A three-plate mold is a specialized injection molding tool designed to produce plastic parts with precision and efficiency. It consists of three main plates: the feed plate, the cavity plate, and the core plate. The design allows for the use of pinpoint gates, which are located at the center of the mold, enabling the molten plastic to flow into multiple cavities simultaneously. This structure is particularly useful for complex parts that require multiple gates or when the gate location must be carefully controlled to minimize visible marks on the finished product. The three-plate mold separates the runner system from the part, allowing for automatic degating and reducing material waste.
Key Points Explained:
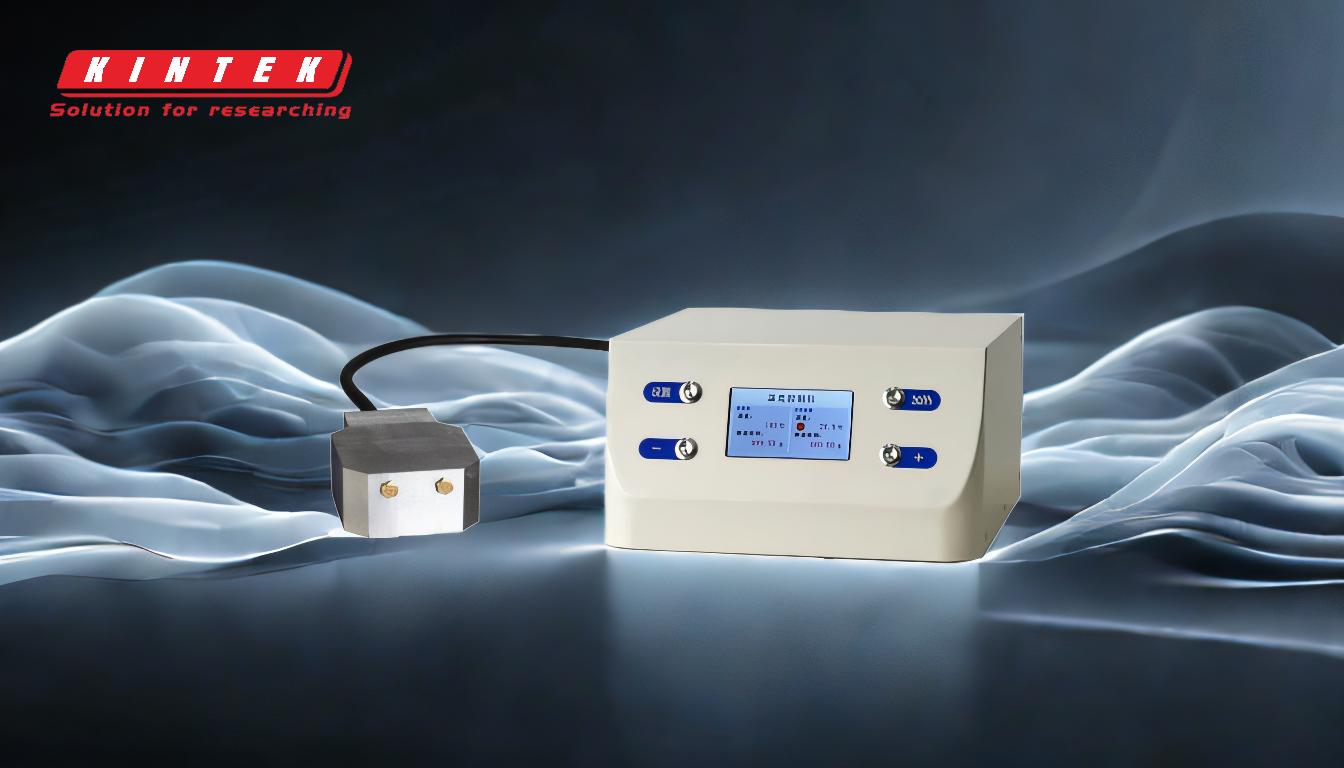
-
Three-Plate Mold Structure:
- The three-plate mold is composed of three distinct plates: the feed plate, the cavity plate, and the core plate.
- The feed plate is the first component, responsible for distributing the molten plastic from the injection molding machine to the mold cavities.
- The cavity plate (intermediate plate) contains the cavities where the plastic part is formed.
- The core plate assembly is the final component, which houses the cores that shape the internal features of the part.
-
Pinpoint Gate:
- The three-plate mold typically uses a pinpoint gate, located at the center of the mold.
- This gate design allows for precise control of the flow of molten plastic into the cavities, ensuring uniform filling and reducing the risk of defects.
- Pinpoint gates are particularly beneficial for parts that require a clean appearance, as they leave minimal visible marks on the finished product.
-
Separation of Runner System:
- One of the key advantages of a three-plate mold is the separation of the runner system from the part.
- The runner system, which channels the molten plastic from the injection molding machine to the cavities, is located between the feed plate and the cavity plate.
- After the part is ejected, the runner system is automatically separated from the part, allowing for easy removal and reducing material waste.
-
Automatic Degating:
- The three-plate mold design facilitates automatic degating, where the gate (the point where the plastic enters the cavity) is automatically removed from the part during ejection.
- This process eliminates the need for manual degating, reducing labor costs and improving production efficiency.
-
Applications:
- Three-plate molds are ideal for producing complex parts that require multiple gates or precise gate placement.
- They are commonly used in the production of small, intricate components, such as electronic connectors, medical devices, and automotive parts, where high precision and minimal gate marks are critical.
-
Advantages:
- Precision: The use of pinpoint gates and the separation of the runner system ensure high precision in part formation.
- Efficiency: Automatic degating and reduced material waste contribute to overall production efficiency.
- Versatility: The three-plate mold can accommodate complex part designs and multiple cavities, making it a versatile tool in injection molding.
-
Disadvantages:
- Complexity: The three-plate mold is more complex to design and manufacture compared to a two-plate mold, which can increase initial costs.
- Maintenance: The additional components and complexity may require more maintenance and care during operation.
In summary, the three-plate mold structure is a sophisticated injection molding tool that offers precision, efficiency, and versatility for producing complex plastic parts. Its design allows for the use of pinpoint gates, automatic degating, and separation of the runner system, making it an excellent choice for applications where high precision and minimal gate marks are essential. However, the complexity of the design may result in higher initial costs and maintenance requirements.
Summary Table:
Aspect | Details |
---|---|
Structure | Composed of feed plate, cavity plate, and core plate. |
Pinpoint Gate | Enables precise plastic flow, minimal visible marks on finished parts. |
Runner System | Separates runner system from the part, reducing material waste. |
Automatic Degating | Eliminates manual degating, improving efficiency. |
Applications | Ideal for complex parts like electronic connectors and medical devices. |
Advantages | Precision, efficiency, and versatility in part production. |
Disadvantages | Higher initial costs and maintenance due to design complexity. |
Ready to enhance your injection molding process? Contact us today to learn more about three-plate molds!