Cathode sputtering is a physical vapor deposition (PVD) technique used to deposit thin films of materials onto a substrate. It involves bombarding a solid target (cathode) with high-energy ions, typically argon ions, in a vacuum chamber. The target is negatively charged, while the substrate acts as the positive electrode. When the argon ions strike the target, they dislodge atoms from its surface, which then deposit onto the substrate to form a thin film. This process is widely used in industries such as semiconductors, optics, and architectural glass for creating coatings with specific properties like durability, conductivity, or optical performance.
Key Points Explained:
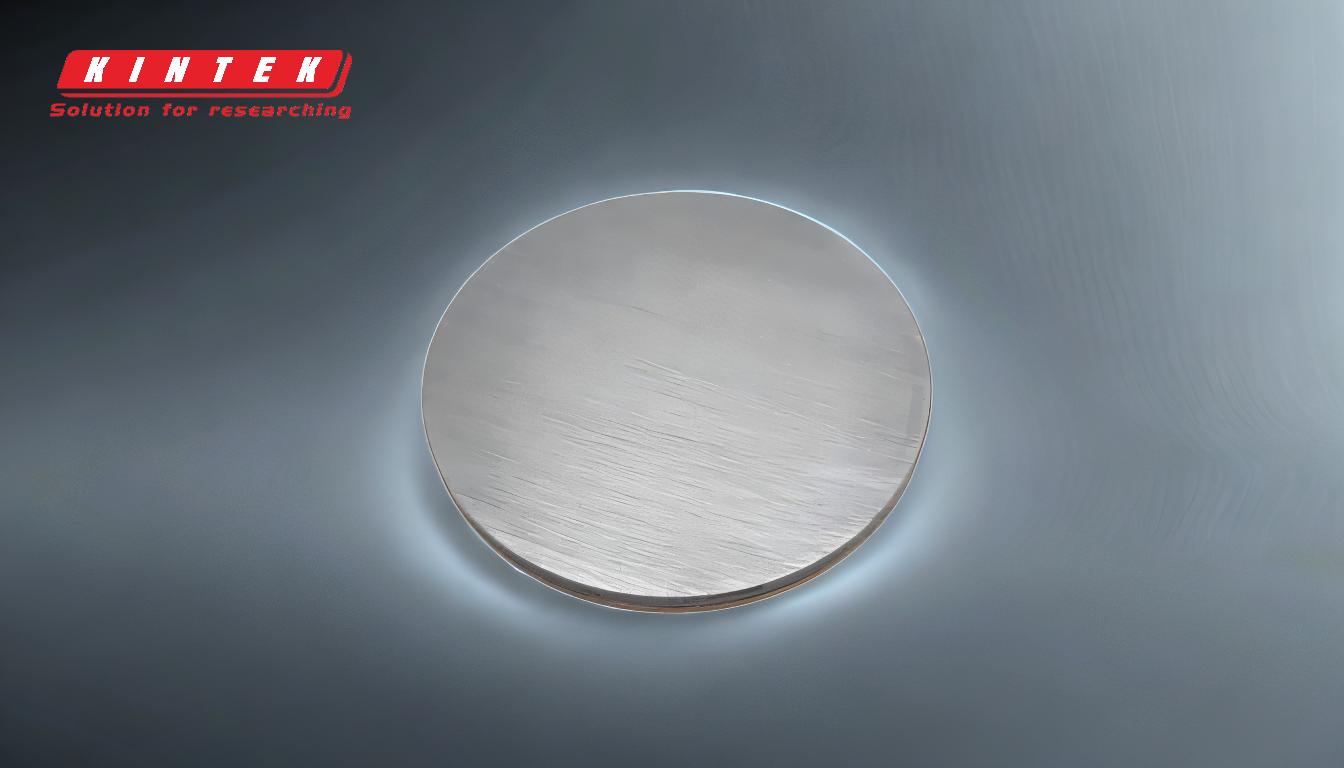
-
Definition and Process of Cathode Sputtering:
- Cathode sputtering is a PVD technique where a solid target material is bombarded by high-energy ions in a vacuum environment.
- The target is negatively charged (cathode), and the substrate is positively charged (anode).
- An inert gas, usually argon, is introduced into the chamber and ionized to create a plasma.
- The argon ions accelerate toward the target, dislodging atoms from its surface, which then deposit onto the substrate as a thin film.
-
Key Components and Setup:
- Target Material: The solid material to be sputtered, typically metallic or conductive.
- Substrate: The surface onto which the sputtered material is deposited.
- Inert Gas: Argon is commonly used due to its inert nature and ability to form a stable plasma.
- Vacuum Chamber: Ensures a controlled environment free from contaminants.
- DC Power Supply: Provides the negative potential to the target, generating the electric field necessary for ion acceleration.
-
Applications of Cathode Sputtering:
- Semiconductor Industry: Used for depositing thin films in integrated circuits and computer hard disks.
- Optical Industry: Produces polarization filters and anti-reflective coatings.
- Architectural Glass: Coats large-area surfaces with functional films, such as low-emissivity coatings.
- Aerospace and Defense: Applies specialized coatings like gadolinium films for neutron radiography.
- Medical Devices: Creates dielectric stacks to electrically isolate surgical tools.
-
Advantages of Cathode Sputtering:
- Versatility: Can deposit a wide range of materials, including metals, alloys, and some non-conductive materials.
- Precision: Allows for the deposition of thin films with thicknesses ranging from nanometers to micrometers.
- Uniformity: Produces highly uniform coatings, even on complex geometries.
- Scalability: Suitable for both small-scale research and large-scale industrial applications.
-
Limitations of Cathode Sputtering:
- Material Constraints: Less effective for non-conductive materials, as they can become positively charged, repelling ions.
- Cost: Requires specialized equipment and a high-vacuum environment, which can be expensive.
- Deposition Rate: Typically slower compared to other deposition methods like evaporation.
-
Comparison with Other Sputtering Techniques:
- DC Sputtering: The simplest form of cathode sputtering, ideal for conductive materials.
- RF Sputtering: Uses radio frequency to sputter non-conductive materials by preventing charge buildup.
- Magnetron Sputtering: Enhances efficiency by using magnetic fields to confine electrons, increasing ionization and deposition rates.
-
Future Trends and Innovations:
- Advanced Materials: Development of new target materials for specialized applications, such as high-temperature superconductors.
- Hybrid Techniques: Combining sputtering with other deposition methods to achieve unique material properties.
- Sustainability: Reducing energy consumption and environmental impact through optimized processes and recycling of inert gases.
By understanding the principles, components, and applications of cathode sputtering, purchasers and engineers can make informed decisions about its use in various industries, ensuring optimal performance and cost-effectiveness.
Summary Table:
Aspect | Details |
---|---|
Process | Bombardment of a solid target with high-energy ions in a vacuum chamber. |
Key Components | Target material, substrate, inert gas (argon), vacuum chamber, DC power supply. |
Applications | Semiconductors, optics, architectural glass, aerospace, medical devices. |
Advantages | Versatility, precision, uniformity, scalability. |
Limitations | Material constraints, high cost, slower deposition rate. |
Comparison | DC sputtering, RF sputtering, magnetron sputtering. |
Future Trends | Advanced materials, hybrid techniques, sustainability. |
Discover how cathode sputtering can enhance your projects—contact our experts today!