Comminution in sampling refers to the process of reducing the particle size of materials such as ore, rock, coal, or other substances through breaking, crushing, or grinding. This process is essential in mineral processing as it helps liberate valuable minerals trapped within waste rock, making them accessible for further processing. Comminution is a critical step in ensuring the accuracy and representativeness of samples, as smaller particle sizes allow for more uniform mixing and easier extraction of the desired components.
Key Points Explained:
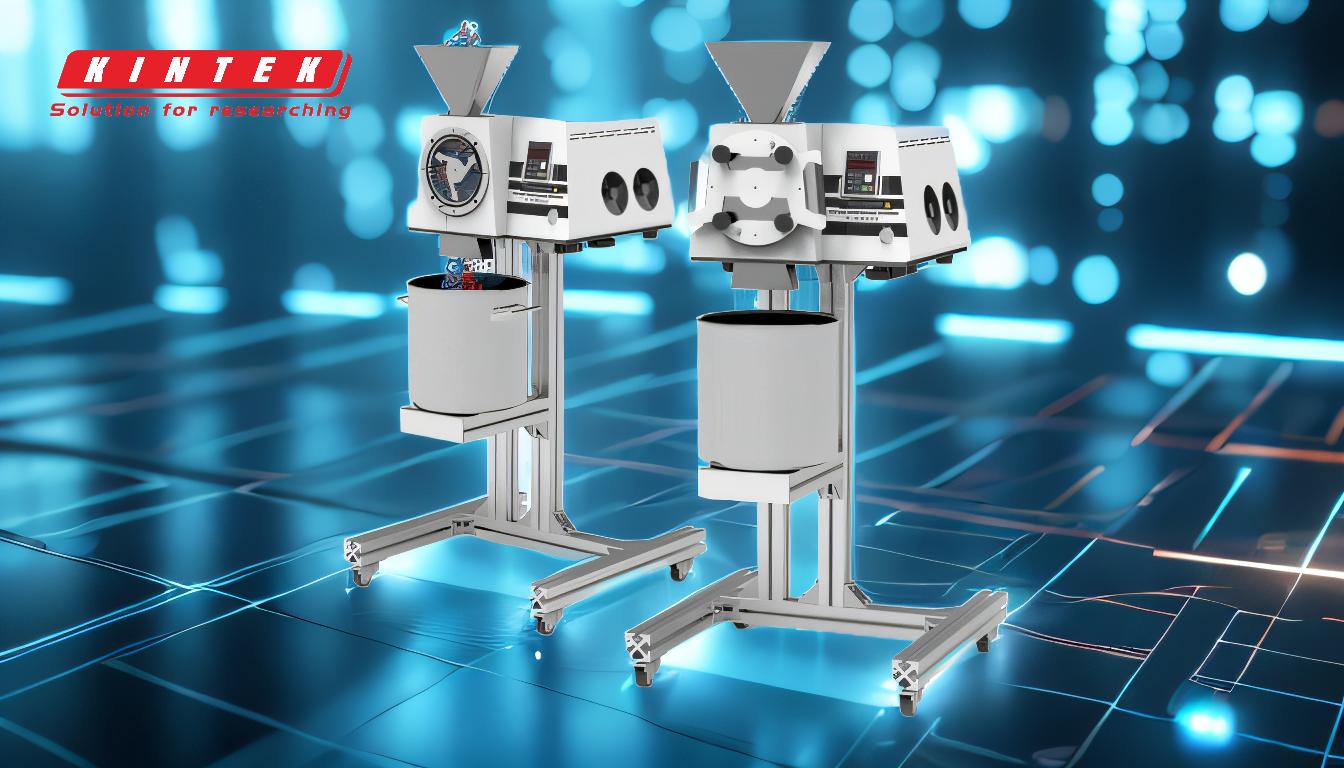
-
Definition of Comminution:
- Comminution is the process of reducing the size of particles in a material through mechanical means such as breaking, crushing, or grinding.
- It is a fundamental step in mineral processing and sampling, as it prepares the material for further analysis or extraction.
-
Purpose of Comminution in Sampling:
- Liberation of Valuable Minerals: One of the primary purposes of comminution is to liberate valuable minerals that are locked within waste rock. By reducing the particle size, the minerals become more accessible for extraction.
- Uniform Sampling: Comminution ensures that the sample is more homogeneous, which is crucial for obtaining accurate and representative results during analysis.
- Improved Processing Efficiency: Smaller particle sizes can lead to more efficient processing in subsequent steps, such as flotation or leaching.
-
Methods of Comminution:
- Crushing: This involves using mechanical force to break down larger particles into smaller ones. Crushing is typically the first step in the comminution process.
- Grinding: After crushing, grinding further reduces the particle size to a finer consistency. This is often done using ball mills or other grinding equipment.
- Breaking: This method involves applying force to fracture the material along its natural lines of weakness, such as cleavage planes in minerals.
-
Importance in Mineral Processing:
- Enhanced Recovery Rates: By reducing the particle size, comminution increases the surface area of the material, which can enhance the recovery rates of valuable minerals during processing.
- Energy Consumption: Comminution is often one of the most energy-intensive steps in mineral processing. Optimizing this process can lead to significant energy savings.
- Environmental Impact: Efficient comminution can reduce the environmental impact of mining operations by minimizing waste and improving the recovery of valuable materials.
-
Challenges in Comminution:
- Energy Efficiency: Achieving the desired particle size while minimizing energy consumption is a significant challenge in comminution.
- Equipment Wear: The process can cause significant wear and tear on equipment, leading to increased maintenance costs.
- Particle Size Distribution: Ensuring a consistent particle size distribution is crucial for downstream processing and can be difficult to achieve.
-
Applications Beyond Mineral Processing:
- Coal Preparation: Comminution is used in coal preparation to reduce the size of coal particles, making it easier to separate coal from impurities.
- Recycling: In recycling operations, comminution is used to break down materials such as plastics, metals, and glass for further processing.
- Pharmaceuticals: In the pharmaceutical industry, comminution is used to reduce the size of active ingredients to ensure uniform distribution in medications.
In summary, comminution is a vital process in sampling and mineral processing, serving to liberate valuable minerals, ensure uniform sampling, and improve processing efficiency. While it presents challenges such as energy consumption and equipment wear, its benefits in terms of enhanced recovery rates and environmental impact make it an indispensable step in many industries.
Summary Table:
Aspect | Details |
---|---|
Definition | Reducing particle size through breaking, crushing, or grinding. |
Purpose | Liberate minerals, ensure uniform sampling, and improve processing efficiency. |
Methods | Crushing, grinding, and breaking. |
Importance | Enhances recovery rates, reduces energy consumption, and minimizes waste. |
Challenges | Energy efficiency, equipment wear, and particle size distribution. |
Applications | Mineral processing, coal preparation, recycling, and pharmaceuticals. |
Discover how comminution can optimize your sampling process—contact our experts today!