Atomization in powder metallurgy is a critical process for producing metal powders, which are essential for various applications in manufacturing and engineering. The process involves breaking down molten metal into fine particles using either a gas or liquid spray. This method is widely used due to its efficiency and ability to produce high-quality powders in large quantities. Gas atomization typically uses inert gases like nitrogen, helium, or argon, while water atomization employs high-velocity water streams. Both techniques are significant in the production of metal powders, with each having its own advantages and applications.
Key Points Explained:
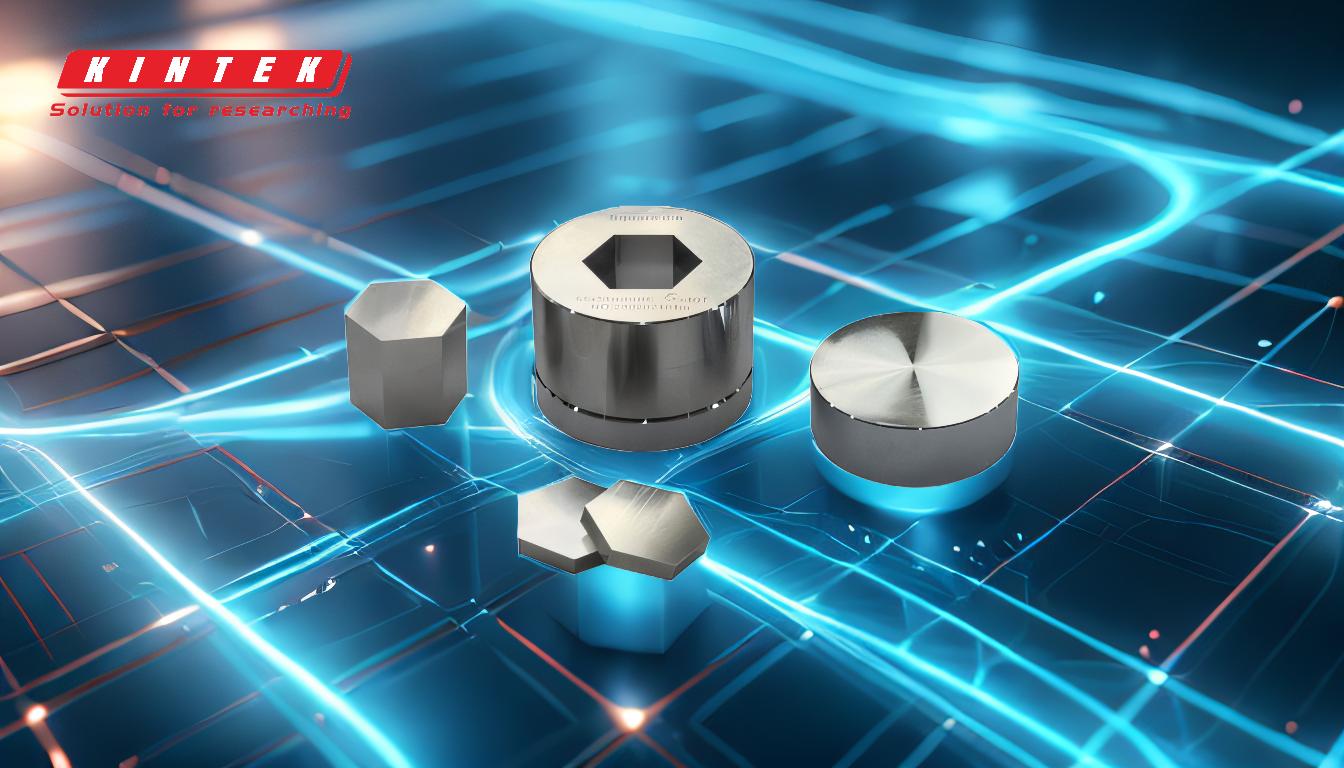
-
Definition of Atomization in Powder Metallurgy:
- Atomization is the process of converting molten metal into fine powder particles. This is achieved by spraying the molten metal with either a gas or liquid, which breaks it into small droplets that solidify into powder. This method is crucial for producing metal powders used in various industries.
-
Gas Atomization:
- Process: In gas atomization, inert gases such as nitrogen, helium, or argon are used to break up the stream of molten metal. The high-pressure gas stream disintegrates the molten metal into fine droplets, which then solidify into powder particles.
- Advantages: Gas atomization produces powders with a spherical shape, which is beneficial for applications requiring good flowability and packing density. The use of inert gases also minimizes oxidation, resulting in high-purity powders.
- Applications: This method is commonly used for producing powders for additive manufacturing, metal injection molding, and other high-performance applications.
-
Water Atomization:
- Process: Water atomization involves using a high-velocity water stream to break molten metal into particles. The water cools and solidifies the metal droplets rapidly, forming irregularly shaped powder particles.
- Advantages: Water atomization is cost-effective and capable of producing large quantities of powder in a single batch, ranging from 10 kg to 10,000 kg. The irregular shape of the particles can be advantageous for certain applications, such as pressing and sintering.
- Applications: This method is widely used for producing powders for conventional powder metallurgy, including automotive parts, tools, and other industrial components.
-
Comparison of Gas and Water Atomization:
- Particle Shape: Gas atomization typically produces spherical particles, while water atomization results in irregularly shaped particles.
- Purity: Gas atomization generally yields higher-purity powders due to the use of inert gases, whereas water atomization may introduce some oxidation.
- Cost: Water atomization is more cost-effective for large-scale production, while gas atomization is preferred for high-quality, specialized powders.
-
Importance in Powder Metallurgy:
- Atomization is the most significant method for producing metal powders, which are the building blocks for various powder metallurgy processes. The quality and characteristics of the powder directly influence the properties of the final product, making atomization a critical step in the manufacturing chain.
-
Future Trends:
- Advances in atomization technology are focused on improving powder quality, reducing costs, and expanding the range of materials that can be processed. Innovations such as ultrasonic atomization and hybrid methods combining gas and water atomization are being explored to meet the growing demands of advanced manufacturing techniques.
In summary, atomization in powder metallurgy is a vital process that enables the production of metal powders with specific characteristics tailored to various applications. Both gas and water atomization have their unique advantages and are chosen based on the desired powder properties and production requirements. Understanding these methods helps in selecting the appropriate technique for specific manufacturing needs, ensuring the production of high-quality components.
Summary Table:
Aspect | Gas Atomization | Water Atomization |
---|---|---|
Particle Shape | Spherical | Irregular |
Purity | High (minimizes oxidation) | Lower (some oxidation) |
Cost | Higher | Cost-effective for large-scale production |
Applications | Additive manufacturing, metal injection molding | Automotive parts, tools, industrial components |
Discover the best atomization method for your needs—contact our experts today!