Direct current (DC) sputtering is a widely used thin-film deposition technique in the field of Physical Vapor Deposition (PVD). It involves bombarding a target material (cathode) with ionized gas molecules, typically argon, in a vacuum environment. This bombardment causes atoms to be ejected from the target surface, which then condense and form a thin film on a substrate (anode). DC sputtering is particularly suitable for conductive materials due to the direct flow of electrons toward the anode. It is a cost-effective and straightforward method, making it popular in industries such as semiconductors, jewelry, and optical components. However, it is not suitable for non-conductive materials due to electron flow limitations.
Key Points Explained:
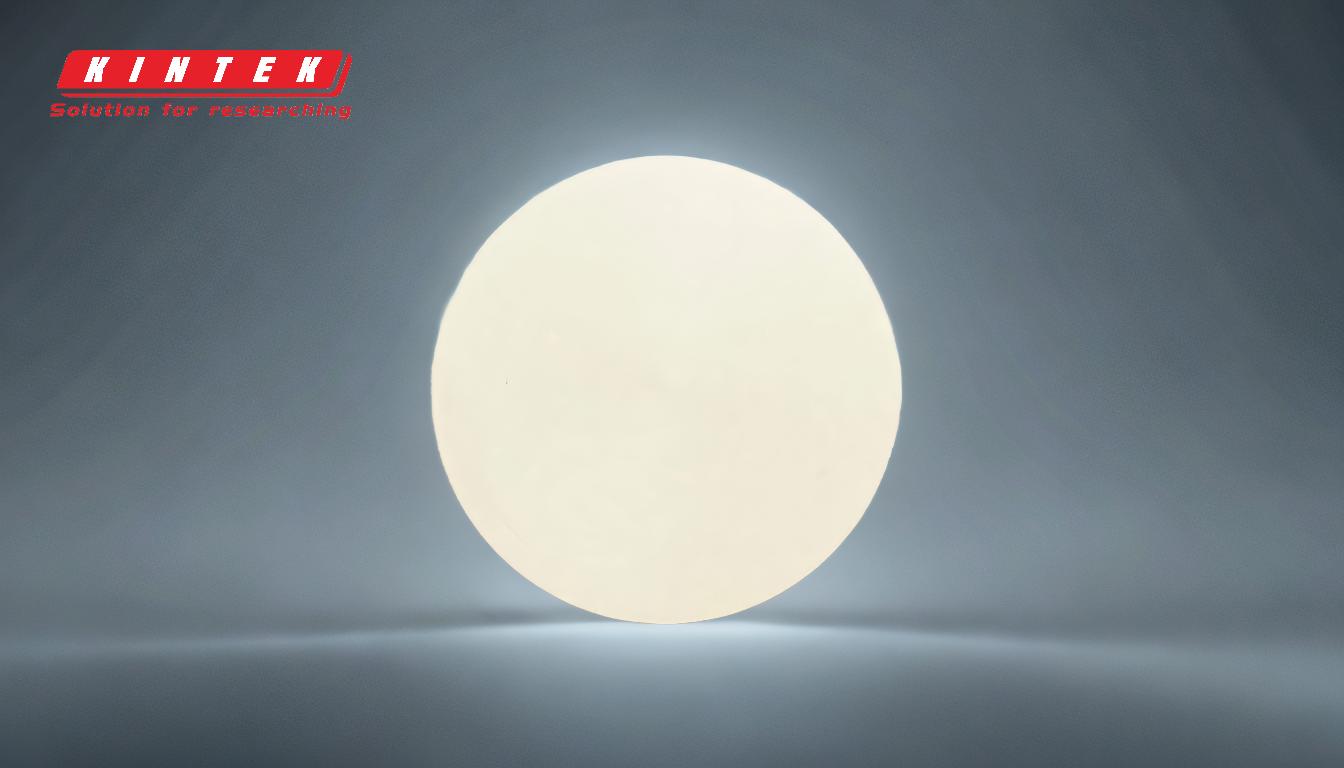
-
Definition of DC Sputtering:
- DC sputtering is a type of Physical Vapor Deposition (PVD) technique.
- It uses a constant DC voltage applied between a target material (cathode) and a substrate (anode).
- Ionized gas, typically argon, bombards the target, causing atoms to be ejected and deposited onto the substrate.
-
Mechanism of DC Sputtering:
- The process occurs in a vacuum chamber to maintain a controlled environment.
- Argon gas is introduced at a specific pressure and voltage, creating a plasma.
- Ions in the plasma collide with the target material, transferring energy and causing atoms to be "sputtered" off the surface.
- These sputtered atoms travel through the plasma and condense on the substrate, forming a thin film.
-
Key Components:
- Target Material (Cathode): The material to be deposited, typically a conductive metal.
- Substrate (Anode): The surface onto which the thin film is deposited.
- Vacuum Chamber: Provides a controlled environment with low pressure.
- Argon Gas: The inert gas used to create the plasma and ionize the target material.
-
Advantages of DC Sputtering:
- Cost-Effective: It is one of the most basic and inexpensive PVD techniques.
- Wide Applicability: Suitable for depositing conductive materials like metals.
- High-Quality Films: Produces uniform and high-quality thin films with good adhesion to the substrate.
-
Limitations of DC Sputtering:
- Material Constraints: Not suitable for non-conductive materials due to the inability to sustain electron flow.
- Target Erosion: Continuous bombardment can lead to target erosion, requiring periodic replacement.
- Process Complexity: Requires precise control of vacuum pressure, gas flow, and voltage.
-
Applications of DC Sputtering:
- Semiconductor Industry: Used for depositing metal layers in integrated circuits.
- Jewelry: Coating jewelry with precious metals for aesthetic and protective purposes.
- Optical Components: Creating anti-reflective and protective coatings on lenses and mirrors.
- Decorative Coatings: Applying thin films for decorative purposes on various surfaces.
-
Comparison with Other Sputtering Techniques:
- DC Sputtering vs. RF Sputtering: DC sputtering is simpler and more cost-effective but limited to conductive materials. RF sputtering can handle non-conductive materials but is more complex and expensive.
- DC Sputtering vs. Magnetron Sputtering: Magnetron sputtering uses magnetic fields to enhance plasma density, increasing deposition rates and efficiency compared to basic DC sputtering.
-
Process Parameters:
- Voltage: The applied DC voltage determines the energy of the ions bombarding the target.
- Pressure: The vacuum pressure affects the mean free path of the sputtered atoms and the overall deposition rate.
- Gas Flow Rate: The flow rate of argon gas influences plasma formation and sputtering efficiency.
In summary, DC sputtering is a fundamental and versatile PVD technique for depositing thin films of conductive materials. Its simplicity, cost-effectiveness, and ability to produce high-quality coatings make it a preferred choice in various industries. However, its limitations with non-conductive materials and target erosion necessitate careful consideration in specific applications.
Summary Table:
Aspect | Details |
---|---|
Definition | A PVD technique using DC voltage to deposit thin films on conductive materials. |
Mechanism | Argon plasma bombards a target, ejecting atoms that form a film on a substrate. |
Key Components | Target (cathode), substrate (anode), vacuum chamber, argon gas. |
Advantages | Cost-effective, wide applicability, high-quality films. |
Limitations | Not suitable for non-conductive materials, target erosion, process complexity. |
Applications | Semiconductors, jewelry, optical components, decorative coatings. |
Comparison | Simpler than RF sputtering, less efficient than magnetron sputtering. |
Process Parameters | Voltage, pressure, gas flow rate. |
Discover how DC sputtering can enhance your thin-film processes—contact our experts today!