three-Part Molds: Include an additional stripper plate, creating two parting lines and enabling more complex designs and automated processes.
-
Applications of Three-Part Molds
- Ideal for producing parts with multiple cavities or gates.
- Commonly used in industries requiring high precision and complex geometries, such as automotive, electronics, and medical devices.
-
Considerations for Using Three-Part Molds
- Cost: Three-part molds are generally more expensive to design and manufacture due to their complexity.
- Maintenance: Requires more maintenance and careful handling to ensure proper alignment and function of the stripper plate.
- Cycle Time: While they can reduce manual labor, the additional plate may slightly increase the cycle time compared to two-part molds.
In summary, a three-part mold is a sophisticated tool in injection molding that offers significant advantages for producing complex parts with precision and efficiency. Its unique design, featuring an additional stripper plate, allows for automated runner separation and better control over the molding process, making it a valuable choice for high-precision manufacturing applications.
Summary Table:
Aspect | Details |
---|---|
Structure | Three plates: cavity, stripper, and core plates. Two parting lines. |
Purpose of Stripper Plate | Automatically separates the runner system from the molded part during ejection. |
Advantages | - Complex part design support. - Automated runner separation. - Precision material flow control. |
Applications | Automotive, electronics, medical devices, and other high-precision industries. |
Considerations | Higher cost, increased maintenance, and slightly longer cycle times. |
Ready to enhance your injection molding process with a three-part mold? Contact us today for expert guidance!