A mold cavity is typically made from corrosion-resistant metals, such as hardened steel or tool steel, to ensure durability and resistance to wear during the molding process. These materials are chosen for their ability to withstand high pressures, temperatures, and corrosive environments, which are common in molding operations. The use of such materials helps maintain the integrity of the mold cavity over time, ensuring consistent product quality. Additionally, proper maintenance, such as cleaning with mild alkaline solutions, is essential to prolong the lifespan of the mold cavity and prevent contamination or degradation.
Key Points Explained:
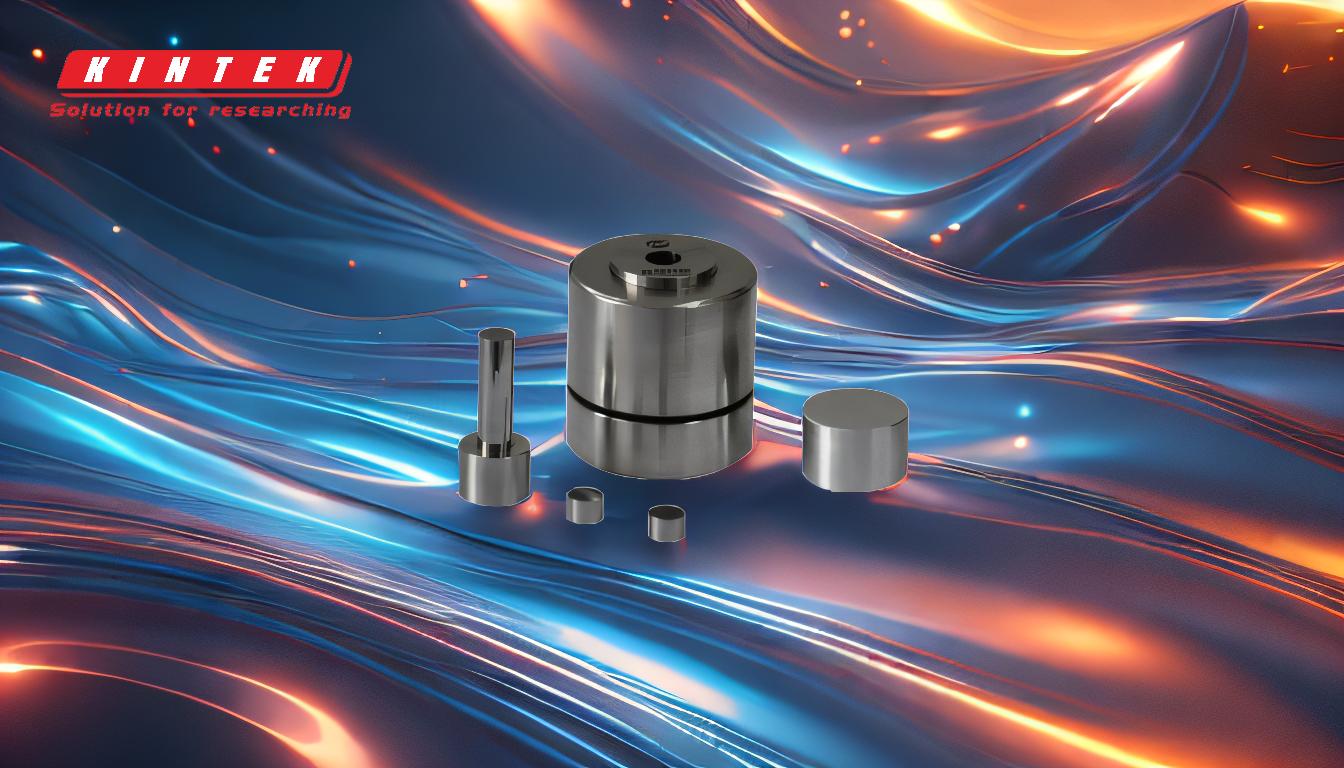
-
Material Selection for Mold Cavities
- Mold cavities are constructed from corrosion-resistant metals to ensure longevity and performance.
- Common materials include hardened steel and tool steel, which are selected for their strength, durability, and resistance to wear and tear.
- These materials are capable of withstanding the high pressures and temperatures encountered during molding processes, such as injection molding or die casting.
-
Importance of Corrosion Resistance
- Corrosion-resistant metals are essential to prevent degradation caused by exposure to moisture, chemicals, or other corrosive elements.
- This resistance ensures that the mold cavity maintains its structural integrity and dimensional accuracy over repeated use.
- Without corrosion resistance, the mold cavity could deteriorate, leading to defects in the molded products and increased maintenance costs.
-
Protective Measures for Mold Cavities
- When mold cavities are made of materials like hardened steel or tool steel without protective plating, additional care is required.
- Regular cleaning with a mild alkaline solution is recommended to remove contaminants and prevent corrosion.
- Proper maintenance extends the lifespan of the mold cavity and ensures consistent product quality.
-
Role of Hardened Steel and Tool Steel
- Hardened steel is known for its high hardness and wear resistance, making it ideal for high-stress molding applications.
- Tool steel offers excellent toughness and heat resistance, which are critical for maintaining performance under extreme conditions.
- Both materials are widely used in the manufacturing of mold cavities due to their ability to retain precision and durability over time.
-
Maintenance and Cleaning Practices
- Cleaning the mold cavity with a mild alkaline solution helps remove residues, oils, and other contaminants that could affect the molding process.
- Regular maintenance prevents the buildup of debris, which can lead to surface imperfections or mold failure.
- Proper cleaning also reduces the risk of contamination in the final product, ensuring high-quality output.
By understanding the materials and maintenance practices for mold cavities, equipment and consumable purchasers can make informed decisions to optimize their molding processes and ensure long-term reliability.
Summary Table:
Key Aspect | Details |
---|---|
Material Selection | Hardened steel, tool steel |
Key Properties | Corrosion resistance, high hardness, wear resistance, heat resistance |
Applications | Injection molding, die casting |
Maintenance Practices | Cleaning with mild alkaline solutions to prevent contamination and corrosion |
Benefits | Longevity, consistent product quality, reduced maintenance costs |
Optimize your molding process with durable mold cavities—contact us today for expert advice!