Ceramic powder refers to finely ground particles of ceramic materials, which are inorganic, non-metallic solids typically composed of metal oxides, carbides, nitrides, or silicates. These powders are the fundamental building blocks used in the production of ceramic products, ranging from everyday items like tiles and tableware to advanced applications such as electronic components, biomedical implants, and aerospace materials. Ceramic powders are characterized by their high melting points, hardness, and chemical stability, making them suitable for demanding environments. They are processed through techniques like sintering, pressing, or casting to form solid ceramic objects with desired properties. The particle size, shape, and purity of ceramic powders significantly influence the final product's performance, making their production and handling a critical aspect of ceramic engineering.
Key Points Explained:
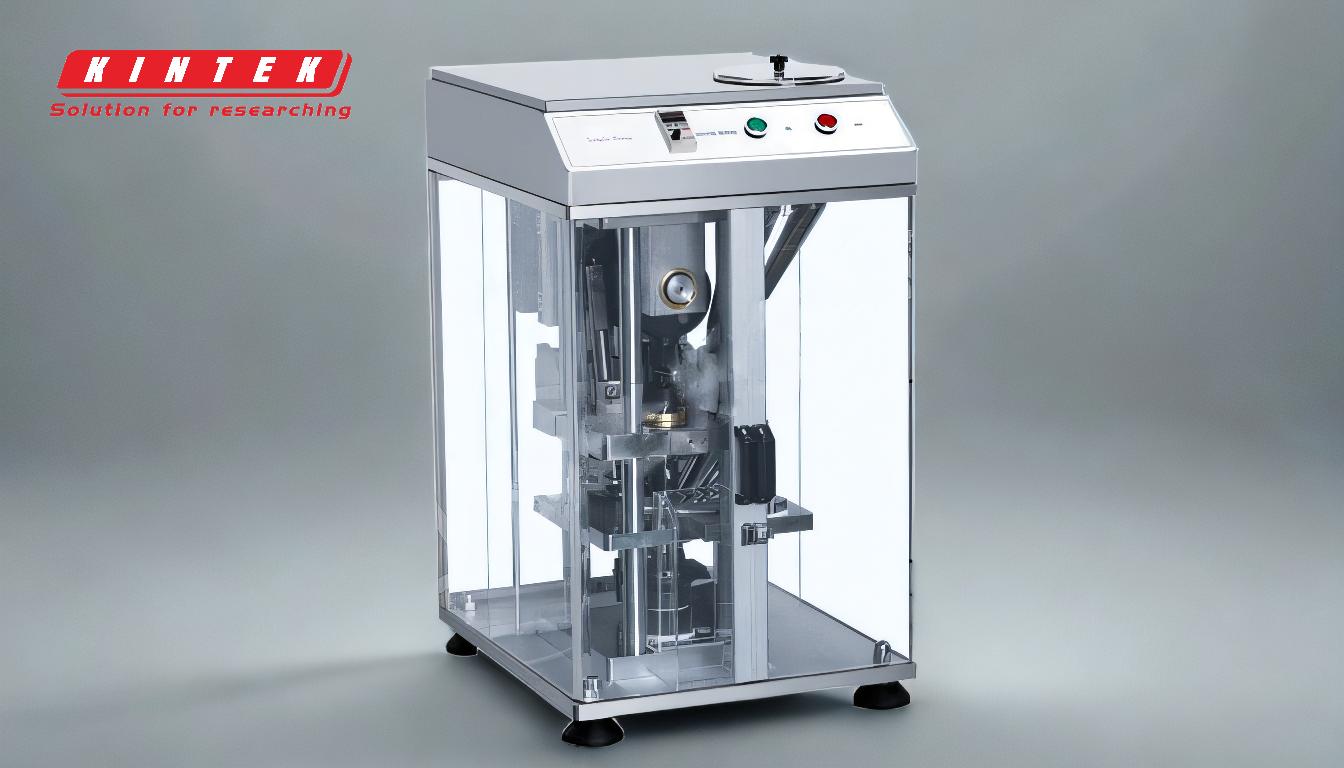
-
Definition and Composition of Ceramic Powder:
- Ceramic powders are finely ground particles of inorganic, non-metallic materials, often composed of metal oxides (e.g., alumina, zirconia), carbides, nitrides, or silicates.
- These materials are chosen for their unique properties, such as high melting points, hardness, and resistance to wear and corrosion.
-
Applications of Ceramic Powders:
- Everyday Products: Used in the production of tiles, tableware, and sanitaryware due to their durability and aesthetic appeal.
- Advanced Applications: Employed in high-tech industries for electronic components (e.g., capacitors, insulators), biomedical implants (e.g., dental crowns, bone replacements), and aerospace materials (e.g., heat shields, engine components).
- Industrial Uses: Utilized in refractory materials, cutting tools, and abrasives because of their thermal and mechanical stability.
-
Properties of Ceramic Powders:
- High Melting Points: Ceramic powders can withstand extreme temperatures, making them ideal for high-temperature applications.
- Hardness and Wear Resistance: Their inherent hardness makes them suitable for abrasive and cutting applications.
- Chemical Stability: Ceramic powders are resistant to chemical reactions, ensuring longevity in harsh environments.
-
Processing Techniques:
- Sintering: A process where ceramic powders are heated below their melting point to bond particles together, forming a solid structure.
- Pressing: Powders are compacted under high pressure to form a green body, which is then sintered.
- Casting: Ceramic powders are mixed with a liquid to form a slurry, which is then poured into molds and solidified.
-
Importance of Particle Characteristics:
- Particle Size: Smaller particles generally lead to denser and stronger final products.
- Particle Shape: Spherical particles are often preferred for uniform packing and flowability during processing.
- Purity: High-purity powders are essential for applications requiring precise mechanical, electrical, or thermal properties.
-
Challenges in Ceramic Powder Production:
- Uniformity: Achieving consistent particle size and shape is critical for reliable performance.
- Contamination: Impurities can degrade the properties of the final ceramic product.
- Cost: High-purity powders and advanced processing techniques can be expensive.
-
Future Trends in Ceramic Powders:
- Nanotechnology: Development of nano-sized ceramic powders for enhanced properties and new applications.
- Sustainability: Focus on eco-friendly production methods and recyclable ceramic materials.
- Customization: Tailoring ceramic powders for specific applications through advanced material design and processing techniques.
By understanding the composition, properties, and processing of ceramic powders, manufacturers and engineers can optimize their use in various applications, ensuring high-performance and durable ceramic products.
Summary Table:
Aspect | Details |
---|---|
Definition | Finely ground particles of inorganic, non-metallic materials. |
Composition | Metal oxides, carbides, nitrides, or silicates. |
Properties | High melting points, hardness, chemical stability. |
Applications | Tiles, tableware, electronic components, biomedical implants, aerospace. |
Processing Techniques | Sintering, pressing, casting. |
Key Challenges | Uniformity, contamination, cost. |
Future Trends | Nanotechnology, sustainability, customization. |
Ready to explore how ceramic powders can enhance your projects? Contact us today for expert guidance!