A two-plate mold is one of the most basic and widely used designs in injection molding. It consists of two main parts: the fixed side (Side A) and the movable side (Side B). During the injection molding process, Side A remains stationary, while Side B moves to open and close the mold. This design is simple, cost-effective, and suitable for producing a wide range of plastic parts. Its straightforward structure makes it easier to manufacture and maintain, making it a popular choice for many injection molding applications.
Key Points Explained:
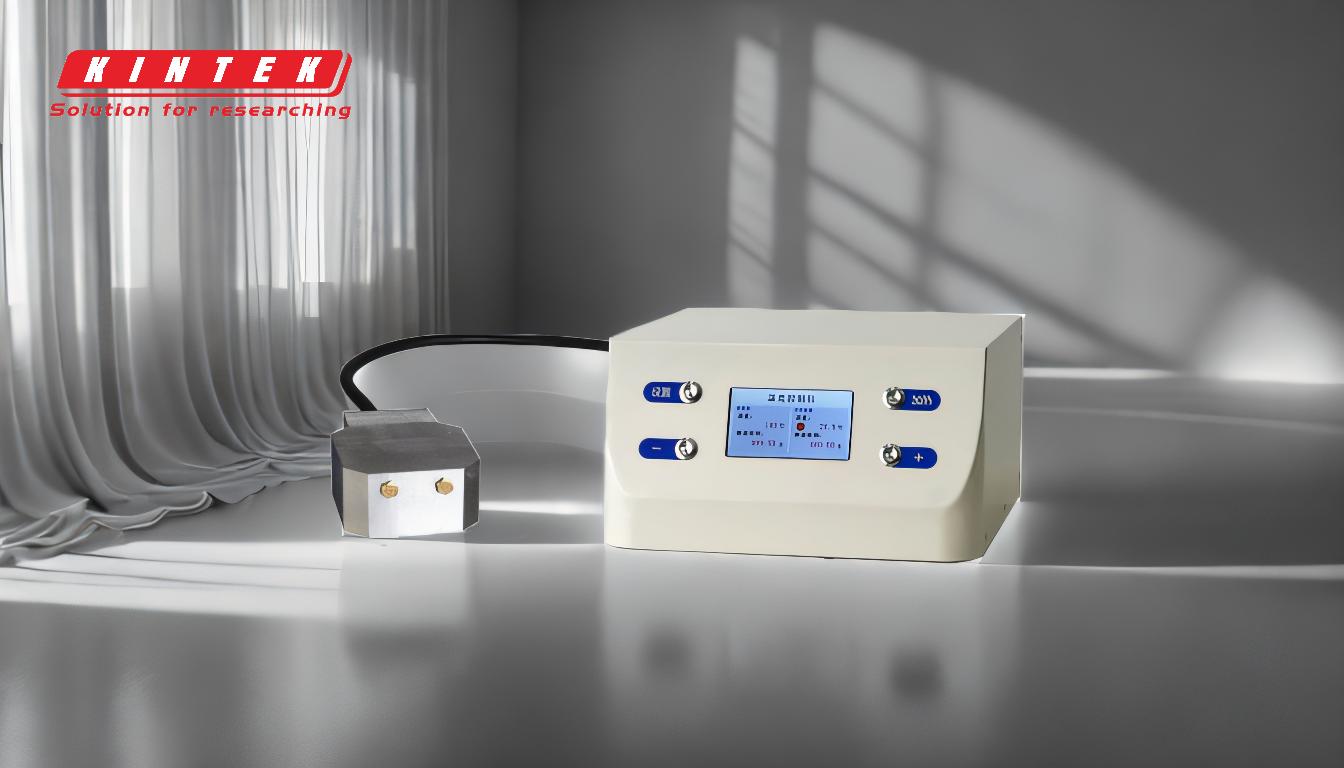
-
Definition of a Two-Plate Mold
- A two-plate mold is the simplest and most common type of injection mold.
- It consists of two main components: Side A (fixed) and Side B (movable).
- This design is widely used due to its simplicity and cost-effectiveness.
-
Structure and Components
-
Side A (Fixed Side):
- Attached to the stationary platen of the injection molding machine.
- Contains the sprue bushing, which directs molten plastic into the mold cavity.
-
Side B (Movable Side):
- Attached to the moving platen of the injection molding machine.
- Houses the ejection system, which pushes the finished part out of the mold after cooling.
-
Parting Line:
- The interface where Side A and Side B meet.
- Determines the shape and features of the final molded part.
-
Side A (Fixed Side):
-
How It Works
- The mold closes, and molten plastic is injected into the cavity through the sprue.
- After cooling, the mold opens, with Side B moving away from Side A.
- The ejection system on Side B pushes the part out of the mold.
- The mold then closes again for the next cycle.
-
Advantages of a Two-Plate Mold
-
Simplicity:
- Easy to design, manufacture, and maintain.
-
Cost-Effectiveness:
- Lower tooling costs compared to more complex molds.
-
Versatility:
- Suitable for a wide range of part geometries and materials.
-
Ease of Operation:
- Straightforward mold opening and closing process.
-
Simplicity:
-
Limitations of a Two-Plate Mold
-
Limited Complexity:
- Not ideal for parts with undercuts or complex geometries that require additional mold components.
-
Runner System:
- The runner system (which delivers plastic to the cavity) is often part of the final product, requiring trimming and potentially leading to material waste.
-
Limited Complexity:
-
Applications
- Commonly used for producing simple to moderately complex plastic parts.
- Examples include lids, containers, and other components with straightforward geometries.
-
Comparison with Other Mold Types
-
Three-Plate Mold:
- Allows for more complex part designs and automatic separation of the runner system.
- More expensive and complex to manufacture than a two-plate mold.
-
Hot Runner Mold:
- Eliminates the need for a runner system, reducing material waste.
- Higher initial cost and maintenance requirements compared to a two-plate mold.
-
Three-Plate Mold:
-
Considerations for Purchasers
-
Part Design:
- Ensure the part design is compatible with a two-plate mold structure.
-
Material Selection:
- Choose materials that work well with the mold's simplicity and cooling requirements.
-
Production Volume:
- Ideal for medium to high production volumes due to its durability and ease of use.
-
Cost Analysis:
- Evaluate the trade-offs between mold cost, part complexity, and production efficiency.
-
Part Design:
In summary, a two-plate mold is a fundamental and versatile tool in injection molding, offering simplicity, cost-effectiveness, and ease of use. While it may not be suitable for highly complex parts, it remains a reliable choice for many applications, making it a go-to option for manufacturers and purchasers alike.
Summary Table:
Aspect | Details |
---|---|
Definition | Simplest and most common type of injection mold. |
Components | Side A (fixed) and Side B (movable). |
Advantages | Simple design, cost-effective, versatile, and easy to operate. |
Limitations | Limited complexity and runner system waste. |
Applications | Ideal for simple to moderately complex parts like lids and containers. |
Comparison | Less complex and cheaper than three-plate or hot runner molds. |
Purchasing Tips | Consider part design, material, production volume, and cost trade-offs. |
Ready to optimize your injection molding process? Contact us today to learn more about two-plate molds!