Sputter coating is a critical sample preparation technique used in scanning electron microscopy (SEM) to apply an ultra-thin layer of conductive metal (e.g., gold, platinum, or iridium) onto non-conductive or poorly conductive specimens. This process prevents charging effects, enhances secondary electron emission, and improves the signal-to-noise ratio, resulting in higher-quality SEM images. It is particularly important for beam-sensitive materials and non-conductive samples, as it protects them from damage and ensures accurate imaging. The typical thickness of sputtered films ranges from 2 to 20 nanometers, providing a conductive layer without obscuring the sample's surface details.
Key Points Explained:
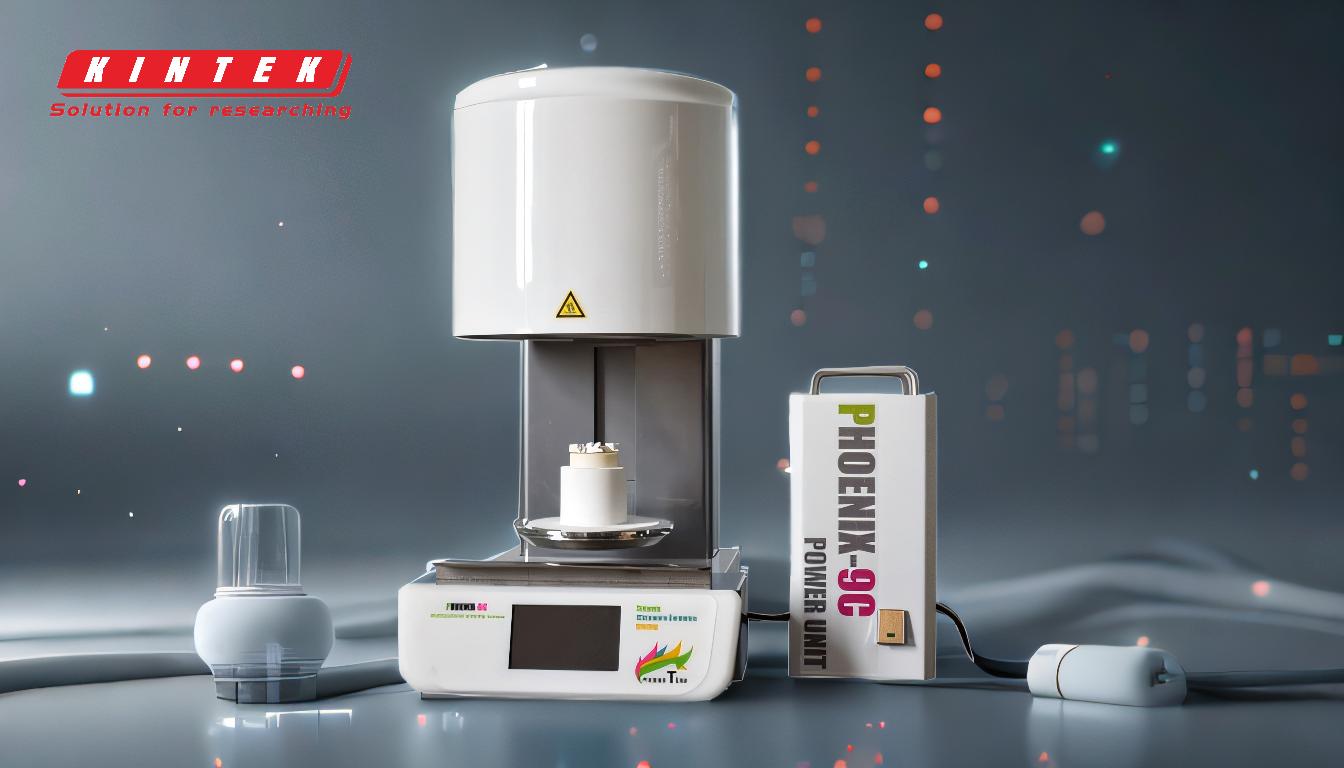
-
Purpose of Sputter Coating in SEM:
- Preventing Charging Effects: Non-conductive or poorly conductive samples can accumulate electrons when exposed to the SEM's electron beam, leading to charging effects. These effects distort the image and make analysis difficult. Sputter coating provides a conductive layer that dissipates these electrons, preventing charging.
- Enhancing Secondary Electron Emission: The conductive coating increases the emission of secondary electrons from the sample's surface, which are crucial for creating high-resolution SEM images.
- Improving Signal-to-Noise Ratio: By reducing charging and enhancing electron emission, sputter coating improves the clarity and quality of SEM images, making it easier to observe fine details.
-
Materials Used for Sputter Coating:
- Common Metals: Gold, gold/palladium, platinum, silver, chromium, and iridium are commonly used due to their excellent conductivity and ability to form uniform thin films.
- Selection Criteria: The choice of metal depends on factors such as the sample's properties, the desired imaging resolution, and the need to minimize interference with the sample's surface features.
-
Process of Sputter Coating:
- Transformation of Solid Material: The sputter coating process involves transforming a solid metal target into a fine spray of microscopic particles using a high-energy plasma. These particles deposit onto the sample, forming a thin, uniform conductive layer.
- Thickness Control: The thickness of the sputtered film is carefully controlled, typically ranging from 2 to 20 nanometers. This ensures conductivity without obscuring the sample's surface details.
- Heat Management: The process generates heat, which is managed using specialized cooling systems to prevent damage to sensitive samples.
-
Applications of Sputter Coating:
- Non-Conductive Materials: Samples such as polymers, ceramics, and biological tissues are often non-conductive and require sputter coating for effective SEM imaging.
- Beam-Sensitive Materials: Sputter coating protects beam-sensitive materials (e.g., organic compounds) from damage caused by the electron beam.
- High-Resolution Imaging: The technique is essential for achieving high-resolution images of challenging samples, enabling detailed analysis of surface morphology and structure.
-
Advantages of Sputter Coating:
- Improved Image Quality: By reducing charging and enhancing electron emission, sputter coating significantly improves the quality and clarity of SEM images.
- Versatility: It can be used for a wide range of materials, including delicate and beam-sensitive samples.
- Precision: The ability to control the thickness of the coating ensures that the sample's surface features remain visible and undisturbed.
-
Limitations and Considerations:
- Potential Artifacts: Improper coating thickness or uneven application can introduce artifacts, such as granularity or masking of fine surface details.
- Sample Compatibility: Some samples may be sensitive to the metals used in sputter coating, requiring careful selection of the coating material.
- Cost and Equipment: Sputter coating requires specialized equipment and can add to the overall cost and complexity of SEM sample preparation.
In summary, sputter coating is an indispensable technique in SEM sample preparation, particularly for non-conductive and beam-sensitive materials. It ensures high-quality imaging by preventing charging, enhancing electron emission, and improving the signal-to-noise ratio. The process involves depositing a thin, uniform layer of conductive metal onto the sample, with careful control of thickness and heat management to preserve surface details. While it offers significant advantages, proper application and material selection are crucial to avoid artifacts and ensure accurate results.
Summary Table:
Aspect | Details |
---|---|
Purpose | Prevents charging, enhances electron emission, improves signal-to-noise ratio |
Common Materials | Gold, platinum, iridium, gold/palladium, silver, chromium |
Coating Thickness | 2 to 20 nanometers |
Applications | Non-conductive materials, beam-sensitive samples, high-resolution imaging |
Advantages | Improved image quality, versatility, precise thickness control |
Limitations | Potential artifacts, sample compatibility, cost and equipment requirements |
Need sputter coating solutions for your SEM imaging? Contact our experts today to learn more!