Sputtering is a widely used thin film deposition technique in various industries, including semiconductors, optical devices, and solar panels. It involves the ejection of atoms from a target material onto a substrate through bombardment by high-energy particles. This process is highly precise and allows for the uniform deposition of materials like aluminum, copper, titanium, and indium tin oxide, which are critical in applications such as microelectronics and optoelectronics. Sputtering is typically performed in a vacuum chamber with an inert gas like argon, where a plasma is generated to dislodge atoms from the target material, forming a thin, consistent coating on the substrate.
Key Points Explained:
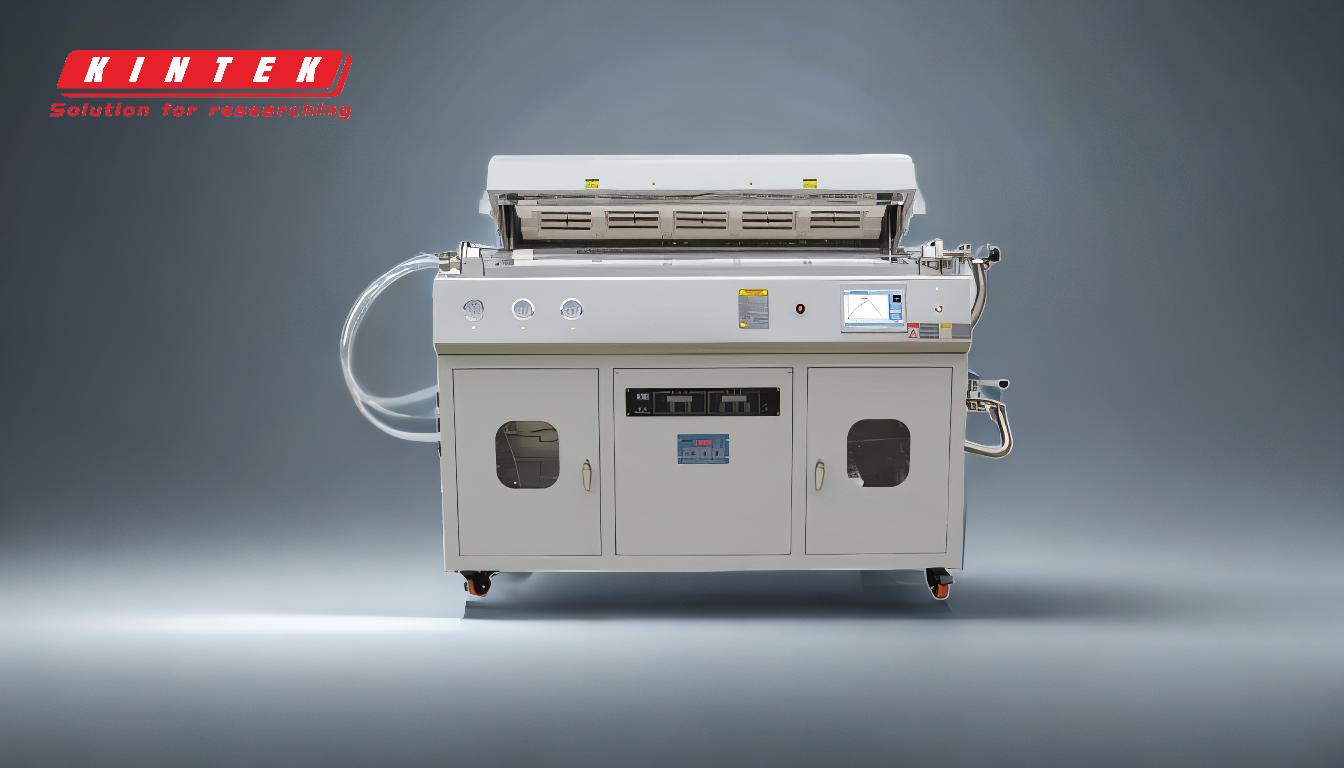
-
Definition of Sputtering:
- Sputtering is a physical vapor deposition (PVD) process used to deposit thin films of materials onto substrates. It involves the ejection of atoms from a target material due to bombardment by high-energy particles, typically ions of an inert gas like argon.
-
Mechanism of Sputtering:
- The process begins by introducing a controlled gas, usually argon, into a vacuum chamber. A cathode is electrically energized to generate a plasma, which ionizes the gas atoms. These ions are then accelerated toward the target material, dislodging atoms or molecules that form a vapor stream. This vapor stream deposits onto the substrate as a thin film.
-
Types of Sputtering:
- One common type is DC sputtering, where a direct current is used to energize the cathode and create the plasma. This method is widely used for depositing conductive materials like metals. Other types include RF sputtering (for non-conductive materials) and magnetron sputtering (for enhanced deposition rates).
-
Applications of Sputtering:
- Sputtering is used in the production of semiconductors, optical devices, solar panels, and disk drives. Materials like aluminum, copper, titanium, gold, and indium tin oxide are commonly deposited using this technique. For example, indium tin oxide is used in touchscreens and solar cells due to its conductive and transparent properties.
-
Advantages of Sputtering:
- The process allows for highly uniform and consistent thin film deposition, even on complex geometries. It is also versatile, capable of depositing a wide range of materials, including metals, alloys, and compounds like cadmium telluride and copper indium gallium selenide, which are used in solar cell manufacturing.
-
Comparison with Other Deposition Techniques:
- Unlike spin coating, which relies on centrifugal force to spread a liquid precursor over a substrate, sputtering is a dry process that does not involve solvents or liquid precursors. This makes it more suitable for applications requiring precise control over film thickness and composition.
-
Example of Sputtering in Action:
- A practical example of sputtering is the deposition of aluminum onto a silicon wafer to create conductive pathways in semiconductor devices. The aluminum target is bombarded with argon ions in a vacuum chamber, and the ejected aluminum atoms form a thin, uniform layer on the wafer surface.
By understanding these key points, one can appreciate the critical role sputtering plays in modern manufacturing and technology, enabling the production of high-performance materials and devices.
Summary Table:
Aspect | Details |
---|---|
Example | Deposition of aluminum onto silicon wafers for semiconductor devices. |
Process | High-energy argon ions bombard an aluminum target in a vacuum chamber. |
Result | Thin, uniform aluminum layer forms on the wafer surface. |
Applications | Semiconductors, optical devices, solar panels, and disk drives. |
Advantages | Precise, uniform deposition; suitable for complex geometries and materials. |
Want to learn more about sputtering and its applications? Contact our experts today!