An attritor is a type of grinding mill used primarily for reducing particle size and achieving fine grinding or dispersion of materials. It operates by agitating a mixture of grinding media (such as balls or beads) and the material to be ground within a rotating or vibrating chamber. This process generates high shear and impact forces, which break down the material into smaller particles. Attritors are widely used in industries such as ceramics, paints, pharmaceuticals, and metallurgy for applications like grinding, mixing, dispersing, and alloying. They are particularly valued for their ability to produce uniform particle sizes and their efficiency in processing both wet and dry materials.
Key Points Explained:
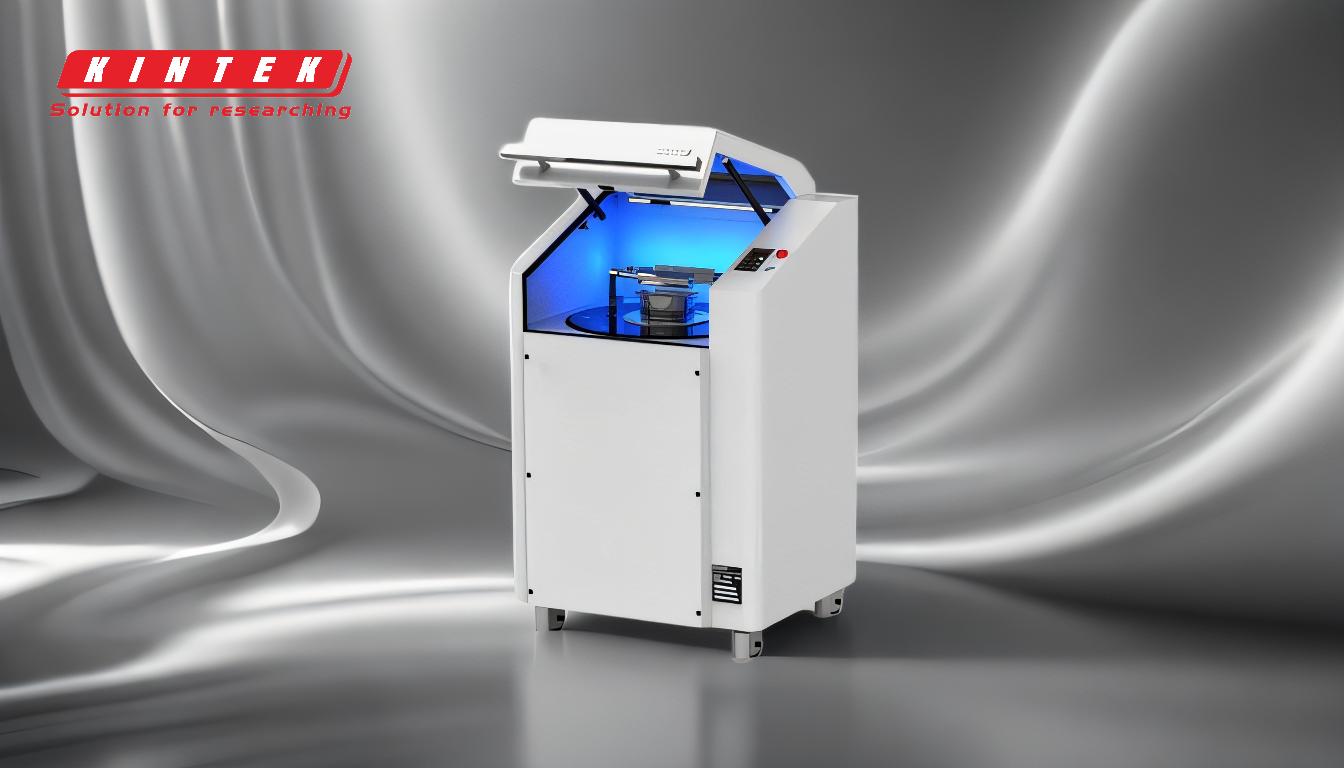
-
Definition and Function of an Attritor:
- An attritor is a grinding mill designed to reduce particle size and achieve fine grinding or dispersion.
- It uses grinding media (e.g., balls or beads) and mechanical agitation to generate shear and impact forces that break down materials.
-
Operating Mechanism:
- The attritor works by agitating a mixture of grinding media and the material within a rotating or vibrating chamber.
- The movement of the grinding media creates high-energy collisions and friction, which effectively grind the material.
-
Applications in Various Industries:
- Ceramics: Used for grinding raw materials and producing fine ceramic powders.
- Paints and Coatings: Employed for dispersing pigments and achieving uniform particle sizes.
- Pharmaceuticals: Utilized for grinding active pharmaceutical ingredients (APIs) to enhance bioavailability.
- Metallurgy: Applied in mechanical alloying and powder metallurgy to create fine metal powders.
-
Advantages of Using an Attritor:
- Uniform Particle Size: Produces consistent and fine particle sizes, which is crucial for many industrial applications.
- Versatility: Can handle both wet and dry grinding processes, making it suitable for a wide range of materials.
- Efficiency: High-energy grinding process reduces processing time and energy consumption compared to traditional mills.
-
Types of Attritors:
- Batch Attritors: Operate in a batch mode, suitable for small-scale production or laboratory use.
- Continuous Attritors: Designed for continuous processing, ideal for large-scale industrial applications.
- Vertical and Horizontal Attritors: Differ in orientation and are chosen based on specific processing requirements.
-
Key Considerations for Equipment Purchasers:
- Material Compatibility: Ensure the attritor is compatible with the materials to be processed (e.g., hardness, abrasiveness).
- Capacity and Throughput: Choose a model that meets production volume requirements.
- Energy Efficiency: Consider the energy consumption and operational costs.
- Maintenance and Durability: Evaluate the ease of maintenance and the durability of the grinding media and chamber.
-
Future Trends and Innovations:
- Automation and Control: Increasing use of automated systems for precise control over grinding parameters.
- Advanced Materials: Development of more durable and efficient grinding media.
- Sustainability: Focus on reducing energy consumption and environmental impact.
By understanding these key points, equipment purchasers can make informed decisions when selecting an attritor for their specific industrial needs.
Summary Table:
Key Aspect | Details |
---|---|
Function | Reduces particle size, achieves fine grinding, and disperses materials. |
Operating Mechanism | Agitates grinding media and material in a rotating/vibrating chamber. |
Applications | Ceramics, paints, pharmaceuticals, metallurgy. |
Advantages | Uniform particle size, versatility, efficiency. |
Types | Batch, continuous, vertical, horizontal. |
Key Considerations | Material compatibility, capacity, energy efficiency, maintenance. |
Future Trends | Automation, advanced materials, sustainability. |
Ready to enhance your material processing? Contact us today to find the perfect attritor for your needs!